What lightweight refractory materials are used in ceramic kilns? Modern ceramic kilns use three categories of lightweight refractory materials: insulating bricks, refractory fibers, and calcium silicate. Improve the calcining efficiency of the kiln by enhancing heat insulation and reducing heat absorption. It can reduce energy consumption, increase kiln output, and improve the quality of ceramic products produced.
Requirements for Thermal Insulation Performance of Ceramic Kilns
Thermal insulation is an important link and means for energy saving and consumption reduction in ceramic kilns. Due to factors such as space and structure, the thickness of the kiln body cannot be very large. Therefore, it is necessary to choose insulation materials with good thermal insulation performance within the allowed size to reduce the surface temperature of the kiln body and reduce heat loss.
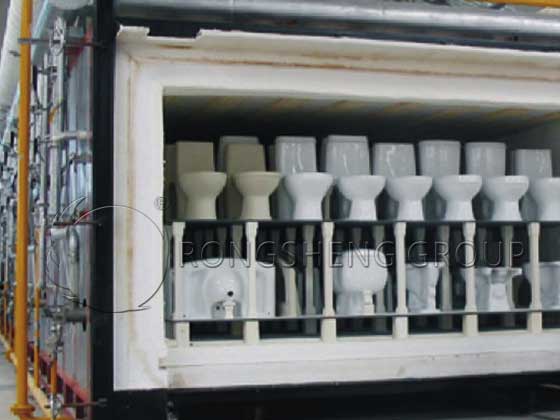
Requirements for Heat Storage of Refractory Bricks in Ceramic Kilns
Ceramic kilns need to reduce the heat storage of refractory bricks for the following two reasons.
(1) Reduce the heat loss caused by the increase in heat storage in the kiln.
For the kiln car materials, kiln furniture pillars, shed boards, etc. of the continuous kiln, the lighter the mass and the smaller the specific heat capacity, the less heat is taken out of the kiln, and the smaller the heat consumption of the kiln for firing unit products. For refractory bricks used in intermittent ceramic kilns, kiln bodies, kiln cars, etc., the heat storage of the refractory bricks should also be minimized to make the kiln heat up and cool down quickly and reduce the heat loss per firing cycle.
(2) Reduce the thermal hysteresis of the kiln.
Modern kilns use computer-controlled firing. If the kiln refractory bricks store too much heat, their thermal inertia will also be large. The control accuracy of the automatic control system is reduced, which is not conducive to improving the quality of fired products. More importantly, the residence time of the kiln car in the kiln can be shortened, thereby saving a lot of energy.
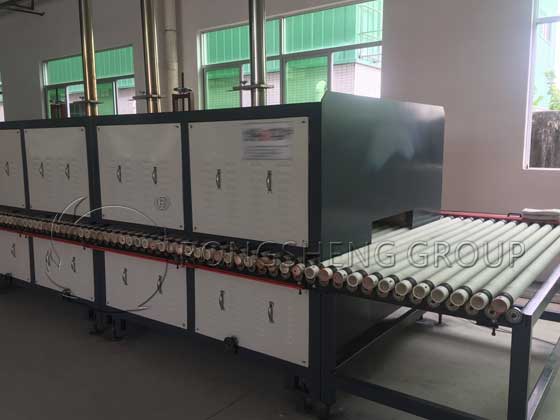
The Development Direction of Refractory Bricks for Ceramic Kilns
With the development of ceramic firing technology, new energy-saving kilns are constantly emerging. Different parts of ceramic kilns place the following requirements on the performance of refractory materials.
- Refractory bricks with good high-temperature mechanical properties and good thermal shock resistance are used as the skeleton of the kiln. Such as kiln furniture, etc.
- Use insulation materials with good thermal insulation properties, such as refractory fibers.
- The kiln body structure is made of materials that have both good high-temperature mechanical properties and good thermal insulation properties.
Energy saving is the theme of kiln development. The refractory materials used in new kilns have outstanding high-temperature resistance in certain circumstances. Due to its better high-temperature mechanical properties, its thermal insulation function can be ignored. However, in another case, in some parts of the ceramic kiln, the thermal insulation properties of the material are mainly used, and the high-temperature mechanical properties of the material are not considered. These two materials are used together throughout the construction of the ceramic kiln. For ceramic kilns, the most ideal material is its high-temperature resistance and thermal insulation properties. This simplifies the design and manufacturing of the kiln, and it will be a key development of new refractory materials.
Refractory Bricks Commonly Used in Ceramic Kilns
Clay refractory bricks. Clay refractory bricks used in ceramic kilns are mainly used for the inner parts of the kiln that are in contact with the flame to resist high temperatures and support the kiln structure. Usually, for continuous kilns, ordinary clay bricks are used where the furnace temperature is below 1000°C. Various holes, passages and other structures in the kiln body (such as smoke exhaust outlets, flues, etc.) are built with clay bricks or large clay slabs.
High alumina refractory bricks. Ceramic kilns mostly use high-alumina refractory bricks in the combustion chamber and high-temperature areas where the kiln temperature is higher than 1000°C. Such as building tunnel kiln vaults, kiln burner bricks, etc. The use of more high-alumina special-shaped refractory bricks is also a feature of ceramic kilns.
Corundum bricks. Corundum bricks are mainly used in the combustion chamber of ceramic kilns.
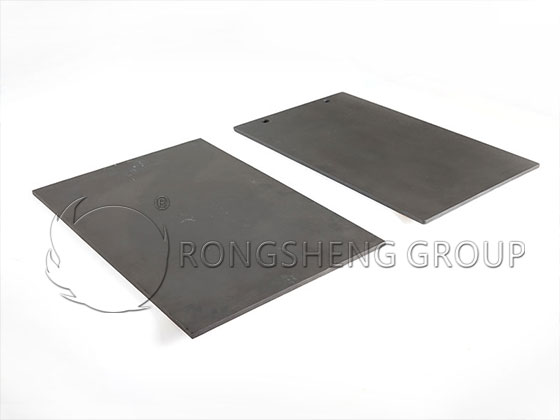
Silicon carbide refractory bricks.
Due to the good high-temperature strength of silicon carbide refractory bricks, they are used as shed boards, pillars, beams, etc. for kiln cars in ceramic kilns. And because it has good heat conduction properties, it is used as a flame muffle plate in flame muffled ceramic kilns. According to the type of binder, the following silicon carbide refractory bricks are commonly used in ceramic kilns.
- Clay bonded silicon carbide refractory bricks. The biggest feature of clay-bonded silicon carbide refractory bricks is that the production technology is not complicated and the price of refractory bricks is low. It is mostly used in flame retardants, kiln furniture, shed boards, pillars, etc. in medium and low-end kilns.
- Self-bonding silicon carbide, also known as recrystallized silicon carbide. Because this material has good high-temperature strength, it is often used in ceramic kilns to support beams for kiln cars and rollers for sanitary porcelain roller kilns. Burner, combustion chamber, etc.
- Silicon nitride bonded silicon carbide refractory bricks. This type of refractory brick has high strength, with a compressive strength greater than 200MPa and a tensile strength of 19MPa at 1000°C. It has good thermal shock resistance and can be water-cooled at 900℃ for more than 100 times. The softening under load starts at a high temperature, reaching a maximum temperature of 1800°C. Therefore, it is widely used in burner nozzles, kiln furniture beams, and rollers in sanitary porcelain roller kilns in ceramic kilns.
Unshaped refractory materials. Ceramic furnaces commonly use refractory castables to precast kiln walls, cast kiln cart tables, and complex-shaped burner bricks.
Rongsheng Refractory Materials Manufacturer is a powerful manufacturer and seller of refractory materials. We can provide high-quality furnace wall refractory materials and furnace top insulation materials for ceramic kilns. Contact us for free customized ceramic kiln refractory lining solutions. In addition, we also provide free samples and quotations.