The composition of silicon carbide refractory castable is mainly made of high-purity silicon carbide as aggregate, and then adding pure calcium aluminate cement and micro powder as a binder. Construction methods can be cast, sprayed, and smeared. Silicon carbide castable high-temperature wear-resistant lining has high strength and wear resistance, so it is often used as the lining of launders and containers for molten metal or slag. Such as iron furnace molten iron flow trough, molten iron tank lining, tapping groove, etc. It can also be used as a high-temperature wear-resistant lining, such as a high-temperature cyclone lining.
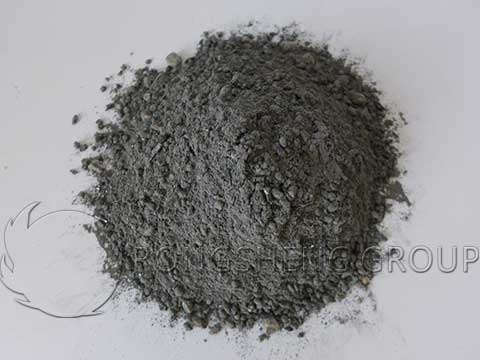
Composition of silicon carbide castable high-temperature wear-resistant lining
- Silicon carbide
Silicon carbide, also known as emery, is made from raw materials such as quartz sand, petroleum coke (or coal coke), and sawdust (salt is required to produce green silicon carbide) through high-temperature smelting in a resistance furnace. It is widely used in refractory raw materials. Common silicon carbide is divided into black silicon carbide and green silicon carbide.
Silicon carbide has stable chemical properties, high thermal conductivity, a small thermal expansion coefficient, and good wear resistance. In addition to being used as aggregate for refractory castables, there are many other uses. For example, coating silicon carbide powder on the inner wall of the turbine impeller or cylinder block by a special process can improve its wear resistance and prolong the service life by 1 to 2 times. Low-grade silicon carbide is an excellent deoxidizer, which can speed up steelmaking, facilitate chemical composition control, and improve steel quality. Silicon carbide is also widely used to make silicon carbide rods for electric heating elements.
- Pure calcium aluminate cement
Pure calcium aluminate cement is a hydraulic binder with an alumina content of about 70-80%, which is formed by sintering high-purity calcium oxide and alumina at high temperatures. Pure calcium aluminate cement can not only impart high mechanical properties to amorphous refractories but also make it have excellent high-temperature performance, which is very suitable for high-temperature environments. Therefore, it is used by refractory castable manufacturers to configure the high-temperature wear-resistant lining of silicon carbide castables.
Advantages and disadvantages of silicon carbide castable high-temperature wear-resistant lining
One of the major advantages of silicon carbide castable high-temperature wear-resistant lining is that silicon carbide refractory castable has high thermal conductivity, low thermal expansion, no reaction with slag, high strength, and good wear resistance. However, silicon carbide refractory castables are easily corroded in some oxidizing environments, and silicon carbide is poorly soluble in water. In water-based unshaped refractories such as castables, poor fluidity sometimes results in poor compactness of silicon carbide refractory castables.
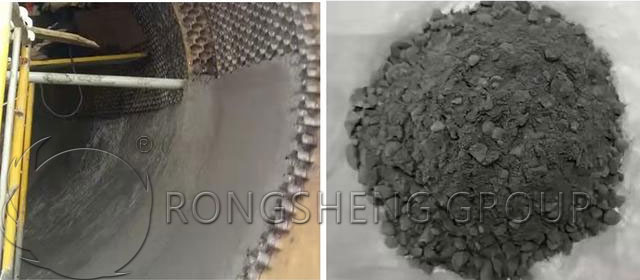
Construction of Silicon Carbide Castable High-Temperature Wear-Resistant Lining
Silicon carbide castable high-temperature wear-resistant lining, like common refractory castables, is constructed by pouring, or by spraying and smearing. In the construction process, the quality of the construction should be strictly controlled, and the configured castables should be used in time. Avoid problems in the construction of refractory castables over time. Maintenance should be carried out in time after construction, so as to better ensure the service life of silicon carbide refractory castables.
In what atmosphere and temperature are the silicon carbide castable high-temperature wear-resistant lining suitable for use?
Silicon carbide castables are suitable for use in furnace linings in a reducing atmosphere, and the effect is better when used at temperatures above 1500 °C.
Silicon carbide castable is a composite refractory castable. A certain proportion of silicon carbide, alumina micro powder, corundum, or high-content bauxite is added to the inner matrix. The binder is composed of pure calcium aluminate cement and some other chemical components.
The use temperature of silicon carbide in reducing atmosphere is as high as 2454 ℃. If used in an oxidizing atmosphere, an oxidation reaction is likely to occur. Silicon carbide cannot produce a protective film on the surface if used in an oxidizing atmosphere. If the oxidation pressure is high, the surface layer will crack or peel due to temperature change and mechanical shock.
If the oxygen partial pressure is low, the protective layer cannot be formed, but it will diffuse in the pores, resulting in a decrease in the quality of the high-temperature wear-resistant lining of the silicon carbide castable.
The castable manufacturer adds a certain proportion of binder to the composite process ratio to adjust the oxidation reaction. In general, metal silicon is used to adjust to inhibit the oxidation reaction. Sodium salt solution or sol can also be used to penetrate into the open pores of the material, which can inhibit oxidation and improve the service life.
Therefore, silicon carbide castable high-temperature wear-resistant linings are not suitable for use at low temperatures, especially in oxidizing atmospheres. Used in a reducing atmosphere, the higher the temperature, the better the use effect.
Silicon carbide castable high-temperature wear-resistant linings are mostly used in boiler linings or linings for iron trenches in front of blast furnaces. High wear-resistant castables are used in boiler linings. It is also used in the blanking part of the rotary kiln, and its use effect is also very good. A castable called an anti-skinning castable is used in this area.
Because of the high temperature and harsh conditions of use. Silicon carbide castables have particularly good wear resistance. As long as it is used in the right place, the service life will be increased by more than 50% compared with the service life of ordinary low-cement castables. Silicon Carbide Castable High Temperature Wear Lining in the Philippines, for free samples and quotes, please contact Sales@rongshengrefractory.com.