Phosphate refractory castables are made of phosphoric acid or aluminum phosphate as a binder, high alumina or corundum as raw materials, and additives. They are prepared in proportion, cast, cured, and baked. Rongsheng Refractory Material Factory is a powerful manufacturer and seller of refractory materials. Rongsheng Refractory Material Factory’s phosphate castables are widely used. To purchase high-quality refractory lining materials, wear-resistant lining materials, and phosphate castables, don’t hesitate to get in touch with Rongsheng for free samples and quotes.
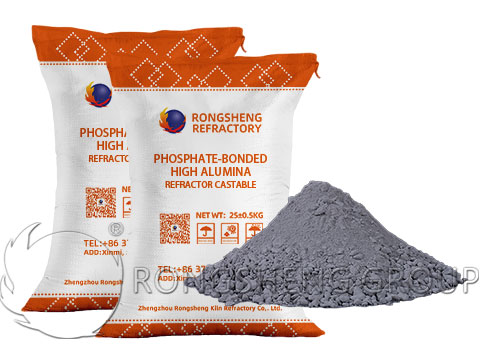
Application of Phosphate Refractory Castables
- It can be used in industrial equipment such as heating furnaces, soaking furnaces, coke ovens, and cement kilns.
- It can also be used to repair some parts in metallurgical furnaces and other containers.
- For parts with high wear resistance, it is more appropriate to use phosphate-refractory castables.
In summary, the binder of phosphate-bonded refractory castables, phosphate binders often use aluminum dihydrogen phosphate, sodium phosphate, and orthophosphate. The aggregates used in phosphate-bonded refractory castables are high aluminum, clay, silicon, and magnesium. A hardener can be used to take into account the room-temperature hardening performance of the castable. Active aluminum hydroxide, talc, ammonium fluoride, magnesium oxide, alkaline aluminum chloride, pure calcium aluminate cement, etc. can all be used as hardeners. However, the good hardening effect of magnesium oxide will affect the hot strength, and the hardening time varies greatly with the temperature.
Several High-Aluminum Phosphate Castables for Sale
Phosphoric acid hardly reacts with acidic oxides at room temperature, nor does it harden. Therefore, it is not suitable as a binder for acidic refractories. Phosphoric acid reacts with amphoteric oxides (such as Al2O3) at room temperature to form a hard solid, and the reaction rate between them can be controlled. Therefore, it is particularly suitable as a binder for high-aluminum refractories. Rongsheng Refractory Material Manufacturer has the following high-aluminum phosphate castables for sale.
- Phosphoric acid combined with high-aluminum refractory castables
- Rapid heating wear-resistant castables for circulating fluidized bed boilers
- Corundum-mullite wear-resistant refractory castables
- High-strength aluminum phosphate combined with corundum castables
Phosphate-bonded high-aluminum refractories have the following characteristics. Not affected by temperature, especially in winter, it sets quickly and is easy to demold without cracks. There is no low-strength zone in the hot state, especially at medium and low temperatures. High refractoriness. Excellent slag resistance. Good burst resistance and thermal shock resistance.
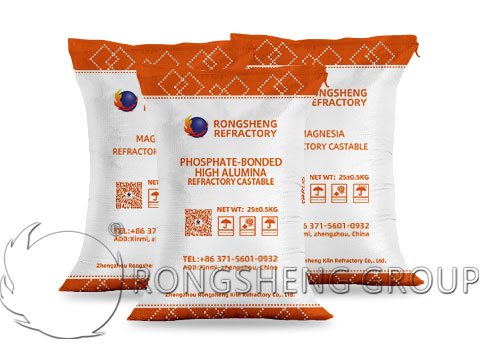
Rongsheng Phosphate-bonded Castables Manufacturer
Phosphate castables are refractory castables made of phosphoric acid or phosphate as a binder, refractory aggregate, powder and admixture. There are many types of phosphates. Industrial phosphoric acid, aluminum dihydrogen phosphate, magnesium dihydrogen phosphate, sodium tripolyphosphate and sodium hexametaphosphate are commonly used as binders in refractory materials.
There are many refractory materials used as phosphate-bonded refractory castables. Commonly used ones are: alumina clinker, clay clinker, siliceous raw materials, magnesia raw materials, corundum, mullite, zircon, alumina, chromium slag and silicon carbide. Light aggregates include expanded perlite, fly ash floating beads, alumina hollow balls, etc. Commonly used phosphate binders are aluminum dihydrogen phosphate, sodium polyphosphate and orthophosphate. Aggregates are divided into high alumina, clay, siliceous and magnesia.
The composition of phosphoric acid and phosphate-bonded refractory castables is similar to that of general refractory castables. Aluminum phosphate and phosphoric acid react only slowly with neutral and acidic aggregates at room temperature. In order to give the castable room temperature hardening properties, a hardener must be used. Hardeners include active aluminum hydroxide, talc, ammonium fluoride, magnesium oxide, alkaline aluminum chloride, pure calcium aluminate cement, etc. Calcium aluminate cement is a commonly used hardener.
Phosphoric acid and aluminum dihydrogen phosphate are used as binders for high-aluminum, clay, siliceous, silicon carbide and other castables. Generally, refractory aggregates are 60%-70%, and powders are 30%-40%. The amount of phosphoric acid and aluminum dihydrogen phosphate added with a concentration of 40%-60% is 11%-14%, and the amount of cement accelerator added is 2%-3%.
Preparation method of phosphoric acid and aluminum dihydrogen phosphate combined refractory castables
First, accurately weigh various raw materials according to the mix ratio, mix the aggregate and powder, and then add about 3/5 of the liquid used for the binder to stir. After stirring evenly, the material is trapped. During the second stirring, add cement accelerator according to the proportion, mix evenly, add the remaining binder, and stir for about two minutes. The mixed material can be poured and used. The mold is removed one day after casting and cured in the air for three days. This is the particularity of mixing construction of phosphoric acid and aluminum dihydrogen phosphate as castable binders, which is different from other binders.
The composition materials of phosphoric acid and phosphate refractory castables are mainly determined by the reaction rate of the binder with the main oxides in the refractory aggregate and powder. In particular, the selection of refractory powder is very important. Because its surface area and activity are larger than aggregates, it is easy to react with the binder. Only when the reaction rate is appropriate can the hardening process of phosphoric acid and phosphate refractory castables be completed, so as to obtain the performance. Generally speaking, for aggregates and powders composed of alkaline oxides, weakly acidic magnesium phosphate and sodium hexametaphosphate are used as binders, which has a better effect. For acidic or neutral aggregates and powders, phosphoric acid or aluminum dihydrogen phosphate and magnesium phosphate can be used as binders, but because the reaction rate is slow, accelerators and other measures can be added.
The main admixtures are accelerators, retarders and mineralizers. Because some phosphoric acid and phosphate refractory castables do not harden or harden very slowly at room temperature, they need to be heated and baked before use. For the convenience of construction and use, accelerators need to be added to make them harden at room temperature and obtain sufficient strength. If the hardening is too fast, retarders need to be added to control it.