High-purity refractory castables refer to refractory castables made of fused corundum, a-Al2O3 ultrafine powder, and CA-70 or 80 cement. Sometimes, raw materials such as fused magnesia powder, alumina-rich spinel powder, and Cr2O3 powder are added during the production process. Among them, CA-70 or 80 cement is what we often call Castable Cement CA 70/80. Due to its good high-temperature resistance, it is also called refractory cement.
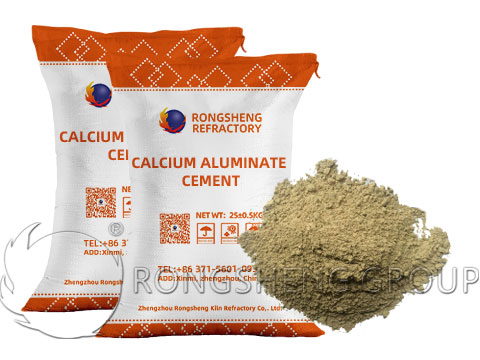
CA 60/80 Refractory Cement for Castables
Refractory cement, as a key component in refractory materials, is often widely used in the mixing of refractory castables. Many manufacturers also purchase refractory cement separately to meet specific needs. However, due to insufficient knowledge of refractory cement, users often face many confusions, such as what type of refractory cement to choose, how to use it correctly, and how to interpret the various labels when purchasing. In addition, problems that occur during use, such as cracking, shedding and peeling, are often mistaken for cement quality problems, but in fact, these may be caused by improper operation or wrong selection. Rongsheng Refractory Material Factory can help you better choose refractory cement, Castable Cement CA 60/80. Contact Rongsheng for free details.
Castable Cement CA 60/80, refractory cement, also known as aluminate cement, is a special cement designed for the field of refractory materials. Its production process is rigorous, with selected bauxite and lime as raw materials, sintered into raw materials after precise proportioning, and then aluminate extracted from it as the core component. At the same time, the alumina content is ensured to reach about 50%, thus producing clinker. This clinker is finely ground and finally becomes a fine powder, namely refractory cement. It not only has excellent fire resistance but also is a hydraulic cementitious material that can maintain stable structure and strength in high-temperature environments.
Refractory Cement Label
Like the various logos printed on its packaging, it represents the national standards and corresponding performance followed by the product. According to the provisions of my country’s standard GB201-2000, aluminate cement is given a specific code CA, and its classification is defined based on the percentage of alumina (Al2O3).
Specifically, aluminate cement can be divided into the following categories:
- CA-50: The alumina content is between 50% and 60%, often referred to as 50 cement, and is the most common refractory cement in daily applications.
- CA-60: Its alumina content is between 60% and 68%, so it is named 60 cement.
- CA-70: This type of cement has an alumina content between 68% and 77%, and is referred to as 70 cement.
- CA-80: When the alumina content exceeds 77%, it is called 80 cement. It is worth noting that CA-70 and CA-80 cements are often referred to as pure calcium aluminate cement in the industry.
In addition, we will also encounter designations such as CA-50-G6, CA-50-625, CA50-A600, etc. They all convey a common message: the alumina content of these aluminate cements is about 50%, and the compressive strength within three days can reach about 62.5MPa. Similarly, the designations such as G7/725/A700 indicate that the compressive strength of the cement within three days can reach about 72.5MPa. These detailed classifications and designations provide important references for our refractory cement selection.
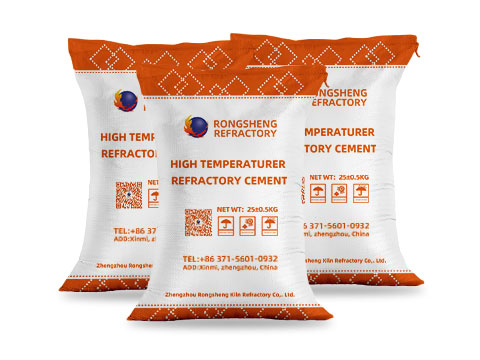
Characteristics of Refractory Cement
First, let’s take a closer look at the fineness of refractory cement. The fineness of cement, that is, the coarseness and fineness of cement particles, has a significant impact on the performance of cement. The finer the particles, the larger the specific surface area of cement, thereby enhancing its ability to react with water. This sufficient hydration reaction not only increases the reaction speed, but also ensures that the cement can maintain high strength in both the early and later stages. According to national standards, high-quality refractory cement should have a specific surface area of at least 300 square meters/kilogram, which is an important guarantee for its superior performance.
Secondly, setting time is also one of the key characteristics of refractory cement. During the construction process, the initial setting time, that is, the moment when cement begins to lose plasticity, needs to be reasonably arranged to ensure that construction personnel have enough time to operate. The final setting time, that is, the time when cement completely loses plasticity and begins to generate strength, should be shortened as much as possible to ensure that the hardness after construction quickly reaches the requirements. According to regulations, the initial setting time of silicate cement should not be earlier than 45 minutes, and the final setting time should not be later than 390 minutes. Such a time range not only ensures the smooth progress of construction, but also gives full play to the performance of high alumina cement.
Finally, we have to mention the volume stability of refractory cement. This is an important indicator to measure whether the volume change of cement paste is uniform during the setting and hardening process. If the volume change is uneven, that is, the volume stability is poor, then problems such as curling and cracking may occur during use, seriously affecting the quality of the project and even causing safety accidents. Therefore, volume stability is an indispensable aspect when evaluating the performance of refractory cement.
Precautions for the Use of Refractory Cement
In the construction and application of refractory materials, a common misunderstanding is to confuse refractory cement with refractory clay. However, there is a significant difference between the two. If the two are mixed by mistake, the performance of refractory cement will be seriously affected, and its solidification strength and grade will be significantly reduced.
Therefore, I would like to remind the workers who have been engaged in furnace construction for a long time: in the construction process of refractory materials, it is necessary to strictly distinguish refractory cement and refractory clay, and avoid mixing them. Only in this way can we ensure that the performance of refractory cement is fully released and provides long-lasting and stable protection for equipment. I hope that every worker friend can realize this and contribute our strength to the safety of buildings and equipment.