Sillimanite bricks for glass kilns are refractory bricks mainly made of sillimanite minerals. Sillimanite is converted into mullite and free silica after high-temperature calcination. It is generally produced by the high-temperature firing method and slurry casting method. Its physical and chemical properties are better than those of high-alumina bricks, with refractoriness of 1770-1830 °C, and a load softening starting point of 1500-1650 °C. It is mainly used for the molding of liquid holes in glass pool kilns, blast furnace lining, furnace throat, and ceramic industrial kiln furniture.
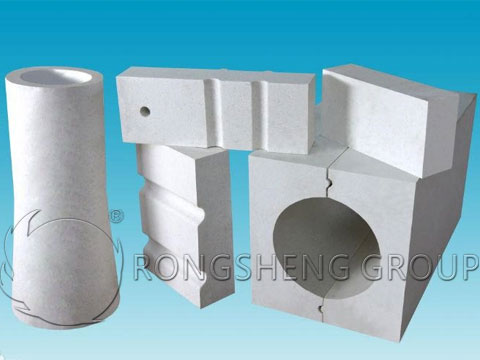
Sillimanite is a natural high-grade refractory mineral, which has the characteristics of low thermal expansion rate, resistance to corrosion from metallurgical slag and various glass liquids, and good high temperature wear resistance. Its physical and chemical properties are better than those of high-alumina bricks, with refractoriness of 1770-1830 °C, and a load softening starting point of 1500-1650 °C. It has good thermal stability at high temperatures, resists the erosion and erosion of glass liquid, and has little pollution to the glass liquid.
Types of Sillimanite Bricks for Glass Kilns
Sillimanite products include forehearth bricks, flow troughs, rotating tubes, feed basins, feed bowls, stirring paddles, and punches. Barrel, fire, slag-blocking bricks, gate bricks, and material basin cover bricks. There are hundreds of products and hundreds of specifications, such as opening bricks, burning nozzle bricks, beam bricks, cover bricks, muffle furnace bricks, etc.
- Material bowls are mainly used in glass kilns. The material bowl has good thermal stability at high temperatures, resists the erosion and erosion of the glass liquid, and has little pollution to the glass liquid.
- The material basin has good thermal stability at high temperatures, resists the erosion and erosion of the glass liquid, and has little pollution to the glass liquid. Can be processed into any size.
- The punch has high strength, high density, good thermal shock stability, and good resistance to glass solution erosion. For molten glass, it has high refractoriness and long service life. It can be replaced in a hot state without preheating, which can effectively reduce the bubbles of the molten glass and prolong the service life of the furnace. Mainly used in glass furnaces.
- The stirring paddle is mainly used to stir the glass liquid. The stirring paddle has the advantages of preventing the glass liquid from condensing and promoting the flow of the glass liquid to make it uniform. The sillimanite stirring paddle has the characteristics of resisting the erosion and scouring of the glass liquid and having little pollution to the glass liquid.
- Barrels are mainly used in glass furnaces. The barrel has the characteristics of good high-temperature thermal stability, resistance to glass liquid erosion and erosion, and little pollution of glass liquid. There are various types of barrels, which can also be made according to the drawings according to the needs of customers.
Characteristics of Sillimanite Bricks for Glass Kilns
Sillimanite bricks are made by adding a certain proportion of sillimanite raw materials to the ingredients of high alumina bricks, so as to improve the thermal shock resistance of the products. In particular, the high-temperature creep rate of the product is reduced. This kind of brick is also called low creep high alumina brick. It is widely used in key parts such as blast furnaces, hot blast stoves, and torpedo tanks.
- Thermal expansion rate
Sillimanite is a natural high-grade refractory mineral, which has a low thermal expansion rate.
- The high softening temperature under load
Load softening start point 1500 ~ 1650 ℃. It has good thermal stability at high temperatures.
- Strong slag resistance
Resist the corrosion of metallurgical slag and various glass liquids.
- Chemical resistance
It has the characteristics of little pollution to the glass liquid.