High chrome bricks use chromium oxide and alumina as the main raw materials, or introduce a small amount of zirconium oxide, and are fired at high temperatures to obtain a chromium oxide content of not less than 75%. Shaped refractory products with chromium oxide, alumina, and zirconium oxide content of not less than 98%. High chrome bricks are generally chromium oxide products produced with industrial pure chromium green as the main raw material.
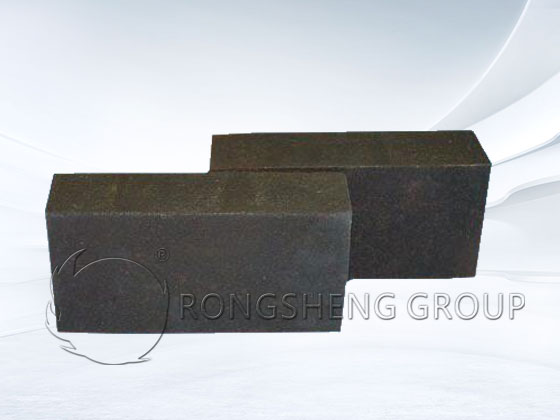
High Chrome Bricks
Chemical index Cr2O3(%): 80, 86, 90, 92, 93, 96
Bulk density (g/cm3): 4-4.65
Apparent porosity (%): 10-20
Cold pressing strength (MPa): 120-300
Load softening temperature (℃): ≥1670, ≥1700
Excellent Properties of High Chrome Bricks
High chrome bricks have the characteristics of excellent corrosion resistance, high normal temperature compressive strength, high-temperature strength, excellent wear resistance, high fire resistance, excellent thermal shock resistance, and good high-temperature volume stability.
Application of High Chrome Bricks
High chrome bricks are widely used in coal gasification furnace lining materials and coal water slurry pressurized gasification furnace working surface linings.
In the past, high-chromium refractory products were mainly used in reinforced glass furnaces and to a small extent in insulated glass pool furnaces. High chrome bricks are now increasingly being used in some soda-lime glass pool furnaces. Its main use is no longer limited to full or partial flow holes, but also to end walls and, to a limited extent, to corner bricks of feed openings. There is a potential risk of coloration due to the composition of high-chrome bricks, so high-chromium products are often incompatible with very “white” glass. Initially, this product was mainly used for colored glass, but now high chromium products have also been successfully used in clear container glass furnaces. The amount of high chromium products used in a glass melting furnace depends largely on the design of the flow hole, the cooling of the flow hole, the daily output of the pool furnace, and the operation of the furnace. A glass manufacturer may use high chrome bricks for the entire cover plus the end walls of the melting tank. High chrome brick masonry’s flow holes offer the potential to increase kiln life, as this material is at least twice as resistant to most glasses as fused brick. However, certain design and operating parameters differ from fused AZS bricks and need to be discussed with the supplier.
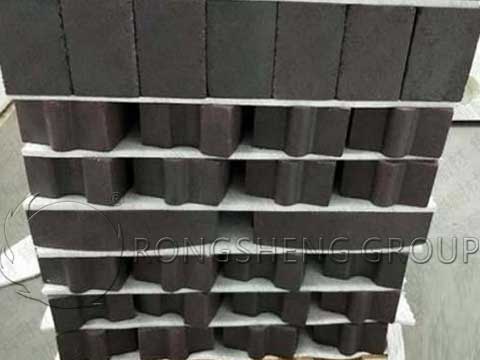
Rongsheng High Chrome Bricks
High chrome bricks refer to refractory bricks with a combined content of chromium oxide, alumina, and zirconia not less than 98%. Its models are: GGZ-75, GGZ-85, GGZ-90, GGZ-95.
High chrome bricks use industrial-grade chromium trioxide and alumina as the main raw materials or introduce a small amount of zirconia. After high-temperature firing, shaped refractory products with a chromium trioxide content of not less than 75% and a combined content of chromium trioxide, alumina, and zirconia of not less than 98% are obtained. It has the characteristics of good corrosion resistance, high normal temperature compressive strength, high-temperature strength, good wear resistance, high refractory resistance, thermal shock resistance, and good high-temperature volume stability.
High chrome bricks are divided into four grades based on chromium trioxide content: GGZ-75, GGZ-85, GGZ-90, and GGZ-95. G, G, and Z- in the brand name are the first letters of the Chinese pinyin of “Gao, Ge, and Zhuan” respectively. The Arabic numerals are the mass fraction of chromium trioxide.
Performance Characteristics of High Chrome Bricks
(1) Good resistance to slag erosion.
Cr2O3 material itself has good slag corrosion resistance, which is mainly due to the following points. 1) The solubility of Cr2O3 in coal slag is very low, thus ensuring the integrity of the material. 2) Most slag has poor wettability to Cr2O3 materials, which delays the dissolution of Cr2O3 in the slag. 3) After the Cr2O3 material is dissolved into the slag, it will increase the viscosity of the slag and even form a uniform protective layer on the surface of the material. Block the pores of the material and inhibit slag penetration.
(2) Good high-temperature performance.
The melting points of Cr2O3, Al2O3, and ZrO2, the main components of high chrome bricks, are approximately 2400, 2050, and 2700°C respectively. After high-temperature treatment at 1700°C, Cr2O3 and Al2O3 formed a well-crystallized and continuous aluminum-chromium solid solution. Therefore, high-chromium refractory materials have high high-temperature strength.
(3) Different erosion resistance properties.
The formation of aluminum-chromium solid solution and the burning-promoting effect of ZiO2. The high-chromium material has lower apparent porosity and higher compressive strength (up to 150 MPa or even more than 200 MPa). Therefore, high chromium refractory materials have good erosion resistance.
(4) Thermal shock resistance and thermal peeling resistance.
Due to the phase change toughening effect of ZrO2, the thermal shock resistance and thermal spalling resistance of high-chromium refractory materials are improved.
What are the Uses of High Chrome Bricks?
High chrome bricks can be used as working linings for coal-water slurry pressurized gasifiers and other related reducing atmosphere industrial furnaces. The high chromium bricks (Cr2O3≥90%) produced by Rongsheng Refractory Materials Manufacturer are mainly used in key parts of coal chemical industry, chemical industry kilns, alkali-free glass fiber kilns, waste incinerators, gasification furnaces, and other kilns. Chrome corundum bricks are mainly used for the lining of carbon black furnaces, copper smelting furnaces, molten pools of glass furnaces, slides of steel rolling heating furnaces, and tapping platforms. The external dimensions, physical and chemical indicators, and service life of the products have reached or exceeded the level of similar products at home and abroad.
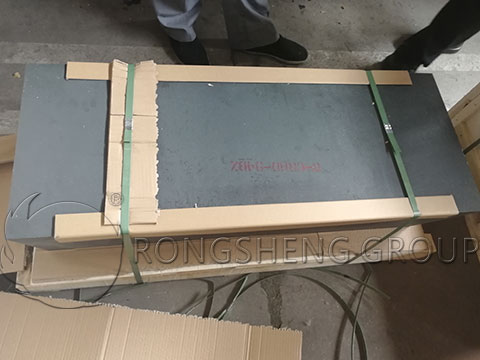
Why is Chrome Oxide Green Often Used to Produce High-Chrome Bricks?
Chromium oxide green is often used to produce high chrome bricks for the following reasons.
High chromium brick is an important refractory material, usually used in corrosive media at high temperatures, such as metallurgy, chemical industry, glass, and other industrial fields. Chromium oxide green, as a refractory pigment, has good high-temperature stability and corrosion resistance. It can remain stable in high temperatures and corrosive media without affecting the fire resistance of high chrome bricks.
Chromium oxide green can be mixed with high alumina cement and other oxides to form a high chrome brick formula. At high temperatures, high-alumina cement reacts with chromium oxide green to form a high-temperature stable chromium-aluminum spinel phase. This phase has good fire resistance and corrosion resistance, which can improve the service life and stability of high chromium bricks.
Chrome oxide green can also adjust the color and appearance of high-chrome bricks, making them more beautiful and practical. In the production process of high-chromium bricks. Chromium oxide green can be added as a pigment to mixtures of high-alumina cement and other oxides. The high-chrome bricks appear bright green, enhancing their beauty and recognition.
Therefore, chromium oxide green, as an excellent refractory pigment, is often used to produce high-chrome bricks. Its stability and corrosion resistance, as well as its compatibility and compatibility with other materials such as high alumina cement. These are all important reasons that make it one of the ideal materials for the production of high-chromium bricks.