Overview of flat-top tunnel kiln. A pulverized coal brick kiln is a tunnel kiln that heats and burns wet bricks made of coal gangue or shale as the main raw materials to form finished bricks. The length of a pulverized coal brick kiln is generally more than 140 meters, and its width can be divided into several specifications such as 3.3 meters, 3.6 meters, 4.6 meters, and 6.9 meters according to the size of the brick kiln.
Working Temperature and Insulation Structure of the Firing Section
- Long-term working temperature is 950℃, and the theoretical working temperature is 1000℃~1050℃.
- 1200℃ high-temperature firing section, calculated according to the worst theoretical working conditions. According to the working temperature in the furnace, the thickness of the hot surface ceramic fiber module, and the total insulation thickness, calculate how low the temperature of the outer wall of the furnace is. The normal working temperature of the high-temperature section is ≤1050℃. The use of high-aluminum ceramic fiber modules with a long-term working temperature of 1200℃ can meet the working requirements of the converter. The backing blanket has a greater temperature drop due to its distance from the hot surface. Therefore, ordinary ceramic fibers with a long-term working temperature of 950°C can meet the requirements.
- Low temperature section below 650°C: Ordinary ceramic fibers with a long-term working temperature of 950°C can meet the requirements.
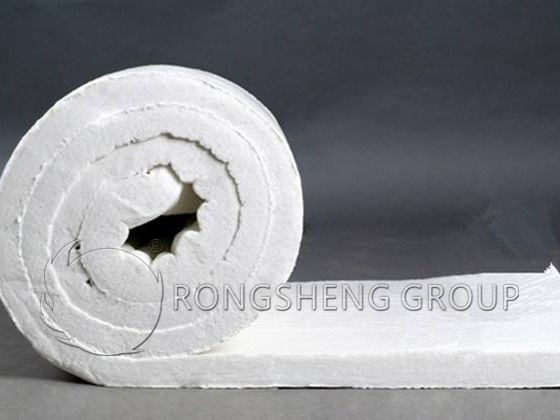
Advantages of Using Ceramic Fiber Insulation Materials as Furnace Lining
- Low volume density: Ceramic fiber furnace lining is more than 75% lighter than lightweight insulation brick furnace lining, and 90% to 95% lighter than lightweight castable furnace lining. If fiber furnace lining is used, the steel structure load of the kiln can be greatly reduced and the service life of the furnace can be extended.
- Low heat capacity (heat storage): The heat capacity of ceramic fiber is only about 1/10 of that of lightweight heat-resistant lining and lightweight castable lining, and the heat capacity of the furnace lining material is proportional to the weight of the furnace lining.
- Low thermal conductivity: The thermal conductivity of ceramic fiber furnace lining is 1/10 of that of lightweight heat-resistant lining, and the thermal insulation effect is significant.
- Simple construction: No expansion joints are required during the construction process, and construction personnel can take up their posts after basic training.
- Excellent resistance to thermal shock and mechanical vibration. The fiber blanket and module are flexible and elastic, and the fiber folding module furnace lining can be heated or cooled at any speed and is not easy to break.
- No need to bake the furnace: The furnace lining can be put into use after the construction is completed, and no baking procedure is required.
- Good sound insulation performance: Ceramic fiber can reduce high-frequency noise with a frequency less than 1000 Hz. For sound waves less than 300HZ, the sound insulation ability is better than that of commonly used sound insulation materials, which can significantly reduce noise pollution.
- Stable chemical properties: Ceramic aluminum silicate fiber is a neutral and slightly acidic material. In addition to reacting with strong acids and alkalis, it is not corroded by other weak acids, alkalis, water, oil, and steam, and is not wetted by lead, aluminum, and copper.
New Insulation Materials for Tunnel Kilns
Modern industrial tunnel kilns mainly include flat-top tunnel kilns, three-center arched tunnel kilns and semicircular arched tunnel kilns. In the early years, tunnel kilns were mostly built with refractory bricks and thermal insulation layers. With the promotion and application of ceramic fiber modules, their thermal performance is gradually improving.
Kiln roof insulation structure
Aluminum silicate ceramic fiber module is made of ceramic fiber needle-punched blanket of corresponding material, processed on special machinery according to the structure and size of fiber components. During the processing, a certain proportion of compression is maintained to ensure that after the wall lining of the ceramic fiber module is completed, the ceramic fiber module expands in different directions, so that the ceramic fiber modules are squeezed into a seamless whole. Ceramic fiber modules can be directly fixed on the anchor nails of the steel plate of the industrial kiln shell through various forms of anchors.
Advantages of lightweight aluminum silicate ceramic fiber flat ceiling insulation structure
The density of ceramic fiber module is only 200-260kg/m3, and the volume density is only 1/10 of refractory bricks. Ceramic fiber replaces traditional refractory products such as refractory bricks and castables in the steel metallurgy and petrochemical industries, and has made outstanding contributions to the energy saving and lightweight of industrial kilns.
Ceramic fiber has the advantages of light weight, high temperature resistance, good thermal stability, low thermal conductivity, small specific heat capacity and resistance to mechanical vibration. Therefore, it has been applied in machinery, metallurgy, chemical industry, petroleum, ceramics, glass and other industries.
The ceramic fiber suspended flat roof structure is used in the tunnel kiln roof, which successfully solves the problem of heavy weight and easy falling off and roof collapse of traditional heavy refractory materials. It realizes the lightweight structure of large-section tunnel kiln roof and mobile tunnel kiln, reduces costs, has a safe and reliable structure, and has a very good energy-saving effect. The most widely used ceramic fiber ceiling module is the flat-laid composite structure, which has good air tightness, good insulation effect and a firm structure.