Product introduction of circular tunnel kiln insulation cotton. Insulation material for a Tunnel Kiln. Circular tunnel kiln insulation cotton-ceramic fiber module. China produces 670 billion standard bricks every year and is a major brick and tile producer. Although the traditional rotary kiln has low project investment, it has high labor costs, high energy consumption, and low output. The development of tunnel kilns in China has gone through three stages:
- ①Heavy refractory materials + lightweight insulation materials + red bricks
- ②Light refractory materials + ceramic fibers
- ③Lightweight energy-saving furnace building materials, ceramic fiber modules
After the brick and tile tunnel kiln, mobile tunnel kiln, and circular tunnel kiln use the circular tunnel kiln insulation cotton ceramic fiber module, it has the advantages of large production capacity, reduced fuel consumption, long service life, high degree of mechanization and automation, and good working conditions.
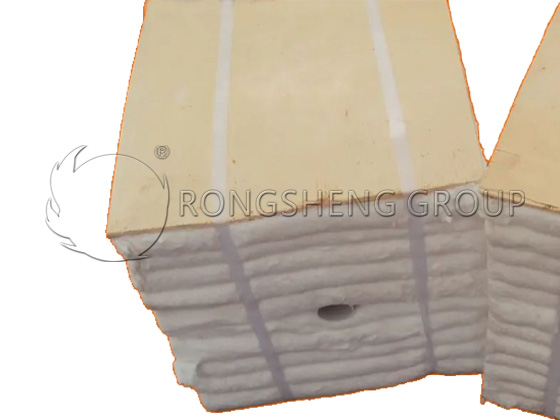
The Structure of the Ring Tunnel Kiln and the Selection of Insulation Cotton
The requirements of the kiln roof structure: the material should withstand high temperature for a long time (especially the firing zone), be light in weight, have good insulation, have a tight structure, no air leakage, and be conducive to the reasonable distribution of airflow in the kiln.
Generally, the tunnel kiln body is divided into a preheating section (low temperature section), a firing and roasting section (high temperature and short), and a cooling section (low temperature section) from front to back, with a total length of about 90 m to 130 m.
The low temperature section (about 650 degrees) generally adopts the 1050 ordinary type, and the high temperature section (1000~1200 degrees) generally adopts the standard 1260 type or 1350 zirconium aluminum type. The structure of the ring tunnel kiln insulation cotton is made by combining ceramic fiber modules and ceramic fiber blankets.
The use of ceramic fiber modules and layered blanket composite structures can reduce the temperature of the outer wall of the furnace and extend the service life of the furnace wall lining. At the same time, it can also level the unevenness of the furnace lining steel plate and reduce the cost of the insulation cotton furnace lining. In addition, when the hot surface material is damaged and gaps are produced unexpectedly, the flat layer can also play a role in temporarily protecting the furnace body plate.
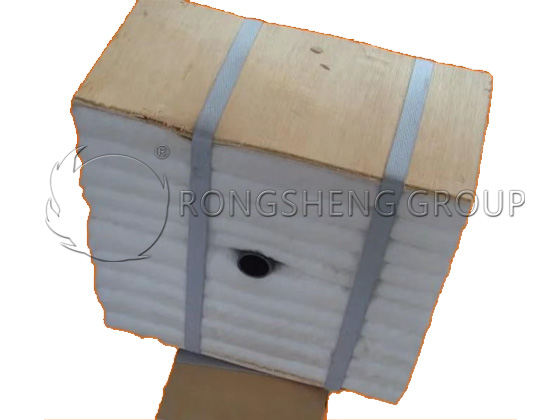
Advantages of Using Ceramic Fiber Module Lining for Circular Tunnel Kiln Insulation
- The volume density of ceramic fiber lining is low, which is more than 75% lighter than lightweight insulation brick lining and 90%~95% lighter than lightweight castable lining. It can effectively reduce the steel structure load of the kiln and extend the service life of the furnace.
- The thermal capacity (heat storage) of ceramic fiber lining is low. The thermal capacity of ceramic fiber is only about 1/10 of that of lightweight heat-resistant lining and lightweight castable lining. Low thermal capacity means that the kiln absorbs less heat during reciprocating operation, and the heating speed is accelerated, which reduces the energy consumption in the furnace temperature operation control. It has a significant energy-saving effect on starting and stopping the furnace.
- Ceramic fiber lining has low thermal conductivity. The thermal conductivity of ceramic fiber lining is less than 0.1w/mk at an average temperature of 400℃, less than 0.15w/mk at an average temperature of 600℃, and less than 0.25w/mk at an average temperature of 1000℃. It is about 1/8 of lightweight clay bricks and 1/10 of lightweight heat-resistant linings.
- Ceramic fiber is easy to construct and operate as a furnace lining. It shortens the construction period of the furnace.
Detailed Installation Steps of Circular Tunnel Kiln Insulation Cotton
Ceramic fiber cotton products can be used as kiln lining, boiler insulation, heat treatment temperature control, and glass kiln roof insulation.
(1) Rust removal: Before construction, the steel structure party needs to remove rust from the copper plate of the furnace wall to meet the welding requirements.
(2) Line drawing: According to the arrangement position of the ceramic fiber module shown in the design drawing, lay out the line on the furnace wall plate and mark the arrangement position of the anchor bolts at the intersection.
(3) Welding bolts: According to the design requirements, weld the bolts of corresponding length to the furnace wall plate according to the welding requirements. When welding, protective measures should be taken for the threaded part of the bolt, and welding slag should not be splashed onto the threaded part of the bolt, and the welding quality should be ensured.
(4) Installation of flat blanket: Lay a layer of fiber blanket, and then lay the second layer of fiber blanket. The joints of the first and second layers of blankets should be staggered by no less than 100mm. For the convenience of construction, the flattening of the furnace roof needs to be temporarily fixed with quick cards.
(5) Module installation:
- Tighten the guide sleeve into place.
- Align the center hole of the module with the guide tube on the furnace wall, push the module evenly perpendicular to the furnace wall, and make the module close to the furnace wall. Then use a special sleeve wrench to push the nut along the guide sleeve to the bolt and tighten the nut.
- Install other modules in the same way.
(6) Installation of compensation blanket: The modules are arranged in the same direction in the folding and compression direction. In order to avoid gaps between modules in different rows due to fiber shrinkage after high-temperature heating, compensation blankets of the same temperature grade must be placed in the non-expansion direction of the two rows of modules to compensate for the shrinkage of the modules. The compensation blanket for the furnace wall is fixed by the extrusion of the module, and the compensation blanket for the furnace roof is fixed with U-shaped nails.
(7) Lining correction: After the entire lining is installed, trim it from top to bottom.
(8) Lining surface spraying: After the entire lining is installed, spray a layer of surface coating on the surface of the furnace lining (optional, which can extend the service life of the furnace lining).