Application of silicon carbide refractory bricks in aluminum electrolytic cells. The electrolytic cell is an important component in the aluminum electrolysis process, and the two main factors affecting the life of the aluminum electrolytic cell are the carbon cathode and the lining refractory material. Rongsheng refractory material manufacturer can provide refractory materials for aluminum electrolytic cells, including various silicon carbide refractory bricks, refractory castables, etc. Contact Rongsheng for more information.
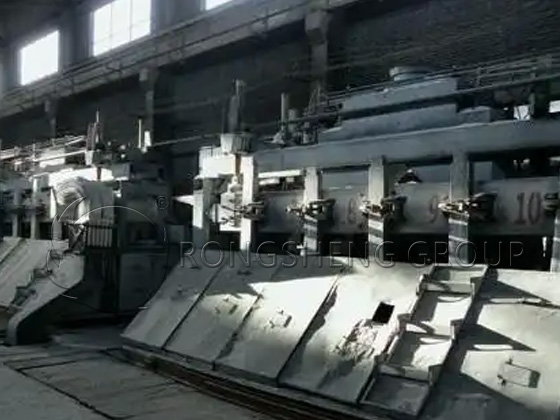
Lining Configuration of the Aluminum Electrolytic Cell
The lining of aluminum electrolytic cell can be divided into bottom lining and side lining according to the area. Functionally, the bottom lining plays the role of supporting the cathode structure and heat preservation. The side lining mainly plays the role of protecting the steel metal shell surface from the erosion of the electrolyte melt.
The side lining of the aluminum electrolytic cell is an important structural part of the electrolytic cell. According to modern concepts, it is proposed that the side wall material of the aluminum electrolytic cell should have the following important properties at high temperature: high resistivity, good thermal conductivity, no chemical reaction with molten cryolite, small porosity, impermeability to electrolyte and aluminum, and no oxidation by air.
Due to the valence bond structure characteristics of silicon carbide, it has a series of excellent properties. Such as high strength, high hardness, high temperature resistance, and oxidation resistance. High thermal conductivity, low thermal expansion rate, excellent thermal shock resistance, good chemical stability, and no wetting by non-ferrous metals. And it has good resistance to high temperature chemical corrosion, which is particularly suitable as a refractory material for the lining of aluminum electrolytic cells.
With the development of material technology and the increase in the capacity of electrolytic cells, the material structure of the inner lining of the electrolytic cell side has gradually evolved from the early double carbon blocks plus insulation bricks structure to no insulation bricks, single-layer carbon blocks, and even to today’s separate silicon carbide combined with silicon nitride materials.
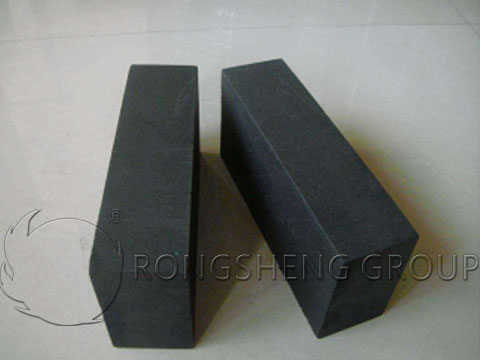
Damage of Silicon Carbide Refractory Bricks in Aluminum Electrolysis Cells
Silicon carbide refractory bricks are a new type of furnace building material recently promoted and used by my country’s nonferrous industry. They were first used in 320kA large prebaked aluminum electrolysis cells. In recent years, the use of enterprises has shown that whether pure silicon carbide refractory brick side blocks or composite side blocks are used, different degrees of fracture and shedding are generally found in the production process, and the silicon carbide layer of the composite side blocks is also lifted.
Temperature difference (bounded by the upper edge of the artificial leg extension) is the main cause of the fracture of silicon carbide bricks. Although silicon carbide bricks have good thermal conductivity and low thermal expansion coefficient. However, because the products are fired at a high temperature of more than 1450℃, a hexagonal ceramic body is formed. Therefore, the thermal vibration resistance and temperature difference resistance are poor. In an environment where the upper and lower parts of the silicon carbide refractory bricks repeatedly form a temperature difference, it is very easy to break.
When the silicon carbide composite layer breaks, the electrolyte penetrates into the cracks. When the electrolytic cell returns to normal temperature from the effect temperature, the electrolyte in the crack solidifies and shrinks, and new electrolyte enters the crack and solidifies again. When the next effect occurs, the solid electrolyte immersed in the crack expands due to heat and lifts up the upper broken block. When the cell temperature returns to normal, the electrolyte solidifies and shrinks again to form a gap. Then new electrolyte enters and solidifies again. When the effect comes again, it expands again to push up the broken block. This repeated action gradually lifts up the upper part of the fracture.
During the electrolytic aluminum process, the temperature is close to 1000℃. At this time, the erosion of the electrolytic cell lining is mainly divided into three parts. The metal aluminum melt near the bottom, the molten electrolyte in the middle, and various corrosive gases in the upper part (such as HF, AINAF4, etc.). Usually, in the electrolyte. Alumina melt, the cation penetration is mainly Na+ ore, and the anion penetration is mainly F–.
Various factors such as porosity, matrix phase, and wettability can affect the corrosion resistance of refractory materials. Materials with high porosity and large pore size must have poor corrosion resistance, because cryolite or aluminum liquid can directly penetrate into the material. The limit pore size of molten metal to refractory materials is 30μm for molten steel, 5μm for molten iron, and 0.5μm for molten aluminum. Therefore, the penetration ability of aluminum liquid to materials is quite strong. The matrix phase is thin and the corrosion resistance is good, but the strength will be directly affected. The thick matrix phase has poor corrosion resistance. If the wetting angle between the material and the aluminum liquid is large, its corrosion resistance is excellent.
The resistance of SiC materials with various bonding phases to electrolyte erosion is the best among all materials except self-bonded SiC. Although the Si3N4 bonding phase is wetted by the melt, the penetration is very shallow and there is no decomposition.
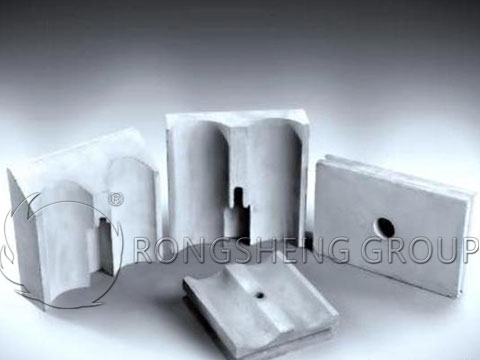
Silicon Nitride Combined with Silicon Carbide Bricks for Aluminum Electrolytic Cells
With silicon carbide and metal silicon powder as the main raw materials, the process parameters such as molding process, nitriding firing temperature, holding time, N2 flow rate and furnace pressure have been optimized and innovated. By controlling the nitriding reaction rate, large-scale silicon nitride combined with silicon carbide products with a thickness of 80-176mm with excellent performance, stable quality and good use effect have been successfully developed. The large-scale silicon nitride combined with silicon carbide products with a thickness of ≥80mm developed have been used in aluminum electrolytic cells of many aluminum companies. The total amount is more than 2,200 tons, the use effect is good, and significant economic and social benefits have been achieved.
Silicon nitride combined with silicon carbide has become the first choice for the lining of the electrolytic cell. Silicon nitride combined with silicon carbide products are a new generation of high-performance refractory materials for the lining of aluminum electrolytic cells, and have become the preferred material for the renewal of aluminum electrolytic cells.
The main advantages of using silicon nitride combined with silicon carbide products in the lining of aluminum electrolytic cells are as follows:
(1) Reduce the horizontal current of the cell, increase the heat dissipation on the side, reduce the cell temperature, and improve the current efficiency. Reduce DC power consumption, which plays a role in energy saving and consumption reduction.
(2) Extend the service life of the electrolytic cell. Silicon nitride combined with silicon carbide has good thermal conductivity, and good resistance to cryolite erosion, oxidation resistance and erosion resistance. When used, it can form a thicker and more stable protective furnace wall on the working surface. Thereby effectively extending the service life of the electrolytic cell. Si3N4 combined with SiC materials have obvious advantages over ordinary carbon blocks. According to statistics, the annual demand for Si3N4 combined with SiC products for aluminum electrolytic cells at home and abroad is about 25,000 to 30,000 tons. SizN4 combined with SiC products for aluminum electrolytic cells have broad market prospects.