Many types of heat treatment furnaces are often used. The heat treatment furnace has low operating temperatures and good operating conditions. Generally use heat insulation refractory bricks or clay refractory bricks for the lining masonry. High alumina refractory bricks, cordierite bricks, silicon carbide bricks, and corundum bricks are used in individual parts. High temperature refractory castable for heat treatment furnace lining can also be used.
The heat treatment furnace is composed of three parts: furnace wall, furnace top, and furnace bottom. Materials such as refractory bricks, refractory castables, and refractory fiber cotton are commonly used as furnace linings. Due to the different furnace types, refractory materials, and heat treatment conditions, their service life is also different.
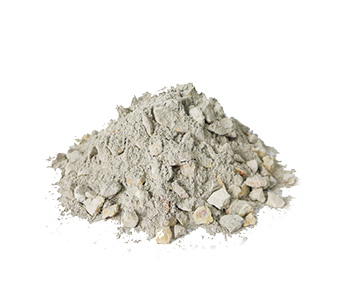
Refractory Castable for Heat Treatment Furnace Body
In the heat treatment furnace, the lining body of the heat treatment furnace working layer is cast with castable refractory, or with its prefabricated blocks. The furnace bodies of chamber furnaces and car bottom furnaces are hung with refractory castable prefabricated blocks. Not only does the construction speed is fast, but the furnace body has less heat dissipation, and the service life reaches 3 years. When the anchor bricks and hanging bricks are used, and clay refractory castables or high-strength lightweight refractory castables are used for on-site pouring, the furnace body has good integrity, low heat dissipation, and good thermal shock resistance. Therefore, its service life is generally 2 years.
High-performance Silica-alumina Refractory Castable
Generally, SiO2-Al2O3 raw materials with Al2O3 content greater than 68% can be used to configure high-performance silica-alumina refractory castables. By reasonably selecting the particle gradation and combining the system (including the variety and amount of binder, active filler, and additives), high-performance silica-alumina refractory castables can be formulated.
To make high-performance silica-alumina (SiO2-Al2O3) refractory castables, it is necessary to select good sintered SiO2-Al2O3 raw materials as refractory aggregates (multi-stage particles in proportion) and powder. Sometimes, in order to improve the performance of the material matrix, it is also necessary to mix a certain amount of high-grade raw materials such as alumina powder, white corundum powder or brown corundum powder into the mixture.
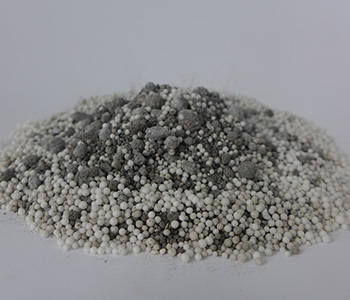
Drying and Dehydration Process of Refractory Castable
There are basically two construction methods for refractory castables: direct casting on-site, and prefabrication. There are three situations for direct casting on-site: integral casting, partial casting, and partial casting and repair.
Refractory castables are non-burning refractory materials. After the pouring construction is completed, if the drying and dehydration are not done properly, the castable will burst, which will seriously affect the service life of the refractory castable.
When the refractory castable is at a lower temperature, the binder will disperse, lose strength, and release water vapor. The dehydration of castables is divided into three stages:
- The first stage is between 30-100°C. At this time, free water is separated, and the dehydration speed is the fastest when the temperature and heat transfer process is 50-60℃.
- The second stage is when the temperature range is 100-170°C. The multi-body shrinks inside the castable, which slows down the discharge of steam. At this time, a small part of the hydrate also began to dehydration.
- The third stage is between 2000-400°C. This temperature is mainly the dehydration of hydrates. However, the dehydration of crystal water does not end until about 550°C. Many construction instructions require that the castable be baked, and the temperature will not rise when it is baked to 600°C. Because the crystal water has been discharged, the castable will no longer appear swelling and cracking of the green body.
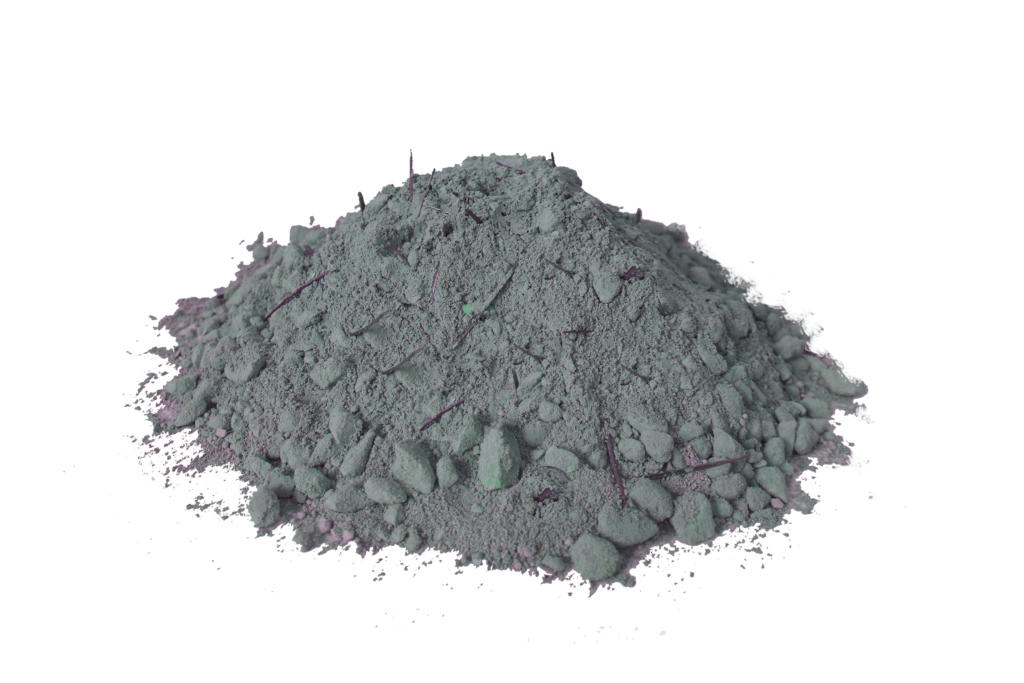
Matters Needing Attention in the Dewatering Process of Castables
During the dehydration process of refractory castable, the strength of the castable will decrease, and the structure will also relax at this time. When the steam is discharged, it will cause a lot of pressure on the cast material body. The easy burst of the castable during the drying process is caused by pressure. Therefore, some castable manufacturers will add anti-explosive agents to the castable, so that during the drying and dehydration process of the castable, micro-pores are formed at the low-temperature dehydration temperature, and stream water is discharged through the pores.
Adding metal powder to the refractory castable will make the castable form capillary vents, which is beneficial to the discharge of gas during dehydration. For example, steel fiber castable, steel fiber can improve the air permeability of the castable body, and will also form connected pores during the dehydration process, which is beneficial to the discharge of water vapor. Of course, the amount of steel fiber should be appropriate, and the amount should be appropriate under the condition of ensuring air permeability. Because the amount of steel fiber is too large, the porosity will increase, and the strength and corrosion resistance of the castable will be destroyed.
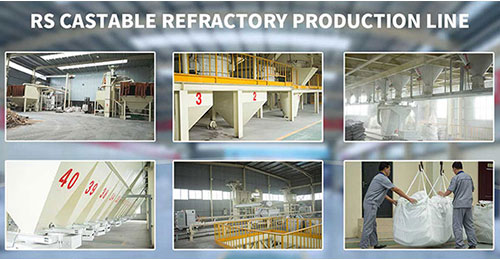
Rongsheng Refractory Manufacturer
Rongsheng is an experienced manufacturer and seller of refractory materials. Rongsheng’s refractories have been trusted by customers in more than 60 countries all over the world. For example, India, Pakistan, Kuwait, South Africa, Malaysia, Vietnam, Netherlands, Philippines, Singapore, Egypt, Russia, etc. Rongsheng’s automatic refractory castable production line has an annual output of 80,000 tons. If you want to know more about Rongsheng refractory manufacturer, or you want to obtain information and prices of high temperature refractory castables for heat treatment furnaces. Please contact us. Or send us an email, we will provide you with services according to your specific needs.