Alumina bubble brick has excellent high-temperature resistance and heat insulation performance, and it can be directly used as the working lining of high-temperature kilns. However, ordinary alumina hollow sphere bricks are spherical because the alumina hollow sphere aggregate particles are point-bonded between the particles, and cannot form a high-strength structure with interlaced networks and inlaid with each other, and the bonding force between the particles is extremely poor. In addition, the matrix phase of ordinary alumina bubble bricks is mainly corundum, which results in extremely poor thermal vibration stability of the product. It has greatly affected the use of alumina hollow ball bricks, and the life of the kiln using alumina bubble bricks is extremely low. For this reason, it is very important to improve the spalling resistance of alumina bubble bricks. So, what is a high-quality Anti-Stripping Alumina Bubble Brick? Refractory manufacturers have finally achieved this goal after many experiments and customer feedback.
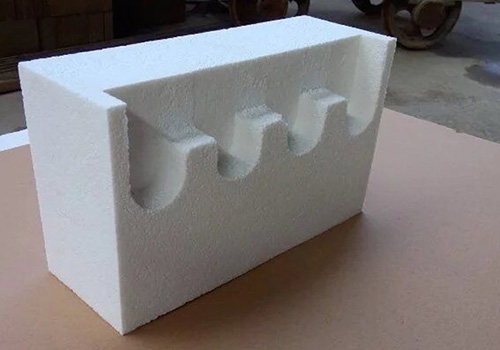
The Raw Material Composition of High-Quality Anti-Stripping Alumina Bubble Brick
The raw material composition of high-quality Anti-Stripping Alumina Bubble Bricks uses high-quality alumina hollow spheres, fused corundum powder, α-Al2O3 micro powder, SiO2 micro powder, sillimanite, and high-quality clay powder as raw materials.
The Production Process of High-Quality Anti-Stripping Alumina Bubble Brick
Substituting the mullite phase for the corundum phase of the matrix part can improve the spalling resistance of alumina hollow ball bricks. Therefore, α-Al2O3 micro powder, SiO2 micro powder, sillimanite powder, or high-quality clay powder are introduced into the matrix part.
Prepare according to the set ingredient plan, mix according to the mixing requirements, vibrate the mixture with a wooden mold, dry it naturally for 24 hours, and then dry it at 110°C for 24 hours. It is fired for 4h at a temperature of 1600°C.
Precautions
In the production of high-quality Anti-Stripping Alumina Bubble Bricks, the amount of SiO2 micro powder and sillimanite added must be strictly controlled. Refractory brick manufacturers have determined the amount of both of them through many experiments, ensuring the performance of alumina hollow ball bricks.
- The amount of SiO2 powder added
When the SiO2 powder is not added, the linear rate of change in the re-burning of the product is negative. With the increase of the amount of SiO2 powder added, the linear rate of re-burning became positive and showed an increasing trend. This shows that after adding SiO2 micro powder, a mullite phase is formed in the matrix part of the alumina hollow ball brick. The amount of mullite phase formation increases with the addition of SiO2 powder. However, such a large change in volume will cause adverse consequences during the use of the product, so the amount of SIO2 powder added should be moderate. The appropriate addition amount is 3%. At this time, the normal temperature compressive strength, high-temperature performance, and thermal shock resistance of the product are also relatively good.
- The amount of sillimanite added
The addition of sillimanite is very helpful to improve the high-temperature performance and thermal shock resistance of the product. However, if the added amount of sillimanite is too large, the re-burning linear change rate of the product is also large, which is not conducive to the use of the product, so the added amount of sillimanite should be controlled. The appropriate amount of sillimanite added is 10%.
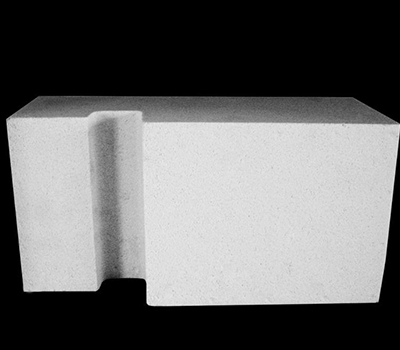
Advantages of High-Quality Anti-Stripping Alumina Bubble Brick
A certain amount of sillimanite, SiO2 micro powder and α-Al2O3 micro powder are introduced into the matrix of the alumina hollow ball brick. Through mullite petrochemical, the lack of point bonding strength between alumina hollow sphere particles is supplemented, the bonding strength is enhanced, and the product has better high-temperature resistance and peeling resistance. The product can be directly used as the lining of high-temperature furnaces for intermittent operation, which improves the insulation performance of the furnace, saves energy, and reduces consumption. It is a promising high-temperature material.
Application of High-Quality Anti-Stripping Alumina Bubble Brick
Add sillimanite powder, α-Al2O3 micro powder, and SiO2 micro powder to the matrix, use water as a binding agent and burn in an inverted flame kiln after molding. Anti-Stripping Alumina Bubble Bricks are used as working linings on the wall and roof of a roller shuttle kiln. Working temperature is 1500~1550℃. After more than two years of use, the brick does not peel off, does not deform, and has excellent high-temperature resistance. The use effect is significantly better than other similar products, which meets the user’s use requirements.
In addition, high-quality alumina hollow ball bricks are used on the kiln car of a 62 m high-temperature tunnel kiln in a ceramic factory. The kiln fires alumina ceramic balls at a firing temperature of 1500~1720°C. After nearly three years of use, it has been shown that the high-quality alumina bubble brick does not flake off and has high strength and good high-temperature performance, which meets the user’s requirements and improves the service life of the kiln car.
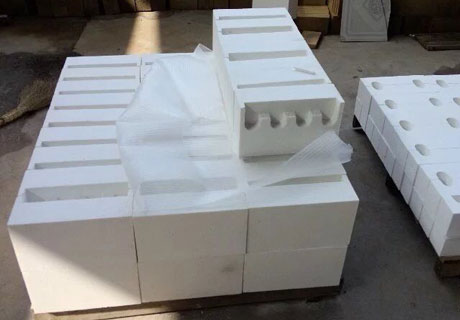
To buy high-quality Anti-Stripping Alumina Bubble Bricks, please choose a strong refractory brick manufacturer. Rongsheng refractory brick manufacturer has rich experience in the production and sales of refractory bricks. High-quality high-alumina bricks, alumina bubble bricks, and other refractory brick products have received many return orders from customers. Choose Rongsheng refractory brick manufacturer, you will have a full range of customer services, from free customization of the kiln lining scheme, to free sample mailing and after-sales service of the final product. Look forward to working with you.