In general, soft clay is often used as a binder in the high alumina bricks manufacture. The main function of clay in batching is to improve the moulding property of the clay and to make the green body have certain strength after forming and drying. However, in the firing process, the free SiO2 in the clay and the free A12O3 in the high bauxite clinker have a secondary Mullite reaction, which is intensified with the increase of the amount of the combined clay. The stronger the secondary Mullite reaction is, the higher the porosity of the high alumina brick will be, and the more the strength and volume density will be decreased. Starting from this point, the alumina refractory bricks supply should minimize the amount of combined clay added to the mix. The amount of clay powder added to the mix is usually 5%.
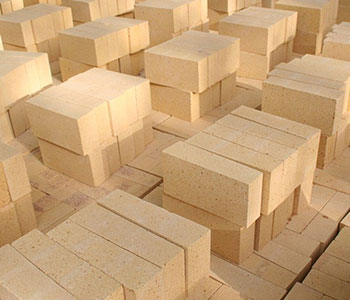
In order to prepare volumetric stabilized high alumina brick, high alumina binder can be used. The volume-stabilized alumina refractory brick without secondary expansion can be prepared by mixing high alumina powder with clay powder in a predetermined proportion and preparing mullite as a binder. The practice shows that increasing the size and quantity of coarse particles can improve the density of sludge and make it easy to form. During sintering, because the specific surface area of the large granular material is small, the secondary Mullite reaction around the material is weakened, which is beneficial to the sintering of the green body. In this way, the porosity of alumina refractory bricks supply is reduced, the softening temperature and compressive strength are increased, and the thermal stability is improved.
The fine powder in the mixture of high alumina refractory brick is beneficial to the sintering of the billet and the improvement of the density of high alumina refractory brick. By adding proper amount of fine powder, the secondary mullite reaction occurred during firing of high alumina bricks can be carried out in fine powder to prevent the loose body due to the secondary mullite reaction around the coarse particles. Moreover, the sintering shrinkage due to the sintering action of fine powder can weaken or offset the volume expansion caused by the secondary Mullite reaction. However, when the fine powder is too much, not only is the forming of the green body difficult and the forming efficiency is low, but also the green body is easy to produce cracks, and the firing shrinkage is larger at the firing time, which increases the rejection rate. In view of this, it is advisable to add about 50% fine powder.
Alumina refractory bricks supply content above 48% is a neutral refractory. Made of bauxite or other raw materials of higher alumina content after molding and calcining. High thermal stability, refractoriness above 1770℃. Good slag resistance, used for lining steelmaking furnace, glass furnace, cement converter, etc. The refractory products have the advantages of high temperature creep, strong corrosion resistance, good thermal shock stability and so on.
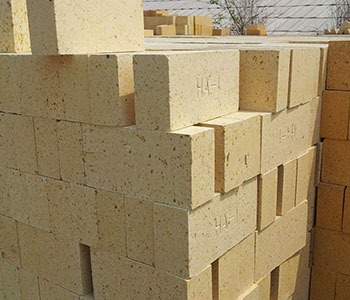
Production technology of the series of refractory brick and clinker clay bricks are similar, the difference is that the ingredients in the clinker ratio is higher, can be as high as 90 ~ 95%, before breaking the clinker grading sorting and screening in addition to iron, firing temperature is higher, such as Ⅰ, Ⅱ high alumina brick with tunnel kiln firing when the general is 1500 ~ 1600 ℃. Al2O3 is more in the composition, which is close to the neutral refractory material and can resist the erosion of acidic slag and alkaline slag. Due to the SiO2 contained in the composition, the ability of alkali slag is weaker than that of acid slag.