In recent years, solid waste landfills have been gradually replaced by reduction incineration. The effect of garbage incineration is affected by factors such as garbage material, combustion temperature, and combustion location. Rongsheng refractory material manufacturer can provide high-quality and long-life refractory linings for waste incinerators. In order to improve the effect of waste incineration, the lining of the waste incinerator should have the following characteristics.
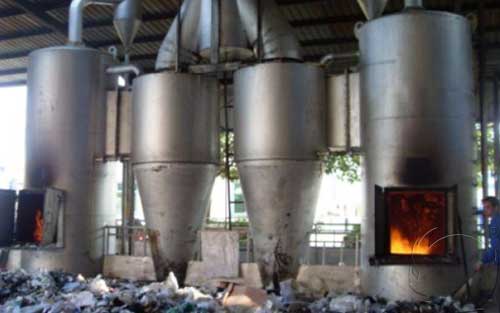
Characteristics of Long-life Waste Incinerator Refractory Linings
- High temperature resistance and thermal shock resistance.
Refractory furnace lining materials, as the name suggests, have high-temperature resistance as their basic performance. When the garbage incinerator is working, the maximum temperature exceeds 1000°C. Refractory materials need to not melt, soften, or undergo other changes in physical and chemical properties at high temperatures. Due to the complex composition of garbage, instantaneous temperature fluctuations may occur during combustion. At the same time, the refractory lining material is also required to have strong thermal shock resistance.
- Resistant to wear and impact.
The garbage contains a certain amount of moisture, the combustion chamber is affected by steam during combustion, and the furnace lining may peel off. The particulate smoke emitted when garbage is burned impacts the surface of the furnace lining, easily causing wear and tear on the furnace lining. The above problems will damage the integrity of the furnace lining and affect the thermal insulation effect of the refractory materials. In order to avoid such problems, it is recommended to choose castables with stronger wear resistance and impact resistance in key parts of the furnace lining.
- Resistant to corrosion and slag invasion.
Solid waste is highly polluting and toxic and has strong chemical erosion capabilities. The refractory material used in the furnace lining needs to have good resistance to slag erosion and corrosion, so as to prevent combustion smoke from eroding the surface of the refractory lining after contacting the refractory material. This causes the furnace lining to become thinner and affects the thermal insulation effect.
All of the above are the basic properties that the refractory materials for waste incinerator linings should possess. The actual thermal insulation effect of the furnace lining is also closely related to the design plan, material quality, and construction techniques. Rongshneg refractory material manufacturers can customize furnace lining designs based on the actual working conditions of customers’ high-temperature industrial furnaces. By using different refractory materials for the feeding port, combustion chamber, slag outlet, and other parts, and using reasonable construction methods, stronger fire-resistant and heat-insulating effects can be achieved. At the same time, the furnace lining is guaranteed to have a longer service life.
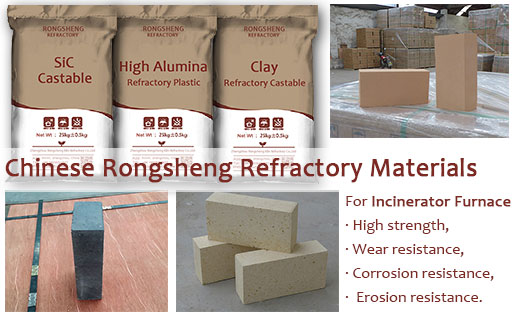
Selection of Configuration of Refractory Bricks and Castables for Waste Incinerator Combustion Chamber
The combustion chamber of the waste incinerator is a key equipment in the waste incineration process, and its performance directly affects the efficiency and environmental protection indicators of waste incineration. The main function of the combustion chamber is to fully burn garbage at high temperatures and convert organic matter into harmless gases and solid residues. In order to achieve this purpose, the combustion chamber needs to have good thermal insulation properties, wear resistance, and thermal shock resistance. Refractory bricks and castables are the main materials of the combustion chamber, and their configuration selection has an important impact on the performance of the combustion chamber.
Configuration selection of refractory bricks and castables
In actual projects, the lining of the combustion chamber of a waste incinerator is usually a combination of refractory bricks and castables. This combination can not only give full play to the respective advantages of refractory bricks and castables but also reduce construction costs. When selecting a configuration of refractory bricks and castables, the following aspects need to be considered.
(1) According to the working conditions and temperature distribution of the combustion chamber, reasonably divide the use areas of refractory bricks and castables. Generally speaking, refractory bricks should be used in areas with higher temperatures and greater wear and tear. Castables can be used in areas with lower temperatures and less wear.
(2) Select the appropriate thickness of refractory bricks and castables. The thickness of refractory bricks and castables directly affects the thermal insulation performance and service life of the combustion chamber. On the premise of meeting the thermal insulation performance requirements, thinner refractory bricks and castables should be selected as much as possible to reduce construction costs.
(3) Choose appropriate construction methods of refractory bricks and castables. The construction methods of refractory bricks and castables include dry laying, wet laying, pouring, etc. Different construction methods have different effects on the performance and service life of the combustion chamber. When selecting a construction method, the selection should be based on actual engineering conditions and construction requirements.
In short, the configuration selection of refractory bricks and castables used in the combustion chamber of a waste incinerator has an important impact on the performance and service life of the combustion chamber. When selecting refractory bricks and castables, factors such as the working conditions, temperature distribution, wear resistance, and thermal shock resistance of the combustion chamber should be fully considered. Reasonably configure the type, thickness, and construction method of refractory bricks and castables. To improve the performance and service life of the waste incinerator combustion chamber and reduce construction and operating costs.
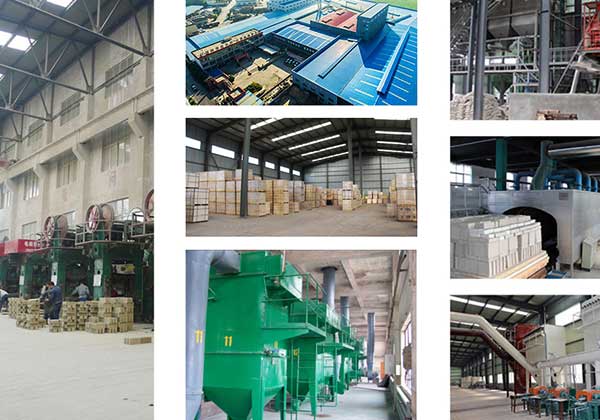
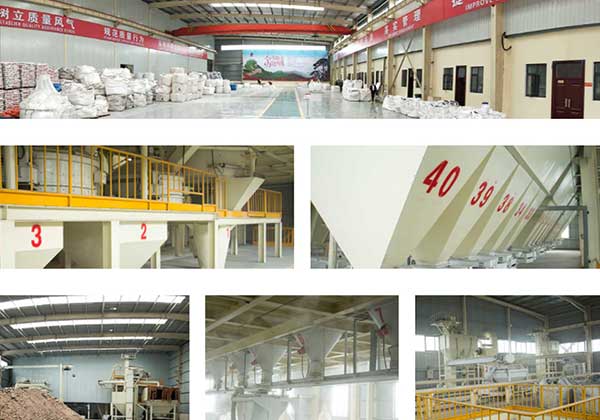
Refractory bricks and castables for the combustion chamber of waste incinerators
With the acceleration of urbanization, the problem of garbage disposal is becoming increasingly serious. As an effective treatment method, waste incineration has received widespread attention and application. However, the waste gas, wastewater, and other pollutants generated during the garbage incineration process have caused serious harm to the environment and human health. Therefore, how to improve the performance of the combustion chamber of waste incinerators and reduce pollutant emissions has become an important issue in the field of waste incineration treatment.
Refractory bricks and castables are the main materials in the combustion chamber of waste incinerators, and their configuration selection has an important impact on the performance of the combustion chamber. By rationally selecting the type, thickness, and construction method of refractory bricks and castables, the thermal insulation performance, wear resistance and thermal shock resistance of the combustion chamber can be improved, the service life of the combustion chamber can be extended, and the construction and operating costs can be reduced. At the same time, it can also reduce the emissions of waste gas, wastewater, and other pollutants produced during the garbage incineration process. Reduce impacts on the environment and human health.
In short, the configuration selection of refractory bricks and castables for the combustion chamber of a waste incinerator is a complex engineering issue that requires comprehensive consideration of multiple factors. By continuously optimizing the configuration of refractory bricks and castables, the performance of the combustion chamber of the waste incinerator is improved. It will help promote the development of waste incineration technology and provide strong support for solving urban waste disposal problems.