There are several main types of thermal insulation materials: Calcium silicate products, Composite silicate products, Rock wool products, Slag wool products, Glass wool products, Aluminum silicate wool and its products, and Magnesium silicate fiber blanket. Four of these seven materials are silicates. Calcium silicate blocks, Preformed calcium silicate blocks. There is a simple introduction in Teacher Cai’s book, which was published in 1992.
- Calcium silicate prefabricated blocks have low thermal conductivity, low price, high temperature resistance, and certain strength at high temperatures. They are a promising thermal insulation material. Calcium silicate has been widely used abroad, and is also produced in China, and has good experience in use, so it should be used first.
- Rock wool and mineral wool are both semi-rigid thermal insulation materials. Because of their strong water absorption, a strict waterproof outer protective layer is required.
- Glass wool. The characteristics are similar to rock wool and mineral wool. However, ordinary glass fiber is piercing and inconvenient to construct, so it is generally not used, and only ultra-fine glass fiber is used.
- Perlite. Its thermal insulation and mechanical properties are inferior to those of calcium silicate, and it easily absorbs water, so its application is decreasing. However, it still has certain applications as a bulk filler.
At present, the use effect of aluminum silicate ceramic fiber insulation materials produced by Rongsheng is still good. In the past, glass wool was used more. It is not clear whether the purchased glass fiber is ultra-fine. It is very likely not. This is very unfriendly to workers. Since the price of glass wool is much lower than that of aluminum silicate ceramic fiber wool, many companies are still using glass wool. For the sake of construction safety and people-oriented, it is recommended that aluminum silicate ceramic fiber insulation materials be used for the insulation of chemical pipelines. Contact Rongsheng for detailed information.
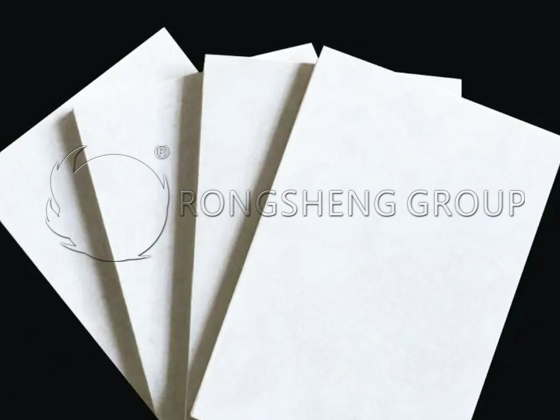
Classification of Calcium Silicate Board
It is divided into two categories according to chemical mineral composition:
- (1) Ordinary calcium silicate board: chemical composition (CaO/SiO2≈0.8, mineral composition is tobermorite (5CaO·6SiO2·5H2O).
- (2) Xonotite board: chemical composition (CaO/SiO2≈1.0, mineral composition is Xonotite (6CaO·6SiO2·H2O).
Raw Materials for Producing Calcium Silicate Board
Silica raw materials are mainly diatomaceous earth, the lightest raw material containing SiO2, which is amorphous SiO2. It is easy to react with lime in warm water below 100℃ to form a colloid. Bentonite, fly ash, quartz sand, silica ash, siliceous shale powder, etc., can also be used.
Calcium raw materials: mainly lime, preferably lime with an effective CaO content of not less than 85%. Fresh lime is digested into lime slurry with water, and the CaO particle size is less than 1μm. It not only has good suspension, but also easily adheres to the surface of SiO2 particles.
Reinforcement fiber: Although asbestos is a good reinforcing fiber, it is banned internationally because magnesium silicate is harmful to the human body. Now it is replaced by alkali-free glass fiber, alkali-resistant mineral wool fiber, pure brucite fiber, etc. Among them, pure brucite fiber is a hydrated carbonate fiber unique to China, which is harmless to the human body. Organic fibers that replace asbestos include pulp, hemp silk, polypropylene silk, etc.
In order to accelerate coagulation, strengthen and reduce bulk density, additives need to be added, including water glass, calcium silicate powder, SiO2 ultrafine powder, polyacrylamide, etc. Among them, water glass is a coagulant, calcium silicate powder and SiO2 ultrafine powder act as nucleation seeds, and the role of polyacrylamide is as follows:
1) Accelerate coagulation;
2) Due to its long molecular chain, it can connect the dispersed phases together to form a network structure, which plays a reinforcing role.
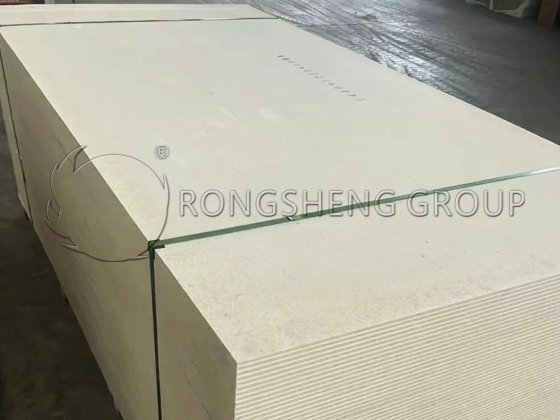
Production Process of Calcium Silicate Board
Weigh the raw materials according to the proportion, put them into the blender with water, and mix them. The amorphous SiO2 in diatomite reacts with slaked lime at a temperature below 100°C to form a gelling particle group with CaO adsorbed on the surface of SiO2 particles.
This particle group undergoes hydrothermal reaction and hydrothermal synthesis under the temperature and pressure of saturated steam in the autoclave. When CaO/SiO2 is about 0.8, calcium-rich CaO·SiO2·H2O is first generated, and low-crystallinity tobermorite (5CaO·6SiO2·5H2O) is further generated. Finally, it is converted into a high-crystallinity tobermorite skeleton with a porosity of more than 90%. After drying and removing the water in the pores, it becomes a calcium silicate insulation material, and after shaping, it becomes a finished product. When (CaO/SiO2 is about 1.0, it becomes hard calcium silicate (6CaO·6SiO2·H2O). Calcium silicate board can be sawed, nailed, and made into shapes such as plates, blocks or tubes.
Performance of Calcium Silicate Board
The performance of calcium silicate board in my country is as follows: the volume density (kg/m3) is divided into three types: 240, 220, and 170. Most international regulations stipulate that it should not exceed 220kg/m3. Compressive strength is above 0.4MPa, flexural strength is above 0.2MPa, thermal conductivity (70±5℃) is 0.049~0.064W/(m·k).
The maximum operating temperature of tobermorite board is 650℃, that of xonotlite board is 1000℃, and the other is a mixed board of tobermorite and xonotlite. Therefore, calcium silicate board has excellent properties such as low bulk density, low thermal conductivity, high strength, convenient construction, and low loss rate.
Storage and Transportation Precautions for Calcium Silicon Board
- No collision is allowed during loading and unloading, and the bottom of the transport vehicle must be flat. After loading, fixed measures should be taken to ensure that there is no displacement or sliding during the journey.
- When hoisting or forklifting, the whole stack of boards must be stacked neatly to prevent the steel rope or forklift shovel from damaging the edge of the board.
- When loading and unloading one by one manually, care should be taken to prevent debris from being sandwiched between the boards. If not cleaned in time, the boards may be cracked or deformed.
- When transporting boards, two people should hold the two sides of the boards upright and transport them. It is strictly forbidden to lift them horizontally.
- The boards should be stacked on a flat ground or placed at the bottom with a special wooden bracket. A small number of loose boards cannot stand upright against the wall.
- The boards should be stored in an indoor warehouse. If they are stored in the open air, they should be covered with tarpaulin.