Large-scale rotary kilns are more and more used in industrial production because of their advantages such as large output, stable production, and uniform calcination of products. In addition to the cement industry, large-scale rotary kilns are used in the production of alumina by activated lime calcination, chromium salt sintering, and alkali-lime sintering. The main difference between the rotary kiln and other kiln types is that it is in a rotating state during the production process. That is, the inner lining rotates with the kiln body, and the material and hot air act on the inner lining alternately, so the requirements for the inner lining material and masonry structure are higher. Long-life refractories for the insulation layer of the rotary kiln are also a very important part. Rongsheng Refractory Factory is committed to providing high-quality Long-life Refractory Lining Solutions for Rotary Kiln Insulation Layers and the design of insulation layer refractory materials for rotary kilns, providing a complete solution to reduce the temperature of the outer wall of the rotary kiln.
Refractory Lining Solution for Rotary Kiln Insulation Layer
The main function of the refractory lining of the rotary kiln is to protect the kiln shell from the damage of high-temperature gas and high-temperature materials, so as to ensure normal production. The damage to rotary kiln refractories is caused by many factors. Some of these damages come from the calcination flame, some from the intrusion of impurities, some from the deformation of the cylinder, and some from the irregularity of the masonry. The damage suffered by refractory materials mainly includes chemical erosion, thermal stress, and mechanical stress. It often occurs that the service life of the overall refractory lining of the rotary kiln is reduced due to damage to the refractory lining material of the insulation layer. Seriously, accidents endangering life safety may occur. Based on years of production and sales experience, Rongsheng Refractory Factory can solve the short service life of rotary kiln refractory lining materials for you. Improve the service life of the refractory lining material of the rotary kiln, reduce the temperature of the outer wall of the rotary kiln, and reduce the production cost for the enterprise. For the special type of rotary kiln, we have used the composite brick structure of dense brick and light insulation brick as the lining of the rotary kiln, and there are also successful cases of prefabricated blocks for the lining of the rotary kiln. Contact us to get more and more detailed solutions for rotary kiln refractory lining.
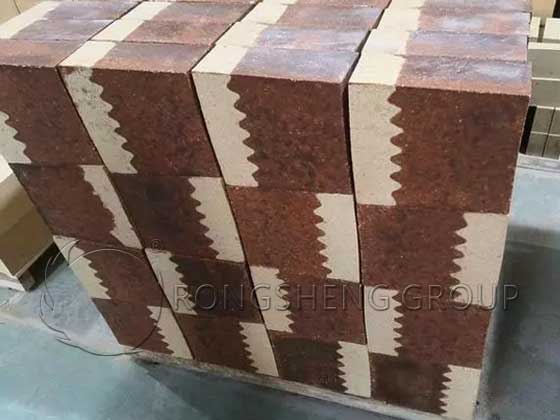
Dense Brick and Light Insulation Brick Composite Bricks
Existing rotary kiln refractory bricks generally include single-layer brick structures and double-layer brick structure masonry. Two methods, among them, the surface temperature of the single-layer brick structure rotating cylinder is too high, which is likely to cause problems such as deformation of the cylinder and fire of the transmission gearbox. The double-layer structure is made of dense bricks and light insulation bricks. The application of composite bricks on the rotary kiln can reduce the temperature of the cylinder surface and effectively reduce the heat radiation loss of the rotary kiln cylinder. It is beneficial to reduce the deformation of the rotary kiln shell and prolong the overall life of the shell and equipment.
Composite refractory bricks usually include a refractory layer and an insulation layer. The refractory layer is used as the working surface, facing the high-temperature fire surface, and the insulation bricks layer faces the furnace shell surface, which plays the role of heat insulation. The refractory layer and insulation layer of the existing composite refractory bricks is generally used as a whole by direct pressing. The dense part of the refractory layer can be made of materials with good wear resistance and corrosion resistance, such as silicon carbide, chromium oxide, sintered corundum, fused corundum, mullite, and activated alumina micro powder. The light part uses bauxite, lightweight corundum aggregate, and composite lightly burned powder. The dense part and the light part are sintered at high temperatures to form an integration of light and dense, and the light part is used as the insulation layer, and the dense part is used as the brick body of the working layer. Composite refractory bricks can not only continue to maintain the wear-resistant and anti-corrosion effect on the original basis but also play a certain role in reducing heat conduction under the support of the insulation layer so that the temperature of the furnace surface is reduced and the loss of heat source is small.
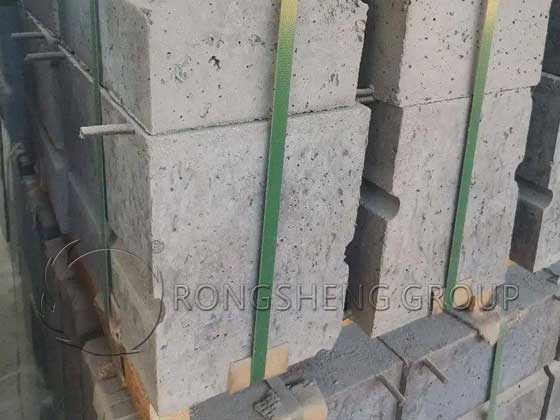
Rotary Kiln Lining Precast Blocks
The prefabricated block of the rotary kiln lining is a cuboid, containing a high-temperature resistant layer and an insulating layer. An anchoring internal reinforcement is arranged in the cuboid prefabricated block, and both ends of the anchoring internal reinforcement protrude beyond the width direction of the surface of the prefabricated block. It is characterized in that strip-shaped protrusions or grooves are provided on both sides of the high-temperature-resistant layer, and the cross-section of the strip-shaped protrusions or grooves is arc-shaped, triangular, trapezoidal, or square. The anchoring internal reinforcement is an approximately inverted “U” shape, or approximately inverted “V” shape, or approximately isosceles trapezoid. The plane where the main part of the anchoring inner reinforcement is located is oblique to the longitudinal center plane of the prefabricated block, and the protruding ends of each anchoring inner reinforcement on both sides of the high-temperature resistant layer are asymmetrical with respect to the longitudinal centerline of the prefabricated block. Outriggers of equal height are provided on the side of the high-temperature-resistant layer close to the shell of the rotary kiln, and the shape and thickness of the insulation layer match the shape and thickness of the outriggers and are snapped together. The anchoring inner reinforcement of the prefabricated block is strong and durable, and the insulation layer is not easily damaged, which can effectively prolong the life of the rotary kiln. For the insulation layer here, Rongsheng Refractory Factory uses castables as a seal and lock seam structure. It solves the problem that the refractory lining of the rotary kiln is easy to drop bricks.
In industrial kilns and thermal equipment, prefabricated block masonry is used to realize mechanized hoisting. Save labor and labor, shorten the construction period, and improve the operating rate of thermal equipment. Rongsheng Refractory Factory can formulate system solutions, material selection, construction, etc. according to the actual production conditions of the customer’s rotary kiln, providing a reliable guarantee for your rotary kiln refractory lining materials.
Of course, for rotary kilns with different production needs, the solutions for the long-life refractory lining of the rotary kiln insulation layer are also different. We can learn from the configuration scheme of refractory lining materials of the same type of rotary kiln. However, refractory material manufacturers remind business owners to customize according to their own production conditions, so as to ensure production safety to the greatest extent. Please contact us for the solution to the short service life of the refractory material of the rotary kiln insulation layer. The design of our professional technical team will not let you down.