Magnesia-carbon bricks are widely used as lining bricks for converters due to their excellent resistance to slag erosion, thermal shock resistance, spalling resistance, and wear resistance, as well as good stability at high temperatures. Magnesia carbon bricks have the problem of deterioration in thermal shock resistance and corrosion resistance due to easy oxidation. This has also become a problem that various enterprises and refractory material manufacturers must solve together.
Magnesia Carbon Bricks for Steelmaking Converters
1) Application of new antioxidant and self-repairing composite antioxidants. Metal Al, Si powder, or Al-Si composite powder is used as the antioxidant of magnesia carbon bricks. After heat treatment or high-temperature service, the in-situ reaction generates SiC, AlN, and other highly corrosion-resistant phases. Significantly improve the performance of low-carbon magnesium carbon materials.
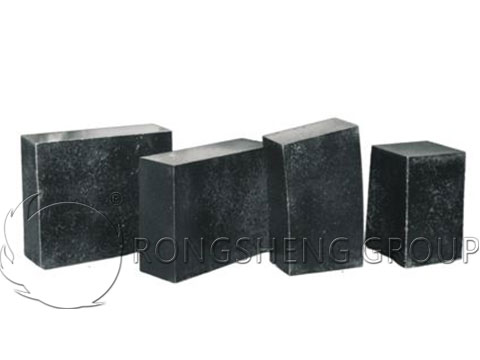
2) Preparation and application of low-dimensional graphitized carbon. The addition and application of various pre-synthesized nanocarbons such as nanocarbon black, nanographite-oxide composite powder, etc. To synthesize low-dimensional graphitized carbon in situ, select inorganic or organic compounds of appropriate transition elements (Fe, Co, Ni) as catalysts. The pyrolysis of phenolic resin produces CO, C2H2, CH4, and other gases, which form low-dimensional graphitized carbon such as carbon nanotubes and nanocarbon fibers under the catalysis of transition metals. Through the development and application of these new technologies, MgO-C bricks can maintain good corrosion resistance and thermal shock resistance.
The MgO-C bricks used in different parts of the converter have different performance requirements. To meet the demand, a Japanese refractory company has developed a series of MgO-C bricks that meet the performance requirements of different parts. The microstructure analysis of used MgO-C bricks shows that the damage of MgO-C bricks is mainly caused by slag erosion damage. By examining the damage factors of MgO-C bricks, Japanese researchers found that limiting the diffusion rate of Mg(g) in MgO-C bricks at high temperatures can reduce the brick damage rate. The slag corrosion resistance test results show that as the apparent porosity of MgO-C bricks (1500°C heat treatment) increases, the corrosion index of the bricks increases linearly. Based on this, dense structure MgO-C bricks were prepared by adjusting the amount of antioxidants added, raw material particle gradation, and production process.
MgO-C bricks in the converter charging area are often subject to mechanical impact from scrap steel raw materials, which are prone to cracks and expansion, leading to damage to the lining. Different types of MgO-C bricks have greatly different creep resistance. This results in differences in the thermal shock and mechanical impact resistance of MgO-C bricks. Researchers from a Japanese refractory company found that MgO-C bricks (HS) with higher high-temperature flexural strength cannot alleviate the occurrence of damage. MgO-C bricks with higher fracture energy (fracture toughness) can effectively inhibit the expansion of cracks. Therefore, two new types of MgO-C bricks were developed, namely matrix-reinforced MgO-C bricks (MR) and carbon-bonded reinforced MgO-C bricks (CB). The two new types of MgO-C bricks have high fracture energies (MR0.40kJ and CB0.49kJ, HS is only 0.26kJ), the crack expansion is suppressed after mechanical impact, and both have better corrosion resistance than HS bricks. Among them, the carbon-bonded reinforced MgO-C brick has better corrosion resistance.
The service life of magnesia carbon bricks at the converter taphole is often affected by carbon oxidation, thermal shock spalling, and flow steel wear. Therefore, the development of low-carbon magnesia carbon bricks with good wear resistance and thermal shock resistance is an inevitable trend of development. Researchers at a steelmaking plant used fused magnesia with m(CaO):m(SiO2)≥2 and high-purity flake graphite (C mass fraction ≥98%) as the main raw materials. Using Al, Mg-Al, Si, B4C, and CaB6 as antioxidants. Thermosetting phenolic resin is used as a binding agent to prepare high-quality low-carbon MgO-C bricks. Using newly developed low-carbon magnesia-carbon bricks in steelmaking converters, the service life of a furnace is stable at 500 to 700 times. It is significantly higher than the 300~400 times of imported low-carbon magnesia carbon bricks.
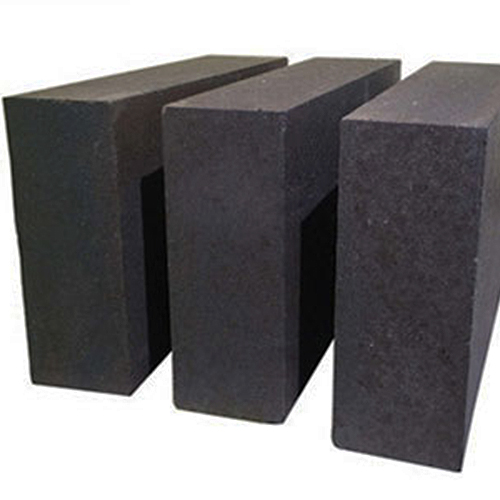
The Use of Magnesia Carbon Bricks in Converter Lining
Since the use conditions of various parts of the converter working lining are different, the use effects of magnesia carbon bricks are also different.
The furnace lining and furnace mouth are constantly impacted by cold and hot molten steel. Therefore, the refractory materials used for the furnace mouth must be resistant to the erosion of high-temperature slag and high-temperature exhaust gas, be difficult to hang steel, and be easy to clean in time. The furnace hat is not only subject to severe slag corrosion but also undergoes rapid cooling and rapid heating temperature changes. Due to the combined effect of the high-temperature airflow of carbon oxidation and the erosion of dust and high-temperature exhaust gas, magnesia-carbon bricks with strong resistance to slag erosion and spalling are used. The charging side requires magnesia carbon bricks to not only have high slag corrosion resistance but also have high-temperature strength and very good spalling resistance. Therefore, high-strength magnesia carbon bricks with added metal antioxidants are usually used. Research shows that the high-temperature strength of magnesia-carbon bricks with added metallic aluminum at lower temperatures is lower than that of samples with composite added metallic aluminum and metallic silicon. At high temperatures, its high-temperature strength increases instead. The slag line is the junction of the three phases of furnace lining refractory material, high-temperature molten slag, and furnace gas. It is the most serious part affected by slag corrosion. Therefore, it is necessary to build magnesia-carbon bricks with excellent resistance to slag erosion, and magnesia-carbon bricks with higher carbon content are required for the slag line.
Rongsheng Refractory Factory
Rongsheng Refractory Factory is a powerful refractory material manufacturer. Our comprehensive refractory services provide customers with high-quality refractory lining material products and high-temperature industrial furnace lining material solutions. Get your free solution for magnesia carbon brick lining for converters. Please contact us.