The strength change characteristics of refractory castables are closely related to the hydration products of aluminate cement and the physical and chemical changes after heating. The microscopic changes in the heating process of aluminate cement are reflected macroscopically in the strength change characteristics of its refractory castables. Relative compressive strength is calculated at 110°C (drying compressive strength is 100%).
After the initial setting of CA-70 cement refractory castable, when cured under standard conditions, the hydration rate is slow and the strength is low. Therefore, steam curing is generally used to speed up the hydration rate and improve the strength; after drying, its strength still decreases.
After the CA-50 cement refractory castable is formed and initially set, standard curing can achieve high strength at room temperature, and the strength decreases significantly after drying. This is due to the crystal form transformation of the hydration product and the elimination of free water; after heating at a temperature of about 300°C, the crystal form transformation is rapid and free water is eliminated. Therefore, the relative intensity decreases more.
Generally, it is 18%~25%. After heating at 800℃~1200℃, the strength can be improved due to solid phase reaction, generation of new products and emergence of liquid phase. However, the cement has lost its cementing effect and undergone significant crystalline transformation, resulting in the strength of the refractory castable being reduced to the lowest value, generally 45% to 55% of the dry strength. When observed under a microscope, the tissue structure of the sample burned at 1200°C is composed of blocks that are separated from each other and have similar sizes, so the strength is the lowest. After heating at 1300~1400℃, the strength rebounds and increases significantly, which is the result of the formation of stable products and the realization of ceramic bonding.
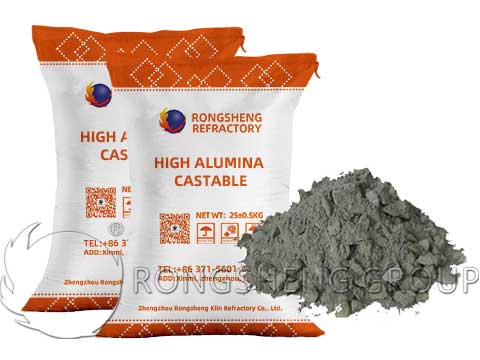
Improving the Medium-Temperature Strength of Refractory Castables
(I) Mechanism of medium-temperature strength reduction
Medium-temperature strength refers to the strength at 900℃~1200℃. The medium-temperature strength reduction of aluminate cement refractory castables is a general rule, especially for CA-50 cement refractory castables, which have a large medium-temperature strength reduction and is representative. Compared with the drying strength, the reduction rate of the medium-temperature strength of this castable is 22%~60%.
At a temperature of 900℃~1200℃, the hydrated calcium aluminate of CA-50 cement refractory castable has basically been secondary CA and CA2-formed, resulting in volume shrinkage and internal pores due to chemical reactions. Before 900℃, about 90% of the free water and part of the bound water are removed, and the strength reduction is small, and the porosity increases greatly. The remaining 6%~10% of bound water may be bound water that enters the coordination structure and exists in the form of hydroxyl groups. When it is removed between 900℃ and 1200℃, the original lattice is destroyed and a new mineral structure is formed, namely secondary CA and CA2.
At the same time, due to the low temperature, the sintering effect is not obvious and its structure is loose. Therefore, the strength decreases significantly. In other words, the decrease in medium temperature strength within this temperature range is due to the fact that ceramicization and hydration mineral chemical reactions have not yet formed to form a loose structure and cause volume shrinkage.
(II) Measures to improve the medium-temperature strength of refractory castables
In aluminate cement refractory castables, adding α-AL2O3 fine powder will produce a chemical reaction with expansion effect at medium temperature, which can compensate for the decrease in medium-temperature strength caused by volume shrinkage. The reaction formula is as follows:
CaO+AL2O3→CaO·AL2O3 (Formula 1)
CA+AL2O3→CA2 (Formula 2)
After calculation, the volume expansion effect of Formula 1 is 19.6%, while that of Formula 2 is 12.86%. After adding α-AL2O3 to cement refractory castables, the medium-temperature strength does not decrease, but increases due to the increased shrinkage compensation effect (i.e., increased expansion rate). The decrease in medium-temperature strength of CA-50 cement refractory castables is reduced, and its decrease rate is only 12%.
In CA-50 cement refractory castables, adding sintering agents can also improve medium-temperature strength. Sintering agents mainly include soft clay, etc., and the dosage is 3%~6%. Its function is to make the castable sintered at a lower temperature, and prevent or improve the drastic change of its organizational structure, thereby improving the medium-temperature strength. Some of them are even better than the drying strength.
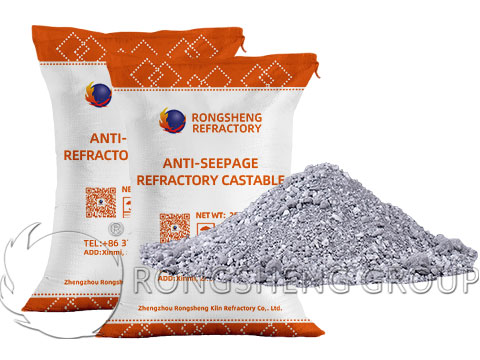
High-Strength Anti-Seepage Castable
The production process of high-strength anti-seepage castable
High-strength anti-seepage castable is made of alumina particles, alumina fine powder, pure calcium aluminate cement, silica powder, and composite anti-seepage additives. And 0.12% of sodium tripolyphosphate and 0.03% of polysilicon acid salt are added as dispersants. Silica sol is added during construction and mixing, and the mixture is mixed evenly, and vibrated and casted at the furnace construction site. It can be used after routine maintenance and baking.
Formula of high-strength anti-seepage castable
The main anti-seepage material is based on the traditional ratio, with the particle grading adjusted, different admixtures added, and cement consumption reduced. Other production procedures are the same as general castables. The anti-seepage material uses clay clinker as refractory raw material, third-grade bauxite clinker as refractory powder, adds ultrafine powder, uses CA-50 cement as binder, and dispersant and siliceous or feldspar anti-seepage agent. This high-strength anti-seepage castable is used between the carbon bricks and the insulation layer of the side wall of the aluminum electrolytic cell. It can prevent the penetration of aluminum liquid and other substances, and also protect the insulation layer. The anti-seepage castable has the characteristics of high strength, low thermal conductivity, and strong anti-penetration. Prevent the penetration and corrosion of aluminum liquid and electrolyte. It is widely used in different parts of the furnace lining such as melting furnaces, heating furnaces, soaking furnaces, heat treatment furnaces, etc.
To purchase high-quality high-strength castables, please choose Rongsheng refractory manufacturer. Our environmentally friendly fully automatic monolithic refractory production line provides high-quality monolithic refractory products for furnace linings. And our comprehensive customer service also provides a guarantee for the long life of the furnace lining. Our refractory products have been sold to more than 120 countries around the world, such as South Africa, Chile, Egypt, Colombia, Uzbekistan, Italy, Indonesia, Ukraine, Hungary, Spain, Kenya, Syria, Zambia, Oman, Venezuela, India, Peru, the United States, Ethiopia, etc. Contact us for free samples and quotes.