Circulating fluidized bed boilers have the advantages of high thermal efficiency, low pollution emissions, and wide adaptability to coal types. They are used in most thermal power plants and heating projects. The lining of the circulating fluidized bed boiler has to withstand strong dust erosion for a long time at 800℃~1100℃, so it puts forward higher requirements on the wear resistance of the castable in the part. The wear amount is generally required to be less than 7~9cm3, and some strict requirements must be less than 5cm3. Therefore, high-strength wear-resistant castables came into being.
Commonly used high-strength wear-resistant castables are made of special sintered alumina clinker and brown corundum as the main raw materials. The maximum particle size is 5mm, and high-alumina cement SiO2 micropowder and Al2O3 micropowder are used as binders, and an appropriate amount of high-efficiency dispersant is used. When used, add about 5.5% of water and vibrate to cast. At 20℃, the performance of the sample dried and hardened for 6h can meet the general wear resistance requirements. However for higher requirements, effective improvement measures need to be found.
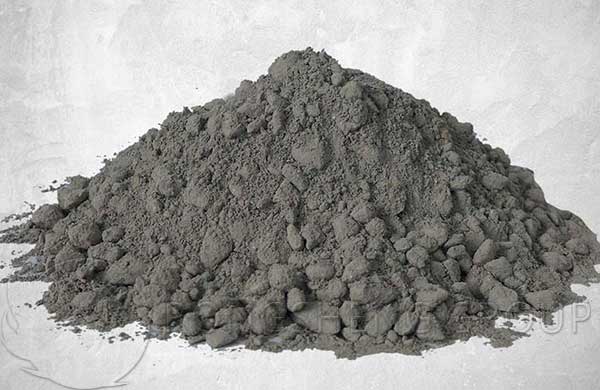
Measures that can be taken to improve the anti-wear performance of high-strength wear-resistant castables:
(1) Increase the maximum particle size and increase the proportion of large particles added.
(2) Reasonably introduce anti-wear agents.
Wear Resistance of High Wear-Resistant Refractory Castables
The parts of the kiln lining that are impacted by heating and cooling require castables with good wear resistance and thermal shock stability. At Rongsheng Refractory Material Factory, castables with good wear resistance include fused corundum, white corundum, and silicon carbide.
Due to the different costs and usage locations during use, companies generally choose different castables according to different lining locations. The castable with good wear resistance and moderate price is silicon carbide castable, also called high wear-resistant castable.
The prices of fused corundum and white corundum castables are relatively high. For the use of furnace linings with medium temperature corrosion, cheaper high wear-resistant materials can be used. High wear-resistant castables are made of special high-alumina bauxite clinker, with a certain proportion of silicon carbide as raw materials, to make low-cement castables, so as to improve the medium-temperature strength performance of the castable. High wear-resistant castables have the properties of wear resistance and thermal shock resistance, and the cost is relatively low.
The binder in high wear-resistant materials is very important. Generally, wear-resistant materials are prepared with white cement. The castables prepared in this way have good fluidity, high strength and good wear resistance. The binder affects the wear resistance of the castable.
During the construction of high wear resistance, too much water should not be added. If too much water is added, the water will evaporate after baking and heating, leaving more gaps and worsening the wear resistance. When the amount of water is moderate, the castable will not have a transformation reaction during the drying process, and the wear resistance will also increase.
When the castable is used in an environment where the actual temperature is reached, the oxidation resistance and wear resistance will be effectively improved. The number of thermal shocks of the castable will also increase.
The wear resistance of high wear-resistant castables is good because a certain proportion of silicon carbide components are added. While silicon carbide improves wear resistance, strength also increases. Generally, high wear-resistant castables are selected in areas with strong erosion.
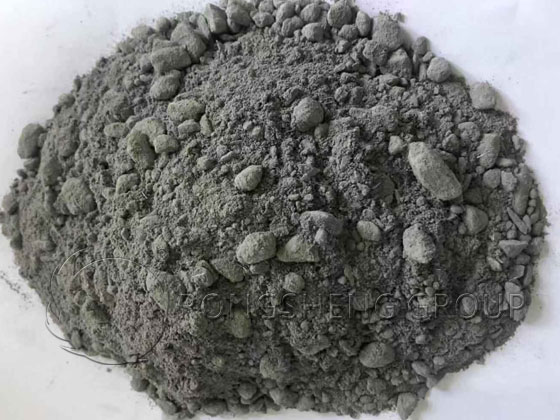
Performance of High-Strength Wear-Resistant Castables
High-strength wear-resistant castables are made of imported high-alumina cement, mineral admixtures, high-strength aggregates and anti-cracking and wear-resistant agents, using micro-powder technology and special process proportions, and are industrially produced and prepared.
High-strength wear-resistant castables are mixed with water and used to form a certain thickness of anti-wear layer on the surface of the silo or ore tank through artificial plastering. After reasonable maintenance, it can meet the technical requirements and has strong impact resistance, high compressive strength and good durability. In particular, it has strong anti-corrosion ability and high wear resistance.
The special performance of high-strength wear-resistant castables is that they have the effects of early strength and early setting. In summer, they can be initially set in 20-30 minutes and final set in 3 hours. In winter, they can be final set in 4-6 hours, and the compressive strength can reach 40MPa in just 1 day. The compressive strength after baking is 65MPa.
Construction method of high-strength wear-resistant castables. First weld the top of the plate and lay the steel mesh. Then stir the wear-resistant castable, add 13-15 liters of drinking water (PH value = 6-7) to 100 kg of dry material, and stir for 2-3 minutes. It is not acceptable to stir the castable for too short or too long. In particular, the amount of water added must be strictly controlled. When constructing in winter, the temperature of water added to the castable must reach 50℃. After the construction is completed, it needs to be cured for 2-3 days to achieve the initial setting effect.
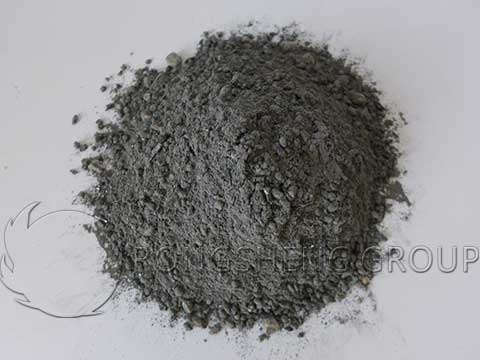
How to Improve the Performance of Ultra-High Strength Wear-Resistant Refractory Castables?
Ultra-high strength wear-resistant refractory castables use high-alumina clinker as aggregate, ultrafine powder (silicon powder) and aluminate cement in different proportions as binders, and high-efficiency admixture sodium tripolyphosphate (P3).
Methods for improving the performance of ultra-high strength wear-resistant refractory castables
(1) Under the conditions of a certain proportion and gradation of aggregates and the use of a 1% naphthalene-based water reducer in cement dosage, the best performance of the castable is considered. The optimal ratio of the castable is a cement dosage of 10%, silica fume dosage of 6%, dispersant dosage of 0.2%, and wollastonite fiber dosage of 5%.
(2) The amount of silica fume is the main favorable factor for compressive strength and flexural strength in the high-temperature stage. The amount of cement is the main favorable factor for strength in the low-temperature stage. Regarding the effect of linear shrinkage after the burning of refractory castables, dispersant P3 is the main favorable factor for strength in the high and low-temperature stages.
(3) The linear shrinkage rate of refractory castables after burning can be controlled by adding fibers. In order not to affect the flexural and compressive strength of the castable, the addition amount is preferably controlled to 5%.
(4) Dispersant P3 has a certain water-reducing effect and can also increase the density of the castable. However, it has a large water seepage property, and excessive addition will affect the strength and linear shrinkage of the castable after burning. The performance is best when the dosage is 0.2%.
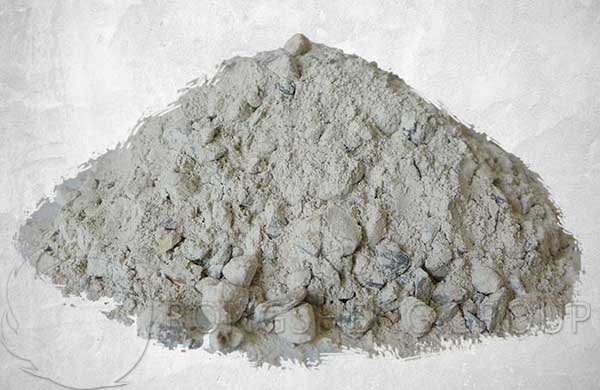
Application of High-Strength Wear-Resistant Castables
High-strength wear-resistant castables are used in the lining anti-wear layer of slag ditches, ore troughs, coal unloading troughs, lower hoppers, and material silos in metallurgy, coal, power plant, chemical, cement, and other industries. High-strength wear-resistant castables will protect the foundation concrete. Especially for power plant boilers, they are used more. Some pipeline linings with large flue gas erosion also need to use wear-resistant castables to resist the erosion of flue gas and high scouring.
To purchase high-quality high-strength wear-resistant refractory castables, please choose a powerful refractory manufacturer. Rongsheng Refractory Material Factory is a manufacturer and seller of refractory materials with rich production and sales experience. Our refractory products have been sold to more than 120 countries around the world, such as South Africa, Chile, Egypt, Colombia, Uzbekistan, Italy, Indonesia, Ukraine, Hungary, Spain, Kenya, Syria, Zambia, Oman, Venezuela, India, Peru, the United States, Ethiopia, etc. Moreover, our environmentally friendly fully automatic amorphous refractory production line provides a reliable guarantee for high-quality amorphous refractory linings. Moreover, our comprehensive customer service also provides a guarantee for long-term and high-life furnace linings. Contact us for free solutions and quotes.