Phosphoric acid and acidic oxides hardly react and harden at room temperature. Therefore, it is not suitable as a binder for acidic refractory materials. Phosphoric acid reacts with amphoteric oxides (such as Al2O3) at room temperature to form a hard solid, and the reaction rate between them can be controlled. Therefore, it is particularly suitable as a binder for high-alumina refractory materials. Rongsheng refractory material manufacturer has rich experience in refractory production and sales. Rongsheng’s advanced monolithic refractory castable production line has an annual output of 80,000 tons. Understand the ratio and performance of phosphate bonded refractory castables. For the prices of various monolithic refractory materials, please contact us.
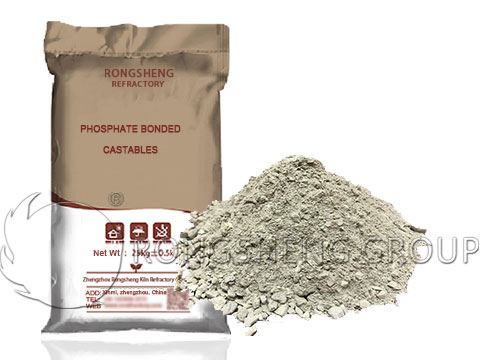
Proportion and performance of phosphate bonded refractory castable
Common phosphate-bonded refractory castables are High-alumina refractory castables, fast-rising wear-resistant castables for circulating fluidized bed boilers, corundum-mullite wear-resistant refractory castables, high-strength alumina phosphate combined with corundum castables, etc. Next, we will separately understand them in detail.
High alumina refractory castable
Refractory workers in my country started the research on phosphate high-alumina refractory castables in the 1960s. Use high bauxite clinker such as Ⅰ and Ⅱ as aggregate and admixture (fine powder), and orthophosphoric acid as a cementing agent. Table 1 lists the ratio of high alumina refractory castable cemented by orthophosphoric acid in my country. Table 2 lists the physical properties of high-alumina refractory castables.
Table 1 Proportion of high alumina refractory castable cemented by orthophosphoric acid in my country
Table 1 The Proportion of High Alumina Refractory Castable Cemented by Orthophosphoric Acid in China | |||||||||
Items | High-Alumina Aggregate | High-Alumina Admixture | Orthophosphate
(additional) |
Coagulant (additional) | Forming Method | ||||
Grade | W / % | Grade | W / % | Grade | W / % | Grade | W / % | ||
Factory Ⅰ | Ⅰ | 70 | Ⅱ | 30 | 50 | 15 | Bauxite cement | 2.8~3.0 | vibration |
Factory Ⅱ | Ⅰ | 70 | Ⅰ | 30 | 45 | 12 | Bauxite cement | 2.0 | vibration |
Factory Ⅲ | Ⅰ | 70 | Ⅰ | 30 | 40~60 | 15~18 | – | – | Ramming |
Factory Ⅳ | Ⅰ | 70 | Ⅰ | 30 | 50 | 14 | Bauxite cement | 2.0 | vibration |
Table 2 Physical properties of my country’s orthophosphoric acid cemented high alumina refractory castable
Table 2 Physical Properties of Orthophosphoric Acid Cemented High Alumina Refractory Castable in China | |||||||||
Items | Refractoriness Under Load / ℃ | Linear Change Rate | Thermal Expansion Coefficient/×10-6 ℃ | Thermal Shock Resistance / Cycle | Bulk Density / (g·cm-3) | Apparent Porosity / % | Crushing Strength / MPa | ||
0.6% | 4% | 40% | 1400℃ | 20~900℃ | 850℃, water quenching | 1400℃ | 1400℃ | – | |
Factory Ⅰ | 1390~1420 | 1400~1430 | – | 0~-0.1 | 6.8~7.1 | >25 | – | – | 30.6 |
Factory Ⅱ | 1290 | 1550 | – | +0.10 | – | >25 | – | – | 43.2 |
Factory Ⅲ | 1300~1350 | 1400~1530 | – | +1.0 | 5.0~6.8 | >80(1000℃) | – | 29.0 | 30~40 |
Factory Ⅳ | 1200 | 1430 | 1490 | – | – | – | 2.70 | ? | ? |
Luoyang Institute of Refractory Materials has developed phosphoric acid combined with high-alumina refractory castables. The proportion (w) is 70% of Ⅰ grade bauxite clinker particles ≤7mm, and 30% of 200 mesh Ⅰ grade bauxite fine powder. Accelerator high alumina cement 2%~3%, mass concentration 50% phosphoric acid 11%. Its performance is listed in Table 3.
Table 3 The performance of phosphoric acid combined with high alumina castable
Table 3 The performance of phosphoric acid combined with high alumina castable | ||||
Heat treatment temperature | Linear Change Rate / % | Flexural Strength / MPa | Crushing Strength / MPa | Bulk Density / (g/cm3) |
110 ℃ 20h | ~ 0.18 | 9.8 | 31.5 | 2.83 |
500 ℃ 3h | ~ 0.02 | 10.5 | 38.5 | 2.82 |
1350℃ 3h | ~ 0.06 | 10.4 | 41.7 | 2.79 |
The influence of liquid alumina dihydrogen phosphate binder on the properties of high-alumina castables
Chen Bei studied the effect of liquid alumina dihydrogen phosphate binder on the properties of high-alumina castables. Among them, the selected high-alumina castable materials are first-grade high-alumina clinkers, clay clinkers, and raw clay. The results are as follows:
- 1) n(P2O5): n(Al2O3)=3 The flexural strength and thermal shock resistance of alumina dihydrogen phosphate combined high-alumina castables are significantly better than water glass combined and alumina sulfate combined high-alumina castables.
- 2) The mass concentration of phosphoric acid used in the preparation of alumina dihydrogen phosphate solution is 65%. And when n(P2O5): n(Al2O3)=3, the combined high-alumina castable has the highest flexural strength (>9MPa), and the thermal shock resistance (900℃, air cooling 5 times) is also good. The flexural strength retention rate is 55%.
- 3) The most suitable amount of alumina dihydrogen phosphate solution is 12% (w). The flexural strength of the castable is 8.83MPa, the softening temperature under load is 1425℃, and the apparent porosity is 22.6%. Air-cooled at 950°C for 5 times. The flexural strength retention rate is 69.5%, and the thermal shock resistance is good.
- 4) Choose a high-alumina castable combined with a composite binder whose volume ratio of alumina dihydrogen phosphate and alumina sulfate is 1:1. It can meet the basic performance requirements of the material: the flexural strength is 6.63MPa, the load softening temperature is 1415℃, and the apparent porosity is 22.7%. Air-cooled at 950℃ for 5 times, the retention rate of residual strength is 68.7%.
Need Refractory Castable Materials for Your Furnace Lining?
Get Free Quote from Factory!
Researchers at Henan University of Science and Technology use 70% (w) high alumina bauxite clinker as aggregate and 30% (w) corundum fine powder and alumina fine powder as a matrix. Add 4%(w) SiO2 powder, 3%(w) soft clay, and 1.5%-2%(w) alkaline hardener to prepare high-alumina castable. They also studied the effect of liquid alumina dihydrogen phosphate on its performance, and the results are as follows. When the mass concentration of alumina dihydrogen phosphate is 50%, n(P2O5): n(Al2O3)=3, and the addition amount is 12%~15%(w), the performance of the castable is the best. The forming process of alumina dihydrogen phosphate combined with high alumina castable is as follows. Weigh the raw materials according to the ratio. After the mixer is evenly mixed, add half of the binder and stir for 3 minutes. After mixing and aging for 10 hours, add the remaining half of the binder to the stale material, and then stir for 3 minutes. Pouring and natural curing for 24h. Demoulding, heat treatment after drying.
Fast heating wear-resistant castable for circulating fluidized bed boiler
A company in Jiangxi invented a fast-rising wear-resistant castable for circulating fluidized bed boilers. This product is supplied in two groups. Group A is prepared from wet materials. In the reaction pot, 100 kg of industrial phosphoric acid with a mass concentration of 85% is heated to 90°C. At the same time, 80 kg of water and 26 kg of active alumina hydroxide were mixed into a paste. While stirring, slowly add the paste into the reaction pot. After the reaction is completed, the material liquid is a colorless transparent colloid. The control viscosity is 45s. At the same time, 180g of oxalic acid was completely dissolved in 200g of water. When the material in the reaction pot is cooled to 50°C, the oxalic acid solution is added dropwise to the reaction pot. After complete mixing, the material liquid is filtered, and the resulting filtrate is the adhesive. Overlay 90kg of special grade bauxite aggregate of 3~1mm, 110kg of ≤1mm, and 30kg of the above-mentioned adhesive and put them into a 0.25m3 strong mixer and stir for 30min to obtain Group A wet material. Each bag is packed in 15kg for later use. Group B is prepared with dry ingredients. Add 50kg of α-Al2O3 powder, 100kg of sub white corundum powder, 40kg of silica powder, 30kg of fused high alumina cement, 2kg of rare earth, 1kg of explosion-proof fiber, 1kg of expansion agent, and 0.5kg of water reducing agent in a 0.25m3 powerful mixer. Stir for 30 minutes to get the dry material of group B. Each 4kg bag is packed for later use. When using, mix one bag in group A and one bag in group B, and mix them manually or mechanically before construction. The properties of the phosphoric acid combined with wear-resistant castable are listed in Table 4.
Table 4 Performance of phosphoric acid combined with wear-resistant castable
Table 4 Performance of phosphoric acid combined with wear-resistant castable | ||||
Items | Factory Ⅰ | Factory Ⅱ (USA) AA-22 | Factory Ⅲ JZ-13 | |
Bulk Density / (g/cm3) | 2.78 | 2.72 | 2.70 | |
Flexural Strength / MPa | 110℃ 24h | 11.8 | 9~10 | ≥7 |
1000℃ 3h | 14.9 | 10.0~15.5 | ≥10 | |
Crushing Strength / MPa | 110℃ 24h | 87.5 | 20~30 | ≥80 |
1000℃ 3h | 122 | 49~70 | ≥90 | |
Linear Change Rate / % | 1000℃ 3h | 0.16 | 0.1~0.5 | 0.2 |
Thermal Shock Resistance / Cycle | 1000℃, air quenching | >40 | – | ≥40 |
Abrasion Resistance / cm3 | 3.24 | – | ≤6 |
Corundum-mullite wear-resistant and refractory castable
In China, a company in Guiyang announced an invention patent for “corundum-mullite wear-resistant and refractory castable”. Through the preparation of suitable binders, additives, wet mud, the added hardener is pure calcium aluminate cement. Then complete the preparation of the castable: wet mud 89%~96%(w), hardener cement 2%~6%(w), bonding agent 2%~5%(w). Since the aggregates in the wet mud are mainly corundum and mullite, the castable made is called corundum-mullite wear-resistant refractory castable. The physical and chemical properties of the castable are as follows: w(Al2O3)≥90%, w(SiO2)≥5%. Bulk density≥3.00g.cm-3, refractoriness 790℃, thermal shock resistance≥25 times. After 110℃24h, the compressive strength is ≥90MPa, the flexural strength is ≥12MPa, and the linear change rate is -0.2%~0.2%. After treatment at 1100℃ for 3h, the compressive strength is ≥160MPa, the flexural strength is ≥28MPa, and the linear change rate is -0.4%~0.4%.
High-strength alumina phosphate combined with corundum castable
Some refractory researchers use powdered solid alumina dihydrogen phosphate with w(P2O5)≥65% and w(Al2O3)≥17% as a binder. Adding 6%(w) MgO as a coagulant, and adding 0.15%(w) NH-66 as a corrosion inhibitor. Brown corundum particles 60% (w), corundum fine powder 40% (w), 3% ~ 5% (w) added to water, developed high-strength alumina phosphate bonded corundum castable, its physical and chemical properties are listed in Table 5.
Table 5 Physical properties of alumina phosphate combined with corundum castable
Table 5 Physical properties of alumina phosphate combined with corundum castable | |||||
Bulk Density / (g/cm3) | Flexural Strength / MPa | Crushing Strength / MPa | |||
110 ℃ | 815℃ | 110 ℃ | 815℃ | 110 ℃ | 815℃ |
3.15 | 3.10 | 20.5 | 21.2 | 90.1 | 105.? |