There are many types of garbage incinerators. Refractories for garbage incinerators are mainly divided into refractory bricks and castables. Refractory bricks are mainly clay refractory bricks, high alumina bricks, and silicon carbide bricks. The refractory castables are mainly clay-based, high-alumina plastics refractory and clay-based, or silicon carbide refractory castables. Next, let’s learn about the reasons for the damage of refractory materials used in the lower grate garbage incinerator. In order to avoid the problem of the refractory lining during the working process of the incinerator, it will be at a loss.
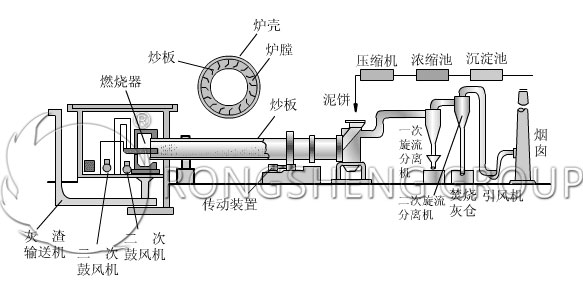
Working Characteristics of Grate Type Garbage Incinerators
When the incinerated garbage is a heterogeneous mixture of different compositions, its type, quantity, and calorific value are also very different. For this reason, the physical and chemical properties of refractory linings for waste incinerators should be adapted to the requirements of different stages of operation.
Because the temperature of the combustion chamber of the incinerator is as high as 1000°C, the input of waste must cause temperature changes. Therefore, refractory materials are required not only to be resistant to wear, corrosion, and adhesion, but also to be resistant to alkali and oxidation. The lower sidewall of the grate is also affected by rubbish wear and slag adhesion.
Complicated working environment, such as gas erosion, rubbish abrasion, and impact on the inside of the furnace body during high-temperature movement, etc. Therefore, the damage to the furnace wall of the grate type waste incinerator is concentrated on the refractory materials in the front and rear arch areas and the refractory bricks on the sidewalls of the second and third sections of the grate. Especially, the furnace wall with an air-cooled structure is prone to bulge and “bulge” phenomenon, and even collapse in severe cases.
These require high-quality refractory linings, and the demand will continue to increase. The use of silicon carbide castables and phosphates combined with high-alumina castables is gradually increasing. Because these two castables have good wear resistance.
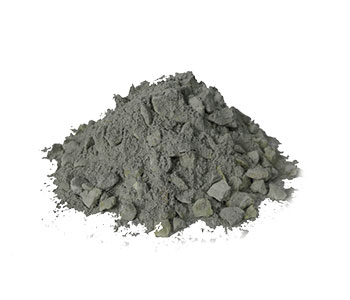
Refractory Corrosion and Ash Formation in the Front and Rear Arch Areas
The front and rear arch areas are directly exposed to high-temperature flue gas and fly ash due to the high temperature, resulting in serious erosion and damage of refractory materials. The ash adheres severely and even falls off. According to the results of the residual lining analysis, it can be seen that the ash and the bulk material react significantly. The formation and erosion of a large amount of low-melting material is the main reason that the steel plate in the back arch area burns red and the furnace is forced to stop.
Refractory materials for the back arch of the incinerator combustion chamber
At present, most of the refractory lining materials used in the front and rear arch areas have the characteristics of fire resistance, wear resistance, good thermal shock resistance, and strong erosion resistance. For example, corundum mullite or mullite-based oxide materials. In the atmosphere of the incinerator, the oxide material easily reacts with garbage fly ash, etc., and corrodes and penetrates, resulting in ash adhesion. Therefore, the incinerator needs to be shut down for dust removal during the operation of the incinerator lining. Compared with oxide materials, non-oxide materials such as silicon carbide not only have the characteristics of good fire resistance, high hardness, and good thermal shock resistance. Moreover, the silicon carbide material is not easy to wet and has good corrosion resistance. Therefore, it has good resistance to ash erosion and adhesion, which largely solves the problem of garbage fly ash adhesion.
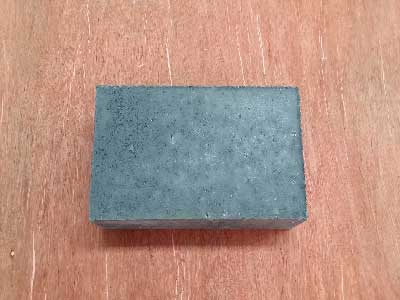
Air-cooled furnace wall “bulge”
The Higgs grate or Martin grate adopts air-cooled furnace walls at the sidewalls of the second, third, and fourth sections of the grate. Generally, there is a 60mm air interlayer, and the working layer refractory bricks are 114mm (Higgs) and 176mm (Cavanta) refractory bricks. In the use process of this kind of structure furnace wall, the thermal stress caused by the fluctuation of the temperature difference in the furnace caused by the fluctuation of the humidity or the heating value of the garbage. And under the dual effect of structural stress caused by repeated shutdown and start-up operations, it is easy to cause the furnace wall in the high-temperature section to “bulge” due to stress concentration. In severe cases, it will fall off or collapse.
Selection of Refractory Materials for Grate Type Garbage Incinerators
The front and rear arches are severely eroded, infiltrated, and scoured by smoke and garbage ash due to the high temperature. The use of silicon carbide-containing materials can greatly improve the corrosion resistance and penetration of ash and slag and the adhesion resistance of ash and slag. In addition, the design of adding anchor bricks can be adopted to improve the tensile strength of the unit structure, which can alleviate the “bulging” problem of the furnace wall to a certain extent. In addition, improve the strength of the hook bricks, the quality of the metal parts of the hook bricks, and the installation quality, and the level of furnace wall masonry. The structural stability of the sidewall is also greatly improved.
Learn more about the use of Rongsheng refractory materials for waste incinerators and the repair methods of refractory linings. For the Rongsheng Refractory bricks for sale, Please contact us, we will provide you with services according to your specific needs.