Metal aluminum is generally produced by cryolite-alumina molten salt electrolysis, and its main equipment is an aluminum electrolytic cell. The lining of the electrolytic cell of the aluminum melting furnace is made of materials such as carbon bricks, refractory bricks, and insulation bricks. During the production process of electrolytic aluminum, the tank lining is eroded by cryolite, Na, and NaF steam and aluminum liquid penetrates into the inner wall refractory bricks and insulation bricks through the cracks of carbon bricks. The carbon cathode penetrates into the insulation layer through the bottom of the tank, resulting in a reduction in the life of the aluminum electrolytic cell. For this reason, refractory material manufacturers have developed anti-seepage castables for side walls and anti-seepage castables for tank bottoms.
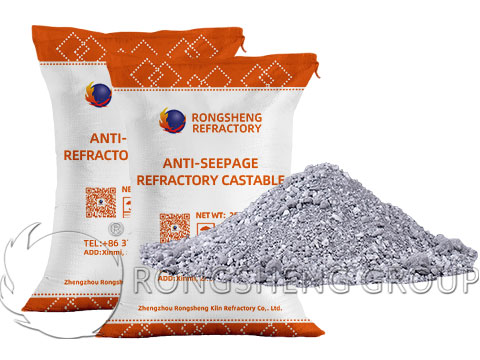
Selection of Refractory Lining for Aluminum Electrolyzer
The design and material selection of the electrolytic cell should ensure that the temperature inside the carbon cathode material is greater than 850°C. Because NaF will crystallize below 850°C, causing volume expansion of carbon cathode and bulging of carbon bricks, reducing its service life. The method is to use good insulation bricks as the insulation layer. At the same time, an anti-seepage material is used as a barrier layer between the carbon brick and the heat insulation layer to prevent the penetration of harmful substances such as NaF. The selection principle of anti-seepage castable is that m(Al2O3)/m(SiO2) is greater than 0.9, which can inhibit the penetration of NaF and Na.
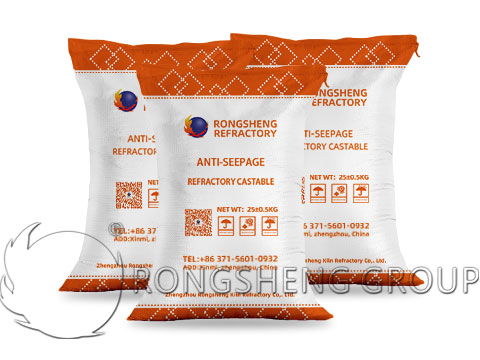
Anti-seepage castables for aluminum electrolytic cell
The impermeable castable has the characteristics of high strength, low thermal conductivity, and strong impermeability, which can prevent the infiltration and corrosion of molten aluminum and electrolyte. In order to achieve the purpose of prolonging the service life of the electrolytic cell. Prevent the electrolyte from entering the refractory insulation layer, increase its thermal conductivity, and increase the power consumption of the electrolytic cell. When in use, it can react with the alkali metal ions in the electrolyte to form a barrier, thereby achieving the purpose of anti-seepage. The anti-seepage material is convenient for construction, can quickly heat up without baking, and can be used as an anti-seepage layer instead of the refractory brick AI2O3 layer on the bottom of the electrolytic cell. The anti-seepage layer of the aluminum furnace bottom (that is, the pouring of the lower part of the bricklaying or pouring operation layer) prevents the molten aluminum from infiltrating. Or other colors of the impermeable layer at the bottom of the stove.
Compared with ordinary castables, anti-seepage castables have improved medium-temperature strength and load-softening temperature, reduced thermal conductivity, and good thermal stability. It also has impermeability, corrosion resistance, impact resistance, wear resistance, and high mechanical strength. The structure of the furnace body is complete, the air tightness is better than that of refractory brick furnaces, the service life of the furnace is extended, the cost of repairing the furnace is saved, and economic benefits are shown. It is mainly used in the selection of different parts of the lining of power stations, boilers, casting furnaces, heating furnaces, soaking furnaces, heat treatment furnaces, and induction furnaces.
The anti-seepage castable uses clay clinker as refractory aggregate and three-grade bauxite clinker as refractory powder. Add ultrafine powder, use CA-50 cement as a binder, and add dispersant and siliceous or feldspar anti-seepage agent. Its main properties: Al2O3 44%, SiO2 49%, bulk density ≥ 2.23g/cm³. The compressive strength after firing at 110°C and 1000°C is 40MPa and 70MPa respectively. The compressive strength after firing at 1000°C is 40MPa and 70MPa respectively. This material is used between the carbon brick on the side wall of the aluminum electrolytic cell and the heat insulation layer, which can prevent the penetration of NaF and Na and other substances, and also protect the heat insulation layer.
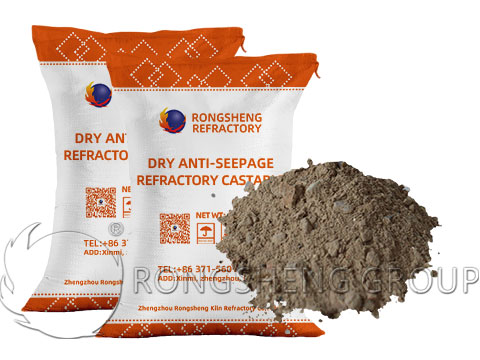
Dry anti-seepage castables material for aluminum electrolytic cell
Chemical anti-seepage material is also called anti-seepage and pouring material, also known as anti-seepage pouring material. It is not impermeable by itself, but can chemically react with penetrating electrolyte components to form a dry barrier in situ, preventing electrolytes from penetrating downward. That is, upon reaction with fluoride, a water-impermeable solid or glassy layer is produced. Materials of this nature include a group of minerals containing calcium silicates or calcium aluminum silicates. When some of these minerals react with fluorine at 900°C, the resulting reactants are all solid compounds, so the molten salt phase is dry. This product has a good anti-seepage effect of dry powder and plays a role in reducing power consumption, reducing furnace manufacturing costs, and prolonging the service life of the tank.
Rongsheng refractory material manufacturer, providing anti-seepage castables for aluminum electrolytic cells
Rongsheng Refractory Material Manufacturer is a powerful refractory manufacturer and sales company. Rongsheng’s refractory products have been sold to more than 70 countries and regions around the world. From customer inquiry to the delivery of samples to the completion of the final order, the perfect customer service of Rongsheng refractory manufacturers is also an inseparable part of the transaction of each order. Extend the service life of the refractory lining of the aluminum melting furnace. From the lining structure design to the selection of high-quality refractory materials to the construction of the refractory lining, and finally to the daily operation. Rongsheng refractory manufacturers can provide full guidance. To purchase anti-seepage castables for electrolytic cells of aluminum melting furnaces, please contact us. Neither our products nor services will disappoint you.