Refractory bricks are indispensable materials in industrial kilns and high-temperature equipment. They have different sensitivity to water according to different materials. What are the problems with the water resistance of magnesia spinel bricks? And how to effectively store and use magnesia spinel bricks? Rongsheng Refractory Bricks Manufacturer, with rich production and sales experience, supplies high-quality magnesia spinel bricks and magnesia-iron spinel bricks. Contact Rongsheng for more information.
Differences in Water Resistance of Refractory Bricks
Refractory bricks are made of various materials, such as clay bricks, high-alumina bricks, corundum bricks, and silica-molybdenum bricks. They can usually be used normally even if they encounter rain during storage and transportation. However, alkaline refractory bricks, especially magnesia-spinel bricks, are highly sensitive to water. Once damp, their performance will be greatly reduced.
Water resistance of magnesia-spinel bricks. Magnesia-spinel bricks contain magnesium oxide and calcium oxide, which are easy to absorb moisture and undergo a hydration reaction when exposed to water, resulting in loose brick structure and reduced strength. Therefore, strict waterproofing measures must be taken during production and transportation.
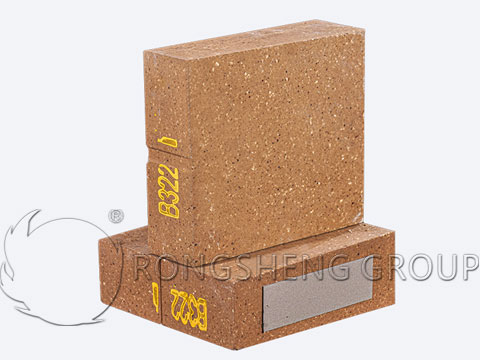
Storage and Use Guide for Magnesium Spinel Bricks
In order to extend the service life of refractory bricks, it is recommended to store refractory bricks in a ventilated and dry environment. Long-term exposure to a humid environment may not only affect the structure of the brick body, but also cause moss to grow on the surface of the brick body.
Weight change of damp refractory bricks. Refractory bricks have a certain water absorption capacity, and they will increase in weight after being damp, which not only affects the transportation cost, but may also cause overloading problems.
Remediation of alkaline refractory bricks after being damp. Once alkaline refractory bricks such as magnesium iron spinel bricks are damp, remedial measures are usually ineffective. Because the hydration reaction may cause irreversible structural changes. In this case, it is usually necessary to re-order new refractory bricks.
Baking of refractory bricks. After the masonry of refractory bricks is completed, the baking process needs to be carried out to remove moisture from the brick body and masonry joints. If the refractory bricks are baked in a damp state, a large amount of water vapor may be generated, which increases the baking time and difficulty, and may even cause safety accidents.
In order to ensure the safety of the project and the performance of refractory bricks, especially magnesia-iron spinel bricks, in principle, they should not be used after being exposed to water and damp. It is recommended to take appropriate waterproofing measures to avoid using damp refractory bricks to ensure the smooth progress and safety of the project.
Correct storage and use can not only extend the service life of refractory bricks, but also ensure the safe operation of industrial kilns and high-temperature equipment.
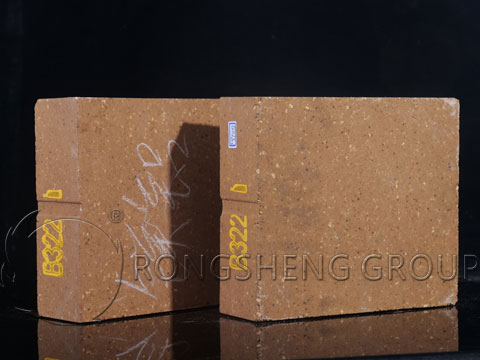
Problems and Improvement Measures of Magnesium Spinel Bricks for Cement Rotary Kilns
Magnesium spinel bricks have begun to be used in cement kilns to deal with the chromium hazards brought by magnesia-chrome bricks. Magnesium spinel bricks not only have excellent thermal shock stability, but also react chemically with cement clinker. A protective film is formed on the surface of magnesium spinel bricks. It can prevent the liquid phase from diffusing into the interior of magnesium spinel bricks, so the peeling resistance of magnesium spinel bricks is better than that of magnesium-chrome bricks.
Although magnesia-chrome bricks can be replaced by magnesium spinel bricks in cement rotary kilns to a certain extent, there are still some problems with magnesium spinel bricks:
- (1) The ability to hang the kiln skin is weak, and the refractory bricks will be severely chemically corroded, thereby reducing the application time of the bricks.
- (2) The heat loss of the cement kiln body increases, the heat consumption increases, and the material is wasted.
- (3) Under high temperature conditions, a low melting point mineral phase is produced inside the magnesia spinel brick. Magnesium spinel bricks are easily subject to severe chemical corrosion and then damaged.
- (4) Magnesium spinel bricks can easily undergo hydration reactions.
Therefore, in order to extend the service life of refractory bricks, improvements can be made to the two aspects of their kiln skin performance and anti-stripping performance. Among them, the methods for improving magnesium spinel refractory bricks include the following measures:
- Add additives to magnesium spinel, such as: TiO2, Fe2O3, ZrO2, etc. Adding additives is very beneficial to the firing of materials, the reduction of apparent porosity, the enhancement of chemical corrosion resistance, and the improvement of kiln skin ability.
- Appropriately reduce the content of magnesium spinel to allow microcracks to exist inside the brick. Thereby reducing thermal conductivity and improving spalling resistance.
- Studies have found that when the content of alumina in refractory bricks is less than 10%, the kiln skin performance of the bricks is better. Therefore, by reducing the alumina content in magnesium spinel bricks, the kiln skin ability of the material can be improved.
In the application of cement rotary kilns, magnesium spinel bricks with high strength, excellent thermal shock stability, and strong resistance to chemical erosion are mainly used in the upper and lower transition zones of cement rotary kilns and thermal kiln equipment that require high-temperature resistance and thermal shock resistance.