1, Pre-reduction Furnace
The furnace mostly uses a shaft furnace and fluidized bed.
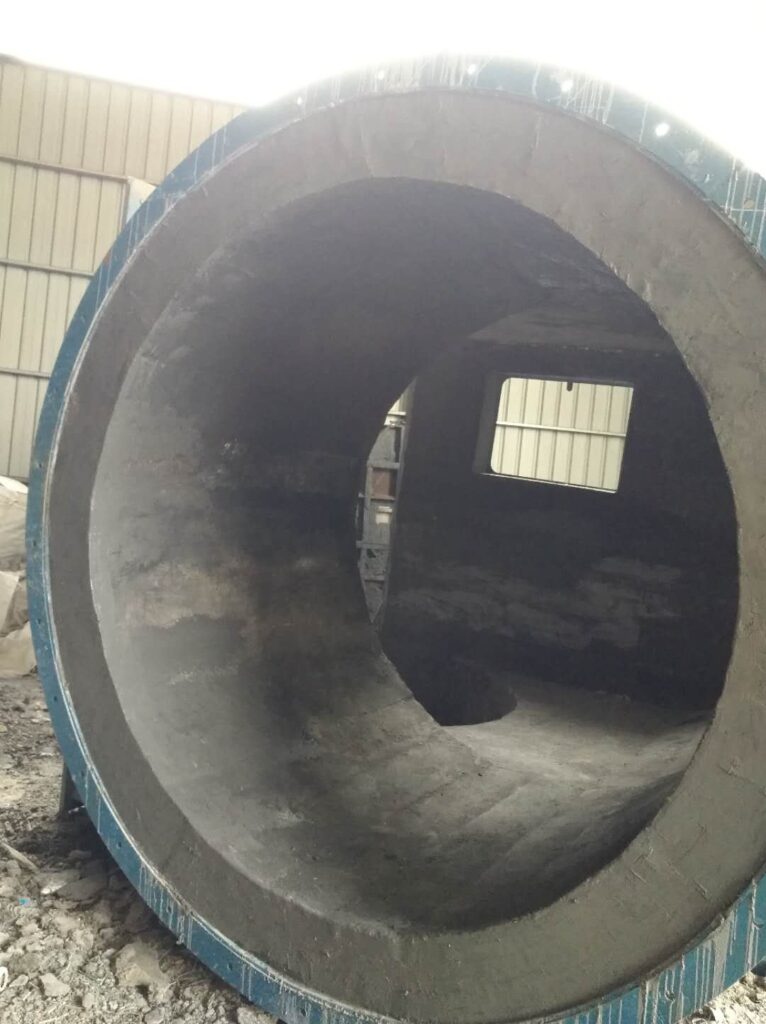
The refractory material of the pre-reduction furnace enters the furnace from the upper part. Due to the heating and reduction of the high-temperature gas flow, the temperature of the refractory material is from top to bottom.
Gradually increase, the temperature in the upper part of the refractory furnace is 300~400C, and the temperature in the middle of the furnace is 400~700C, reaching the lower part of the furnace
The temperature is 700~900C. At the same time, the refractory material in the furnace is always subject to the mechanical erosion of the refractory material and the erosion of the high-temperature gas flow, and the high-temperature destruction by thermal shock.
- Final Reduction Furnace
This furnace mostly uses a shaft furnace, smelting reduction furnaces, electric furnaces, or converters.
The pre-reduced refractory material enters the upper part of the reduction furnace, its temperature is 800~900C, and begins to soften, reaching the middle of the furnace.
The temperature is 900~1100C, and as the temperature continues to rise, the temperature reaching the lower part of the furnace is about 1500C. The upper part of the furnace Refractory materials is subject to mechanical scouring, scouring of high-temperature gas flow, thermal shock damage, and alkali metal erosion. The middle part of the furnace is refractory material that is subject to slag iron erosion, gas flow erosion, and alkali metal erosion. The refractory material under the furnace bears slag iron erosion and flow.
Dynamic erosion, thermal stress damage, and alkali metal erosion.