Compared with magnesia chrome bricks, dolomite bricks have their obvious advantages and disadvantages. Dolomite bricks contain a large amount of free CaO, so they are susceptible to erosion by clinker melt and alkali salts, especially when there is too much SO3 in the kiln gas and kiln materials. At 600~800℃, dolomite bricks will also absorb CO2 and undergo recarbonation. The large amount of free CaO also makes it easier to absorb moisture than other alkaline bricks.
The above are the shortcomings of dolomite bricks, but compared with other alkaline bricks, it has the outstanding points of being easy to hang the kiln skin and easy to maintain the kiln skin. Under the protection of reliable kiln skin, the service life is greatly extended, and the low price brings an extremely favorable price/life ratio. In particular, it avoids the chromium pollution caused by magnesia-chromium bricks to the environment, so it continues to arouse people’s interest.
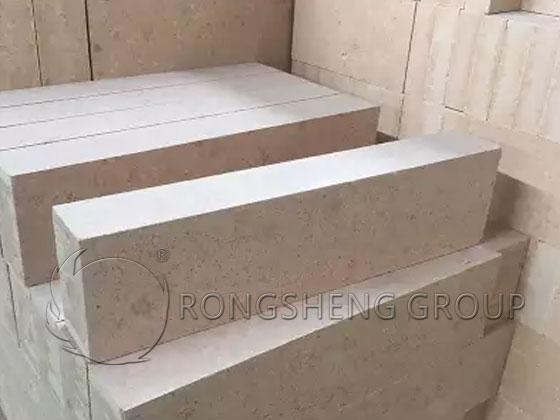
How to Improve the Performance of Dolomite Bricks?
In recent years, the volume density of the produced dolomite bricks has been increased by increasing the sintering temperature of MgO, and the size of the pores in the bricks has been reduced. Measures such as incorporating magnesia aggregates to appropriately increase the magnesium content, soaking bricks in oil, and using reliable moisture-proof packaging methods. It not only fundamentally improves and suppresses the shortcomings of this brick, but also further develops its advantages. It is widely used in the firing zone of precalciner rotary kilns. In Western Europe and North America, where dolomite resources are abundant, dolomite bricks have replaced magnesia-chromium bricks and occupy the dominant position in the lining of the precalcining kiln firing zone. Dolomite bricks have also been used in the firing belt of large-scale precalcining rotary kilns in my country. However, there are still problems with this brick during transportation and storage, so its use is not widespread and there are few manufacturers.
Zirconium-Containing Dolomite Bricks
The main components of the rotary kiln skin are tricalcium silicate (3CaO·SiO2, melting point 1900°C) and clinonotlite (2CaO·SiO2, melting point 2310°C). A stable kiln skin protects the kiln lining from chemical attack and provides a barrier to improve the thermal insulation properties of the kiln lining. Therefore, during the clinker calcining process, the protection of the kiln skin is crucial.
If the kiln skin falls off, the refractory bricks will be exposed and directly in contact with new clinker, high-temperature flames, and high-speed hot airflow. Withstanding the thermochemical erosion of high-temperature airflow and materials, the silicate phase in the clinker enters the brick lining, which will accelerate the damage and peeling of the refractory bricks. At the same time, with the widespread development of rotary kiln co-processing domestic waste and various industrial waste projects, the composition of materials entering the kiln has changed significantly. Harmful components in the waste, such as chlorine, sulfur, and various heavy metals, enter the kiln along with the raw fuel and accelerate the erosion of the refractory materials.
Since the CaO in dolomite bricks easily reacts with 2CaO·SiO2 in the clinker to form 3CaO·SiO2, which has good kiln skin hanging properties, dolomite bricks are suitable for use in the firing zone of the rotary kiln. However, if the SO2 content in the materials in the kiln is high, it will easily react with CaO in the dolomite bricks to form CaSO4 or CaS, causing the refractory bricks to expand in volume and cause structural spalling.
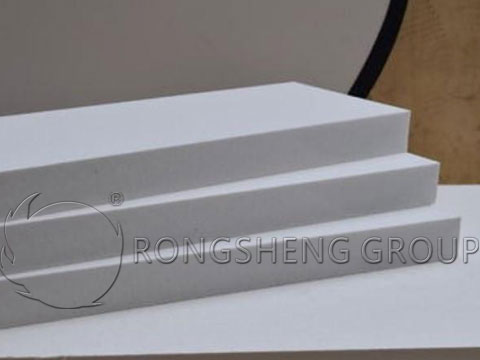
Zirconium-containing bricks are made by adding a small amount of ZrO2 when making dolomite bricks. ZrO2 forms zirconate with the lime phase in dolomite. Not only does the dolomite brick have improved refractoriness (2340°C), but it can also form micro-cracks during calcining. The formation of micro-cracks can limit the expansion of stress cracks in the bricks, reduce the thermal spalling of the refractory bricks, and improve the thermal shock stability of the refractory bricks. And the improvement of anti-flaking performance can better protect the stability of the kiln skin. Therefore, the microcracks generated by this reaction can improve the thermal shock stability and hydration resistance of dolomite bricks. At the same time, the bulk density of dolomite bricks is about 5% lower than that of magnesia-chrome bricks, and the brick thickness can be appropriately reduced by about 10%, which makes dolomite bricks more cost-effective.
Dolomite Bricks Used in Argon Oxygen Furnaces and Their Advantages
In the past, alkaline oxygen-blown converters were the main application areas for dolomite refractory materials. After the 1980s, its main application areas shifted to out-of-furnace refining and different types of ladles. In order to balance the bricks used in furnace linings, the main trend is towards increasing the absorption of slag resistance. The application of asphalt-bonded dolomite bricks is not only that its price is quite low compared to fired dolomite bricks. It is also due to its good and stable corrosion resistance and performance. However, there is a problem of air pollution being generated during heating, thus limiting their wider application.
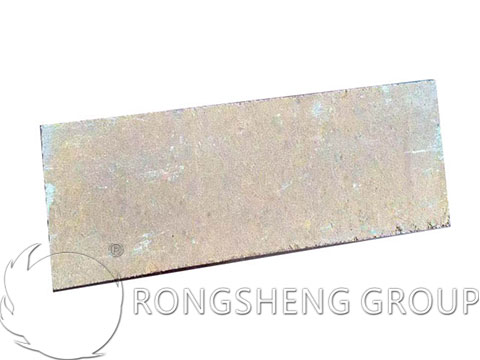
Resin-bonded Dolomite Bricks
With the advent of asphalt-free bricks, the heating process should be extended to eliminate the gas generated by the furnace lining. Increased interest among argon-oxygen furnace steel mills in the application of resin-bonded dolomite bricks. Subsequently, resin-bonded dolomite bricks for argon-oxygen furnaces have been widely used. Resin-bonded dolomite bricks have the best resistance to spalling due to their own thermal expansion properties, so structural spalling is rarely seen. By using a longer preheating method, the amount of carbon absorbed by molten steel from carbon volatiles can be reduced to the level of carbon absorbed by fired dolomite bricks. The reason is that the long heating process increases and deepens the coking of the resin-bound dolomite lining. Another benefit of using a long heating process is that it can significantly reduce the generation of smoke and dust.
It can be seen from the cross-section of the argon-oxygen furnace using resin-bonded dolomite residual bricks that there is an extremely thin layer of slag on the hot surface. The inward penetration is only 0.8~1.6mm deep, and the first non-oxidized residues of carbon can be detected 2mm after approaching the hot surface. Chemical analysis results show that the amount of adhering and penetrating slag components is very low, especially the components containing alumina and MgO that cause corrosion are almost non-existent. According to the study of mineral phases, the erosion is caused by the main transformation of CaO in dolomite into 3CaO·SiO2, 2CaO·SiO2, and some brown goethite and aluminate phases. This shows that due to corrosion, the physical phase in the brick is mainly transformed into a high melting point silicate phase, which can prevent the slag from penetrating into depth and prevent accelerated corrosion.
It seems that the favorable slag composition and the high CaO content provided by the dolomite bricks, which mainly form the high melting point calcium silicate mineral phase, produce favorable corrosion resistance properties. Under these conditions, the amount of residual carbon in dolomite bricks is not as important as the amount of residual carbon in MgO bricks. Because the high-melting-point silicate minerals formed prevent the slag from penetrating into the bricks, they also partially act as carbon. Although the mechanisms of preventing slag penetration by CaO and C are different, the observed effects of preventing slag penetration can be compared. Therefore, the performance of resin-bonded dolomite bricks in argon-oxygen furnaces is not difficult to predict.
The results were obtained by comparing the effects of fired dolomite bricks, asphalt-bonded dolomite bricks, and resin-bonded dolomite bricks on argon-oxygen furnaces. Resin-bonded dolomite bricks and asphalt-bonded dolomite bricks have the same performance but are better than dolomite burned bricks. This shows that the use of resin-bonded dolomite bricks as the lining of the argon-oxygen furnace can reduce the consumption of refractory materials per ton of steel and reduce environmental pollution.
However, the damage speed of various areas of the argon-oxygen furnace lining is different. Therefore, it is necessary to weigh the damage pattern and damage speed of argon-oxygen furnace refractory materials to reduce the consumption of refractory materials per ton of steel. This requires using a variety of refractory materials to comprehensively build the argon-oxygen furnace to achieve balanced corrosion of the furnace lining and achieve a more ideal service life. The figure shows that fired dolomite bricks are used at the furnace bottom, and fired magnesia dolomite bricks containing ZrO2 are used in the tuyere area. The side walls are made of dolomite burned bricks or dolomite bricks with high MgO content, and the inner wall of the cone is made of fired dolomite bricks or resin-bonded dolomite bricks.
Adding ZrO2 to the fired magnesium dolomite bricks used in the more demanding tuyere areas improves the heat-spalling resistance of the refractory materials used in the tuyere areas. At the same time, measures to increase MgO content, reduce porosity, and enhance high-temperature strength can further improve the service life of the tuyere area.
In the slag line area with harsh conditions, especially the trunnion area, dolomite burned bricks rich in MgO are selected. Reducing porosity can improve slag resistance, and measures to enhance high-temperature strength can further extend the service life of the tuyere area.