Alkaline refractory bricks are a kind of refractory material mainly composed of magnesia raw materials. They have excellent slag erosion resistance, thermal shock resistance, and high-temperature structural stability. In industries such as metallurgy, building materials, and chemicals, basic refractory bricks are widely used in the lining of high-temperature equipment such as furnaces, cement rotary kilns, and glass kilns. Rongsheng Refractory Materials Manufacturer, based on years of production and sales experience, has summarized the practical characteristics and application locations of various alkaline magnesia refractory bricks. This article will introduce in detail the types of basic refractory bricks and their magnesium content.
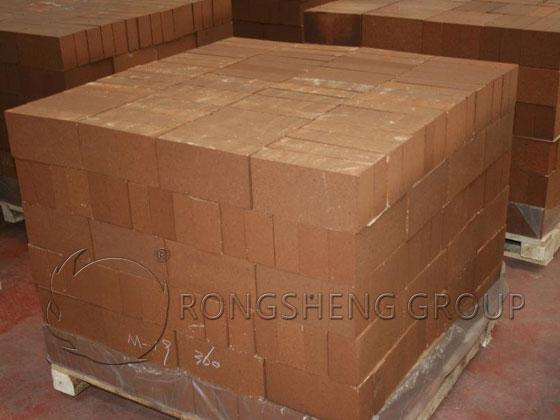
Types of Alkaline Refractory Bricks
- Magnesia chrome bricks. Magnesia chrome brick is an alkaline refractory brick made of magnesia and chromite as the main raw materials and sintered at high temperatures. Magnesia chrome bricks have the advantages of high melting point, high strength, and high resistance to slag erosion. Suitable for working conditions under high temperature, high pressure, and strong alkali environment.
- Magnesia-alumina bricks. Magnesia-alumina brick is an alkaline refractory brick made of magnesia and alumina as the main raw materials, adding an appropriate amount of additives, and sintering at high temperatures. Magnesia-alumina bricks have good thermal shock resistance, slag erosion resistance, and high-temperature structural stability. Suitable for lining high-temperature equipment such as cement rotary kilns and glass kilns.
- Magnesia calcium brick. Magnesia-calcium brick is an alkaline refractory brick made of magnesia and lime as the main raw materials, adding an appropriate amount of additives and sintering at high temperatures. Magnesia-calcium bricks have high thermal shock resistance and slag erosion resistance and are suitable for high-temperature equipment in steel, non-ferrous metals, and other industries.
- Magnesium dolomite bricks. Magnesia dolomite brick is an alkaline refractory brick made of magnesia and dolomite as the main raw materials, adding an appropriate amount of additives, and sintering at high temperatures. Magnesium dolomite bricks have good thermal shock resistance, slag erosion resistance, and high-temperature structural stability. Suitable for lining high-temperature equipment such as cement rotary kilns and glass kilns.
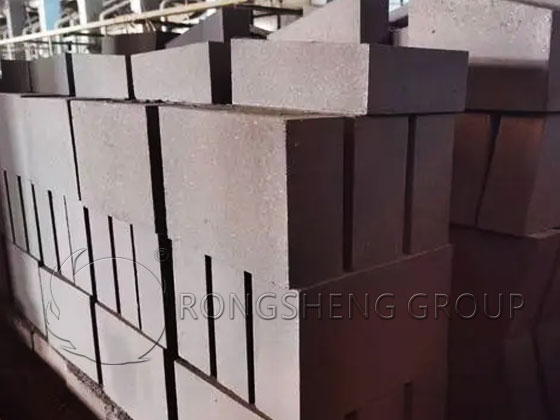
Magnesium Content of Alkaline Refractory Bricks
- Magnesia chrome bricks. The magnesium content of magnesia-chrome bricks is generally between 60% and 80%, and the chromium content is between 20% and 40%. The magnesium content of magnesia-chrome bricks is high, which is beneficial to improving their resistance to slag erosion and high-temperature structural stability.
- Magnesia-alumina bricks. The magnesium content of magnesia-alumina bricks is generally between 50% and 70%, and the aluminum content is between 20% and 40%. The magnesium content of magnesia-alumina bricks is moderate, which is beneficial for improving their thermal shock resistance and slag erosion resistance.
- Magnesia calcium brick. The magnesium content of magnesia-calcium bricks is generally between 50% and 70%, and the calcium content is between 20% and 40%. The magnesium content of magnesia-calcium bricks is moderate, which is beneficial for improving their thermal shock resistance and slag erosion resistance.
- Magnesium dolomite bricks. The magnesium content of magnesia dolomite bricks is generally between 50% and 70%, and the dolomite content is between 20% and 40%. The magnesium content of magnesia dolomite bricks is moderate, which is beneficial to improving its thermal shock resistance and slag erosion resistance.
Precautions for Using Alkaline Refractory Bricks
When selecting alkaline refractory bricks, the appropriate type and magnesium content should be selected based on specific working conditions and requirements.
When laying alkaline refractory bricks, attention should be paid to controlling the size of the brick joints, generally between 2-3mm. Excessive brick joints will lead to increased heat loss, while brick joints that are too small are not conducive to the expansion and contraction of the brick body.
During the masonry process, special anchors should be used to fix the refractory bricks on the base body to prevent the bricks from loosening and falling off. The selection and installation of anchors should comply with design requirements and construction specifications.
After the masonry is completed, the bricks should be trimmed and excess mortar should be removed to make the brick surface smooth and beautiful.
In short, alkaline refractory brick is a refractory material with excellent properties and is widely used in high-temperature equipment in metallurgy, building materials, chemical industry, and other industries. When selecting and using basic refractory bricks, the appropriate type and magnesium content should be selected according to the specific working conditions and requirements to ensure the safe and stable operation of the equipment.
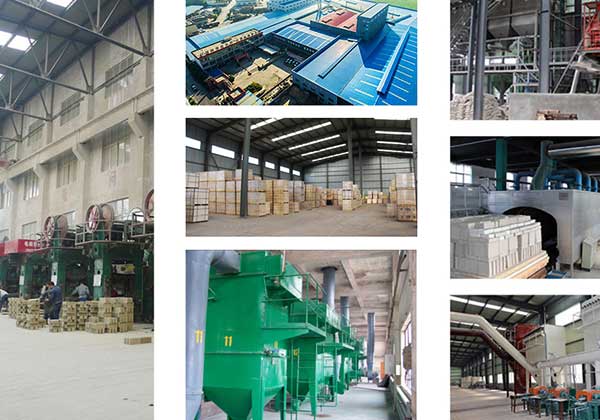
Application of Alkaline Refractory Bricks
In the refractory industry, refractory bricks with MgO as the main component and periclase as the main crystal phase are collectively called alkaline refractory bricks. Basic refractory bricks are mainly used in thermal kilns used in cement, glass, ferroalloy, and other industries.
Taking the glass melting furnace as an example, alkaline refractory bricks are mainly used as checker bricks in the regenerator. They have high thermal conductivity, long service life, and high volume density, which increase the heat storage in the regenerator. The porosity of basic refractory bricks is low, and the thermal expansion coefficient increases linearly as the temperature rises. It is the largest among various refractory materials. Care should be taken to leave sufficient expansion joints during use.
Alkaline refractory bricks are non-insulators above 900°C and have very good conductivity and cannot be used as high-temperature insulating materials.
Alkaline refractory bricks cannot be used in gas regenerators, and hydration will occur when exposed to water vapor for a long time at 40 to 160°C, which will cause the brick structure to become loose and damaged, so they must be kept dry during storage. Before laying the checkered bricks, the regenerator must be dried.