At present, the structural forms of blast furnace bottoms and furnaces at home and abroad can be summarized into three categories: large carbon brick structure, small carbon brick structure, and ceramic cup structure. Blast furnace ceramic cup structure.
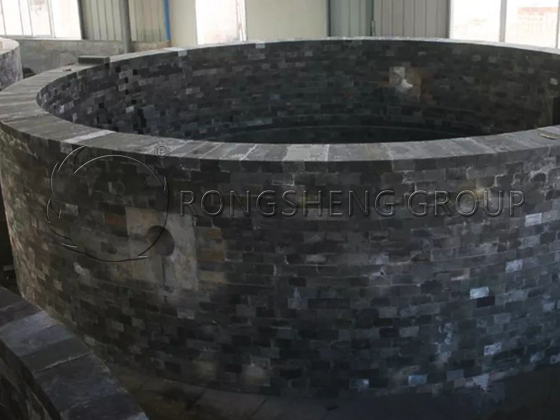
Characteristics of Blast Furnace Ceramic Cup Technology
(1) Prevent the penetration of molten iron. The 1150℃ isotherm is blocked in the ceramic layer. In addition, the special design structure of the ceramic cup and the thermal expansion of the material make the brick joints shrink, minimizing the penetration and erosion of molten iron on carbon bricks.
(2) Reduce the flow erosion of molten iron. The use of ceramic cups must have a reasonable dead iron layer depth, generally 20% of the furnace diameter. After the dead iron layer is deepened, the flow direction of molten iron in the furnace changes, thereby reducing the mechanical erosion of molten iron on the furnace bottom and furnace wall.
(3) Improve the thermal shock resistance of the furnace. The use of ceramic cups can increase the temperature of molten iron by 18~25T, reduce the energy consumption of the process, and create favorable conditions for steelmaking production.
(4) Easy to operate the blast furnace. Due to the increase in the heat storage of the furnace, it provides good conditions for stabilizing blast furnace production, activating the furnace, and re-blowing operation.
Since the thermal conductivity of ceramic cup bricks is relatively low, they can keep the molten iron in the furnace hearth warm, thus increasing the temperature of the molten iron and reducing energy consumption. Sufficient heat in the furnace hearth is beneficial to the operation of the blast furnace and improves the quality of the molten iron. Therefore, the ceramic cup furnace bottom and furnace hearth structure has developed rapidly.
The ceramic cup structure used in many large blast furnaces in China has a good effect, and the life of the furnace bottom and furnace hearth has been greatly improved. Under high smelting intensity conditions, the furnace bottom and furnace hearth can ensure safe production. Domestic ceramic cup bricks such as plastic composite corundum bricks, microporous corundum bricks, corundum-mullite bricks, corundum-silicon carbide bricks, etc., are widely used in large and medium-sized blast furnaces.
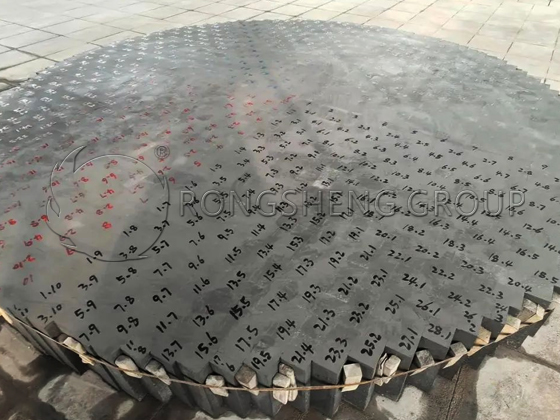
Performance Requirements of Refractory Materials for Blast Furnace Ceramic Cups
The essential function of ceramic cups is to isolate molten iron and protect carbon bricks from being dissolved by liquid molten iron. As long as the ceramic cups are stably present on the inner surface of the carbon brick lining, the ceramic cups obviously also play a role in heat insulation and can reduce the temperature of the carbon brick surface. Not only can it save energy and reduce consumption, but it can also improve the temperature distribution in the carbon brick layer.
Therefore, the refractory materials used for ceramic cups are required to have the following properties:
1. Good resistance to molten iron corrosion and good resistance to slag corrosion on the upper part of the cup wall.
2. Good resistance to molten iron and slag erosion.
3. Under high temperature conditions, the residual line becomes zero or slightly positive; good resistance to CO corrosion; good resistance to alkali corrosion.
4. Good adaptability to stress caused by thermal expansion under pressure; good resistance to thermal shock.
The new composite brown corundum bricks are made of brown corundum and SiC as the main raw materials, with an appropriate amount of metal subdivision added, high-pressure molding, and sintering in a reducing atmosphere. In addition to its strong resistance to molten iron and alkali corrosion, and resistance to molten iron erosion, the product also has the characteristics of self-repair, which prolongs its service life. It is a new generation of high-efficiency and long-life materials for large and medium-sized blast furnaces. In addition to being used for blast furnace ceramic cups, this product is also used for blast furnace hot tuyeres.
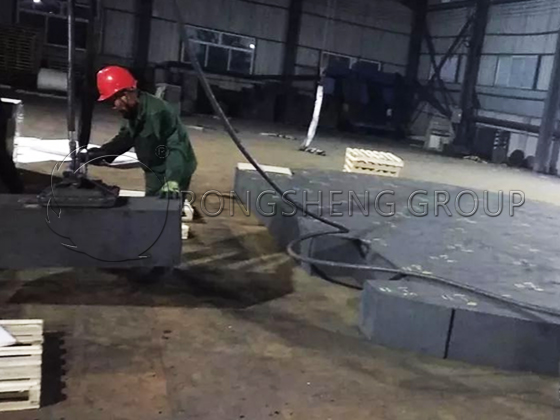
Importance of Pre-Laying of Ceramic Cup Bottom Bricks
Ceramic cups currently used in China for blast furnaces are basically based on the furnace lining technology introduced from the French SAVOIE company. Before the construction of ceramic cups, there is a very important process – pre-laying.
Pre-laying can solve the problems encountered during formal construction in advance. Because the bottom of the cup is solid, the cup wall has a certain thickness. The bottom of the cup is generally pre-laid in four pieces separated by the center of the cross. It can be pre-laid in four colors according to the center line of the cross. The pre-laid diameter is based on the diameter of the furnace to be built, and the total error of the masonry diameter is ±15. In actual construction, the four areas are constructed at the same time according to the odd and even numbers of the marked different colors. The error size is adjusted with brick fire mud during actual construction. To achieve flat masonry.
For the pre-laying of the bottom of the ceramic cup, the composite corundum silicon carbide bricks used must be polished on 6 sides in advance, and the elevation of each diameter must be pre-laid according to the drawing size after polishing. After pre-laying, the surface must be water-polished and smoothed again. Then the partitions are numbered, and the numbers are divided into single numbers and double numbers.
After the single and double numbers are assigned to the four areas, they are unpacked and packed in order, and then the boxes are marked with the order of use. Generally, the numbers of different areas will be sent with the masonry numbering diagram when shipped. And each area will be separated and numbered with a construction drawing. This ensures that the masonry is successfully built according to the pre-built numbers at the construction site.
Therefore, the pre-built ceramic pad is very important. The key is to grind it into the size used in the blast furnace hearth. In order to solve the problem of smooth construction, it also ensures the precision of the ceramic cup and keeps it consistent with the surrounding carbon brick plane.