Phosphate-bonded high alumina bricks (hereinafter referred to as phosphate bricks) are made of special-grade bauxite clinker as the main raw material, adding an appropriate amount of phosphoric acid aqueous solution. It is made through pre-mixing, material trapping, mixing, molding, drying, heat treatment, and other processes. Due to the high strength of phosphate bricks, good wear resistance, and good chemical resistance. And its alkali resistance is better than clay bricks and high alumina bricks, and it has good thermal shock resistance. Therefore, phosphate bricks are commonly used in the transition zone of rotary kilns, kiln mouths, kiln door covers, cooler linings, and other places where refractory bricks are easy to loosen and fall. This article mainly introduces the fire-free production process of phosphate bricks, Rongsheng Refractory, as one of the refractory manufacturers, focuses on the analysis of the bonding agent, drying, and heat treatment used in the production process.
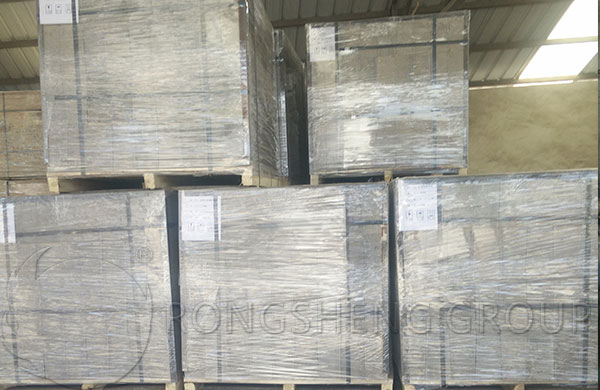
Binder in the Production Process of Phosphate Bricks
Phosphoric acid itself has no cohesiveness. When it reacts with neutral oxides and weak alkaline oxides of raw materials such as special grade clay clinker to form phosphate, it shows good cohesiveness. The bonding effect formed is mainly caused by the polymerization and adhesion of acid phosphate, in addition to the chemical reaction with the material to be bonded. Phosphate-based ions connect them in various ways to macromolecules with long-chain planar network or spatial framework structure. The oxygen in the phosphoric acid group PO4 plays a role in this connection, which causes the body to condense and harden. The acid phosphate formed depends on the degree of neutralization during the reaction, that is, the degree of substitution of hydrogen, mainly aluminum dihydrogen phosphate [Al (H2PO4) 3] aluminum hydrogen phosphate [Al2 (HPO4) 3 ].
It is generally believed that the main component is [Al (H2PO4) 3]. Since it is soluble in water at room temperature, it can still maintain plasticity for a long time after it is used to form a mixture. However, when heated to a certain temperature, the acid aluminum phosphate can be changed into aluminum pyrophosphate and aluminum metaphosphate, and polymerization reaction occurs subsequently.
Aluminum metaphosphate polymer [Al (PO3) 3] exists at temperatures above 400 ℃. Due to the formation and polymerization of this new compound and the formation of strong adhesion at the same time, the combination gains strength. As the temperature increases, aluminum metaphosphate can also decompose to form AlPO4 and P2O5. P2O5 and Al2O3 can also form AlPO4, which improves the strength of the combined body. Therefore, phosphate bricks can have the characteristics of high strength and good wear resistance.
Drying in the Production Process of Phosphate Bricks
Because the formed phosphate brick body contains 4% to 5% water. Therefore, the brick must be dried to improve its mechanical strength. This is also conducive to transportation, kiln loading operations, and ensuring the appearance quality of the products. According to regulations, drying is carried out in a tunnel dryer. The bricks must be dried naturally before entering the drying kiln, and the drying time shall not be less than 12h. The temperature of entering the kiln is 60-80 ℃, the temperature of exiting the kiln is 110-130 ℃, and the drying time is not less than 48h. After drying, the residual moisture content is ≤1%. The heat treatment is carried out in an inverted flame kiln that uses coal gas as fuel. When the bricks are installed in the kiln, they need to be handled with care, so that they are flat, stable, straight, loose, and the bricks are drawn seam, leaving a good fire path.
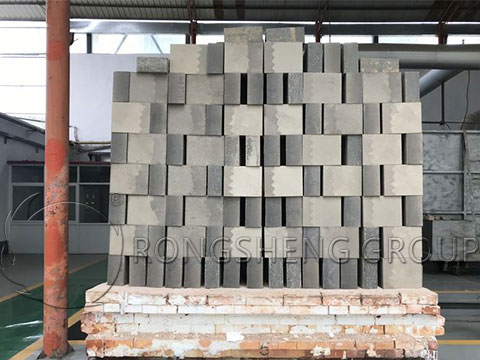
Heat Treatment in the Production Process of Phosphate Bricks
In the actual production process of phosphate bricks, the production of fired bricks is also carried out at the same time as the production of phosphate bricks. The original process parameters are difficult to control in actual production, resulting in dryness and poor turnover, which affects the normal production of the molding process. Moreover, the drying and heat treatment time of phosphate bricks is too long, which easily affects the delivery time. During the heat treatment process, improperly reserved kiln fire channel and high temperature can easily cause the bricks at the top of the kiln to be over-burned (red), and the bricks at the bottom are under-burned (black). These have greatly reduced the product qualification rate of phosphate high alumina bricks.
The heat treatment temperature of phosphate brick is 500~600℃. Therefore, the reasonable layout of the kiln, the width of the brick column, and the size of the brick gap should also be appropriate. The strength of phosphate bricks after heat treatment depends on the degree of polymerization and reaction of aluminum metaphosphate, and the required temperature is above 300 ℃. Therefore, when the temperature is less than 300 ℃, the temperature rise rate can be appropriately increased when the free water remaining in the brick and the atmospheric adsorbed water are eliminated, and the brick has no cracks.
The fire operation during the heat treatment of phosphate bricks has a greater impact on product quality. In addition to correct operation according to the temperature system, it is also necessary to ensure the pressure and atmosphere in the kiln. Therefore, it is necessary to reasonably adjust the gate and the ratio of gas and air to meet the needs. In the low-temperature stage (0~200 ℃), the main purpose is to remove the residual free water and atmospheric adsorbed water in the bricks. The gate should be opened to increase the suction of the chimney and take away the water as soon as possible. In the middle-temperature stage (200~500 ℃), it is mainly the formation of aluminum pyrophosphate and the polymerization reaction of aluminum metaphosphate. The shutter can be appropriately lowered to better control the kiln temperature and make the reaction proceed fully. During the heat preservation stage, the gate should be lowered to increase the temperature of the lower part of the kiln so that the temperature of the whole kiln is uniform.
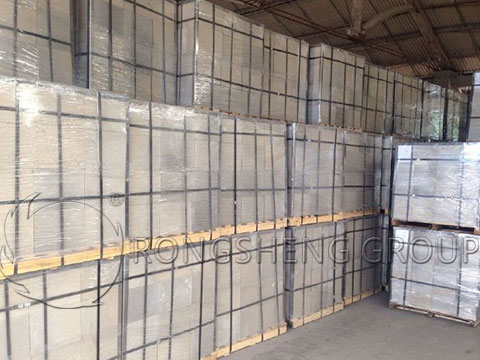
Phosphate Brick Manufacturer
A high-quality phosphate brick manufacturer with rich experience in the production and sales of refractory bricks. The sales of phosphate-bonded high alumina bricks and the refractory products of refractory manufacturers have been sold to more than 60 countries around the world. For example, Russia, South Africa, Kazakhstan, Philippines, Chile, Malaysia, Indonesia, Vietnam, Kuwait, Turkey, Zambia, Peru, Mexico, Qatar, Egypt, etc. In the production process of phosphate pricks and packaging of phosphate bricks, high-quality products certainly require high-quality product packaging. Of course, this is also determined by the types of refractory bricks and the product characteristics of phosphate bricks. Rongsheng refractory materials manufacturers have perfect customer service and high-quality refractory brick lining materials. Get a free quote now.