The checker bricks used for lattice masonry are also called lattice bricks, which refer to the refractory bricks used to build the lattice body of the regenerator in the high-temp furnaces. It is an intermediate medium for heat exchange between high-temperature exhaust gas and preheated gas in the regenerator. Checker bricks are required to have certain corrosion resistance and thermal shock resistance. Commonly used lattice brick materials include refractory clay bricks, high alumina bricks, and mullite bricks, sillimanite bricks, and zirconium corundum bricks. Different brick materials can also be used in sections according to the height of the lattice body, so as to improve its performance of the lattice body. Brick type can adopt standard type or specially shaped brick.
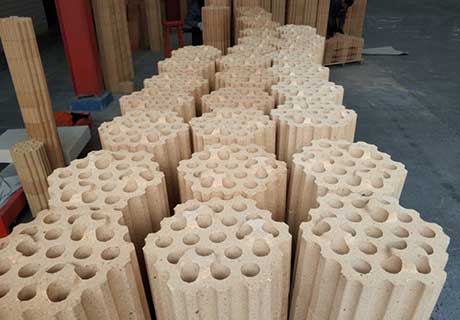
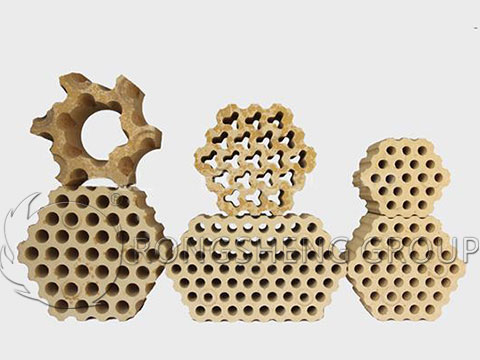
Requirements for Checker Bricks Masonry Technology
Lattice refractory brick refers to the lattice masonry made of refractory bricks in the regenerator. The regenerator must have a large enough lattice body volume and heating area to make full use of the waste heat and promote the preheating gas to reach a higher preheating temperature. There are many forms of masonry for the lattice body, and the following requirements are required in terms of technology.
- It can make full use of the volume of the regenerator, has a large heating area and heat storage capacity, and the temperature of the preheating gas is high and the fluctuation is small;
- Uniform air distribution, high heat transfer efficiency, and low air resistance;
- High-temperature corrosion resistance, stable structure, easy cleaning, and maintenance.
Working principle of glass kiln regenerator
Working principle of glass kiln regenerator. When the high-temperature waste gas in the kiln enters the regenerator from top to bottom through the small furnace mouth and air and gas channels, the regenerator grid is heated to gradually increase the temperature of the grid to store heat. After the fire is changed, the combustion air and gas enter the regenerator from bottom to top through the flue at the bottom of the regenerator. The heat stored in the grid in the regenerator preheats the air and gas. Afterward, the temperature of the lattice body gradually decreases to realize waste heat recovery. Ensure that the flame has sufficient temperature to meet the requirements of glass melting.
The structural form of the glass kiln regenerator
There are many structural forms of glass kiln regenerators, which can be divided into the following types according to whether the regenerators are connected or not.
- Connected structure
The air regenerator below the small furnace on one side of the melting furnace is a connected room, and the gas regenerator is also a connected room. Due to the uneven distribution of airflow, this form is easy to cause local overheating and quickly burns the checker bricks, so it is no longer used at present.
- Separate structure
The regenerator on one side of the melting furnace is divided into several independent chambers that are not connected to each other by each small furnace. The gas distribution is adjusted by the ram on each branch flue respectively and communicates with the air branch flue respectively. Its structural features are convenient adjustment of gas distribution and good thermal repair conditions, but the partition wall occupies more space and reduces the effective volume of the lattice body. But it is one of the most commonly used ways.
- Half-separated structure
It means that the flue below the regenerator bar is separated by each small furnace, the regenerator itself is not divided, and the gas distribution adjustment gate is still on the branch flue.
- Separate structure of two small furnaces
The structural form is that every two small furnaces share a regenerator or separate into a regenerator, and the branch flue is separated by each small furnace to facilitate the adjustment of the gas distribution of each small furnace. This structure is compartmentalized and semi-compartmental. Because of its stable structure, convenient operation, and high heat conversion efficiency, most manufacturers currently adopt this structure.
- Two-stage structure
The structure is to divide a single regenerator into two regenerators, which are separated by a partition wall and connected by a vertical passage. That is, the two parts of the regenerator divided into the high-temperature zone and low-temperature zone adopt this structure mainly to prevent the corrosion of checker bricks by gas, liquid, and solid conversion of sodium sulfate. Make this transformation take place within the link channels of the regenerator to prolong the life of the checker bricks. However, this form of regenerator has a complex structure and is rarely used.
For more details, please contact us, we are Rongsheng Refractory Manufacturer.