Aluminum Magnesium Castables are a general term for refractory castables with alumina and magnesia as the main components. Broadly called alumina-magnesia refractory castable, generally referred to as alumina-magnesia castable.
Application Range of Aluminum Magnesium Castables in Ladle Lining
The use of Aluminum Magnesium Castables on the overall inner lining of small and medium-sized ladle has been completely successful. In a large-capacity ladle, due to the different steel quality requirements and steelmaking process, the composition and basicity of the ladle slag are also different. Different types of ladle should use different refractory linings. When using pure aluminum-magnesium castable lining for a large-capacity ladle, the suitable type of pure aluminum-magnesium castable should be selected according to different types of ladle or different parts of the same ladle.
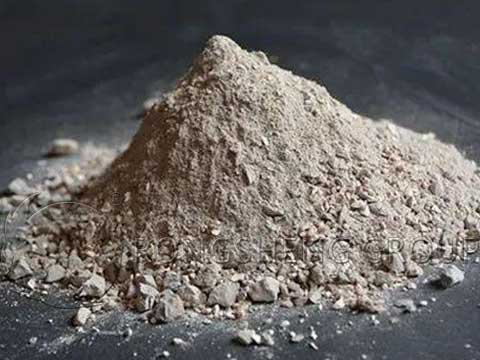
For large-capacity continuous casting ladle, the use of pure alumina-magnesia castable integral lining should be considered technically mature. However, special attention should be paid to the selection of pure Al2O3-MgO castables that can meet the requirements of corrosion resistance, slag permeability resistance, and permanent linear change rate at the slag line. For the refined ladle, which is mainly used for refining clean steel, due to the harsher conditions of use, pure Aluminum Magnesium Castables can only be used in the molten pool (wall and bottom of the ladle) in the low corrosion zone.
Application of Castables for Refining Ladle Slag Line
Over the years, the practice of brick ladle has proved that it is completely reliable in terms of service life and safety in use. However, the heavy physical labor of masonry operations has not been alleviated. The successful promotion and application of the integral lining of the ladle have made people see the prospect of mechanized construction of the lining. The overall increase in the penetration rate of lining is a major trend. At present, only the integral lining of the slag line of the refined ladle has not been fully succeeded and promoted. At home and abroad, for the alkaline castables at the slag line of the refined ladle, such as pure magnesium-aluminum castables, magnesium-silicon castables, etc. A lot of research and development work is being done, but none of them has reached the level of use of MgO-C bricks. The research and development of MgO-C castable for ladle slag line, due to fluidity and C’s oxidation resistance, etc. are not perfectly solved, its use effect is still not up to the level of MgO-C brick. However, the overall lining of the refined ladle is the direction of mechanized construction of the ladle lining.
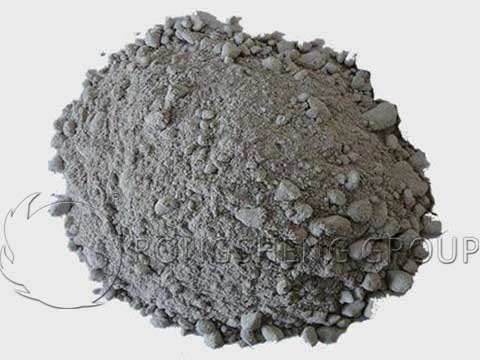
Selection of Pure Aluminum Magnesium Castables Types
Among the types of pure Aluminum Magnesium Castables for ladle, the choice of pure Al2O3-SP castable and pure Al2O3-MgO castable. It should be considered from the characteristics of each type, research and development history, and use effect.
First of all, we must understand the advantages and disadvantages of pure Al2O3-SP castables and pure Al2O3-MgO castables, so that they can be used reasonably in a different ladle and different parts of the same ladle. Of course, in order to maintain the advantages of pure Al2O3-SP castables and pure Al2O3-MgO castables and overcome their shortcomings. According to the principle of matrix matching, when the Al2O3-SP-MgO system is selected as the matrix composition and the SP/MgO ratio is appropriate, the advantages of having two types of castables can be obtained. It also overcomes its shortcomings and has a pure Al2O3-SP-MgO castable with better overall performance. It will get better results in the low corrosion area of the ladle.
Secondly, in the order of development and application, pure Al2O3-SP castable is better than pure Al2O3-MgO castable. It shows that the latter has more advantages than the former, and the applicability of the latter is wider. From the applicability of pure Al2O3-MgO castables, pure Al2O3-MgO castables with different compositions and characteristics can be used to refine any part of the ladle low-corrosion zone (melt pool wall, ladle bottom, and impact zone). Especially for a large amount of package wall, when pure Al2O3-MgO castables are used, the in-situ SP formed by the reaction of MgO and Al2O3 during use is accompanied by controllable and adjustable volume expansion, which is beneficial to reduce or limit slag penetration. What’s more, the pure Al2O3-MgO castable used for the clad wall, due to the radial expansion characteristics of the annular cast body and the restriction of the circular steel shell, the annular cast body will not undergo the so-called “free expansion”.
Third, the study on the corrosion mechanism of pure Aluminum Magnesium Castables for the ladle shows that the working lining of the cast body reacts with the slag to form a protective layer. Most of the iron oxide and manganese oxide in the slag are embedded in the lattice structure to form spinel. The expansion caused by the reaction of iron oxide Al2O3 to FeO·Al2O3 in the slag is not large. CaO in the slag reacts with Al2O3, resulting in greater expansion. However, the CaO and SiO2 in the slag react with Al2O3 to produce mayelite and/or anorthite. This depends on the SiO2 content in the slag and so on. When the melting point temperature is lower than the ladle operating temperature of 1600℃, the mineral reaction is balanced. The combination of pure aluminum-magnesium castable ladle working lining reacts with molten slag to generate a high melting point and low melting point minerals, which provides a hot surface protective layer for the ladle working lining, and minimizes further corrosion of the working lining. In the end, the difference between the different slag compositions on the service life of the two types of ladle working linings of pure Aluminum Magnesium Castables is not very obvious. In this way, the production process is relatively simple and low-cost pure Al2O3-MgO castable.
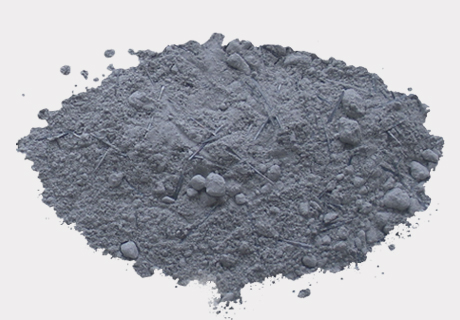
On the Promotion of Large-Capacity Ladle Integral Lining and “Casting”
After the successful application of the integrated lining of small and medium-sized ladles and some large-capacity ladles in China, the “casting” technology has been adopted. The overall inner lining is locally corroded to a certain thickness, cooled, and manually or mechanically removed the residue and the working lining permeable layer. Install the mold to refill the new integral lining, and put it into use after baking and heating. It can also be used for multiple times of “overcasting”, avoiding the waste of residual lining, and significantly reducing the unit consumption of refractory materials. The overall lining and overcasting are used together to show the superiority of ladle castables. Most large-capacity ladle in foreign countries adopt integral lining and sleeve pouring, but my country’s large-capacity ladle adopts integral lining and sleeve pouring less, which can create conditions to promote these technologies.
Rongsheng Ladle Refractory Castable Manufacturer
Rongsheng is a refractory castable manufacturer with an advanced and fully automatic unshaped refractory production line, with an annual output of 80,000 tons. Rongsheng’s refractory castable products have been sold to more than 60 countries and regions all over the world. For example, Russia, South Africa, Kazakhstan, Philippines, Chile, Malaysia, Uzbekistan, Indonesia, Vietnam, Kuwait, Turkey, Zambia, Peru, Mexico, Qatar, etc. Rongsheng manufacturers have extensive experience in the production and research and development of refractory materials for a ladle. If you need to buy refractory castable products for ladle, please leave your specific needs on our message form. We will provide you with refractory lining materials that best suit your production needs according to your specific needs.