As a common brick for glass furnaces, mullite bricks can be used in many parts of the glass furnace. As a manufacturer of mullite bricks, based on the production and sales experience of mullite bricks for many years, Rongsheng refractory manufacturers have summarized the application of mullite bricks in various parts of the glass melting furnace as follows.
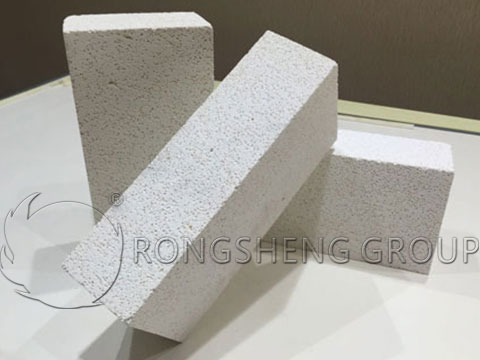
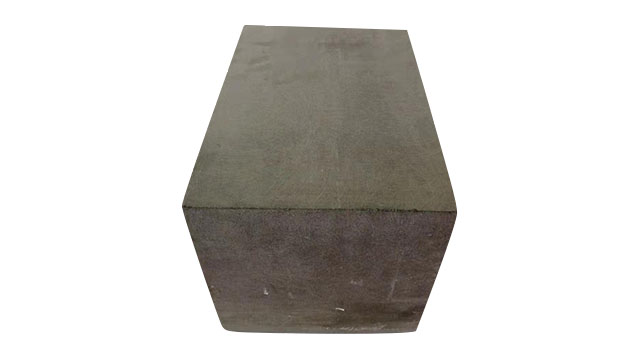
-
Front gable
The front wall of the glass melting furnace is adjacent to the batch area. Due to the large temperature fluctuations in this area and a large amount of raw material dust, the conditions are relatively harsh. Sintered mullite bricks have good resistance to rapid cooling and rapid heating, and have good resistance to batch dust erosion. Therefore, the suspension wall and the wing wall of the feeding port can be designed to use re-sintered fused mullite bricks.
-
Stuck neck
The neck is generally designed with a water bag and a stirrer. During equipment maintenance, there will be a large temperature difference in the neck space, so it is a better design choice to use sintered mullite bricks in this place.
-
Small furnace and the upper wall of the regenerator
The use of fused zirconia corundum bricks for small furnaces is the best design choice. Because mullite bricks, especially mullite bricks made of fused mullite, also have good resistance to the erosion of batch materials and alkali vapor. Re-sintered fused mullite bricks may be used in small furnaces, at least in the last few pairs of small furnaces, in order to improve the operating environment of small furnaces and reduce the cost of this part. Similarly, re-sintered fused mullite bricks can also be used for the upper wall of the regenerator. Compared with alkaline bricks, mullite bricks have lower thermal conductivity and expansion coefficient, which can reduce the expansion and deformation tendency of the kiln body and reduce the heat dissipation and heat preservation costs of the kiln body.
-
Coal-fired glass melting furnace small furnace ascending channel and tongue
As we all know, the bottleneck of the service life of the gas kiln lies in the small furnace. The traditional design here uses silica bricks equipped with fused zirconia corundum bricks for the tongue. Since the temperature here is lower than 1450°C, it is not the best choice to use silica bricks here. This part is severely corroded, and the good anti-corrosion performance of mullite bricks can prolong the service life of this part. In addition, the tongue is made of fused zirconia corundum bricks. Due to its poor thermal shock stability, it may be a better choice to use re-sintered fused mullite bricks.
-
Lattice body of gas regenerator
The grid body of the gas regenerator currently designed is made of clay bricks, and the general service life is 3 to 4 years, which cannot meet the needs of the longer and longer kiln life. Replacing checker bricks is not only labor-intensive but also causes damage to other parts of the kiln. A certain number of sintered mullite bricks are used on the top of the gas lattice body to increase the service life of the kiln.
-
Furnace grate and bottom lattice body
Flue gas condensate will be deposited at the bottom of the grid body of the regenerator, and the longer the kiln age, the more frequent the operation of the regenerator at the bottom. The furnace grate and bottom checker bricks need to experience more thermal shock, and the good thermal shock performance and erosion resistance of sintered mullite bricks can improve the service life of this part.
-
Operating hole
Mullite bricks have good thermal shock stability and high-temperature strength and can be used in each operation hole of the furnace. Such as observation holes, spray gun holes, air supply holes, and other parts.
-
Lattice under special conditions
The latest NOx emission standards have prompted more and more glass manufacturers to improve their production processes and operate in a reducing atmosphere to reduce NOx levels. This will lead to an increase in the concentration of alkali vapor (NaOH) in the flue gas, which will intensify the erosion of the lattice body. The re-sintered fused mullite brick has good resistance to alkali vapor erosion and can be used as a lattice configuration under this condition.
-
Special glass furnace configuration and use
1) Water glass melting furnace
The main component of water glass batch material is soda ash and silica sand, wherein the soda ash weight percent of flux varies according to the difference of water glass modulus, accounting for 25~45%. Compared with other glass products, the water glass batch material has a lower melting temperature and a higher concentration of alkali vapor in the flue gas. At present, silica bricks and high alumina bricks are mostly used in the flame space of domestic water glass melting furnaces. Although silica bricks and high alumina bricks have certain advantages in price, generally water glass furnaces have a short service life and high energy consumption. Comprehensive analysis shows that the use of sintered mullite bricks in water glass kilns has good economic benefits.
2) Oxygen glass melting furnace
The all-oxygen glass melting furnace is a combustion method in which oxygen replaces traditional air combustion. A large amount of N2 is reduced in the flue gas, which reduces the amount of flue gas and facilitates energy saving and consumption reduction. But at the same time, the concentration of alkali vapor and water vapor in the flue gas has also increased significantly, and the traditionally designed silica bricks have been replaced by fused zirconia corundum bricks and fused α, β bricks. Due to the problems of high price and difficult construction of electrically fused bricks, sintered materials such as calcium-free silica bricks produced by RHI and magnesium-aluminum spinel bricks produced by DSF have emerged as substitutes. Re-sintered fused mullite bricks produced by SEFPRO have been successfully used in fiberglass kilns for many years. Perhaps, sintered mullite bricks can also be promoted and used in all-oxygen furnaces for other glass products.
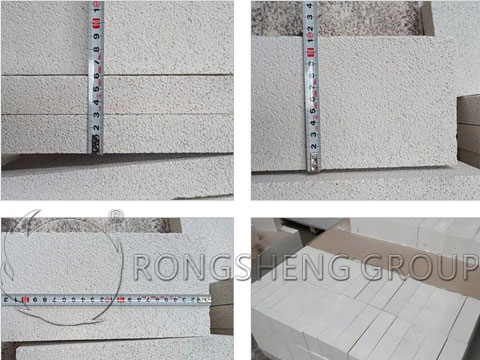
Application of Lightweight Mullite Bricks in Glass Furnace
The lightweight mullite brick hanger has an absolute advantage in performance. At present, the construction of electric melting furnaces with a melting area of more than 8m2 has basically adopted light mullite as the roof structure. From the point of view of small electric melting furnaces and large electric melting furnaces, this kind of mullite refractory brick is the development direction of hanging walls.
-
Application of lightweight mullite brick hanger in the small electric melting furnace
Small electric melting furnaces (melting area of 18m2, less than 1m2 is out of the scope of this article) can use the hanging tie. The main factor limiting its promotion is cost. At present, some domestic manufacturers have used it, but it has not been fully popularized. With the reduction of material costs and people’s emphasis on the reuse of resources, it is believed that there will be more space for the use of hanging rails in small electric melting furnaces.
-
Application of lightweight mullite brick hangers in large electric melting furnaces
With the gradual development of electric melting furnaces in the direction of a large melting area (melting area greater than 20m2) in recent years, new challenges have been put forward for the design of the hanging wall. Increased hanging area means increased weight. In order to ensure the reusability of the hanger, refractory brick manufacturers have created an original split hanger structure. That is to say, each arch body is divided into 3 parts, and each part bears an independent load and can be separately disassembled and hoisted during loading and unloading.