High-alumina ramming mass is a neutral refractory material. It is mainly made of high-alumina bauxite clinker as aggregate, mixed with high-purity corundum powder, improved matrix grade, and added with anti-seepage binder. It has the advantages of compensating for material shrinkage, enhancing spalling, improving density and corrosion resistance. Product advantages of high-alumina ramming mass. In areas with high operating temperature and severe chemical corrosion, high-alumina bauxite clinker with high Al2O3 content and good calcination is usually selected as aggregate. Sometimes, in order to make the ramming mass have a certain plasticity and improve the construction performance, so as to avoid overpressure stratification and high-temperature spalling, high-plasticity clay is added. Rongsheng Refractory Material Manufacturer can provide a baking-free high-alumina-silicon carbide-carbon ramming mass. Contact us for free quotes and samples.
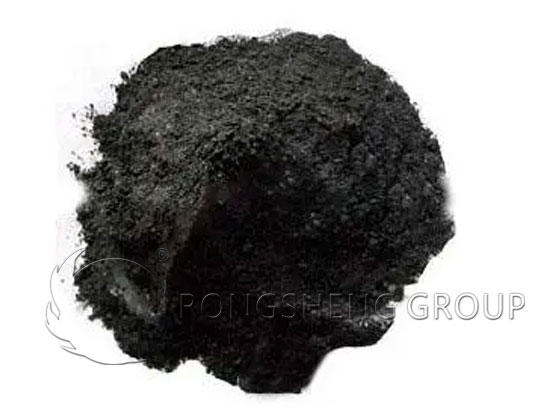
High Alumina-Silicon Carbide-Carbon Ramming Mass
The mixture composed of high-aluminum clinker, silicon carbide, carbon material, binder and admixture, which is constructed by ramming method, is called high-aluminum-silicon carbide-carbon ramming mass. This kind of ramming mass is mainly used as the lining of the iron ditch and slag ditch of medium and small blast furnaces. The main components of the iron ditch material are Al2O3 45%~69%; SiC+C is 10%~25%. The main components of the slag ditch material are Al2O3 35%~45%; SiC+C is 15%~30%.
The high-alumina clinker used to prepare this type of ramming material requires the impurity (Fe2O3, R2O) content to be as low as possible. The water absorption rate is less than 4.5%. Its particle size composition is 40% to 60% for coarse particles (8 ~ 2 mm), 10% to 20% for medium particles (2~0.074 mm), and 30% to 40% for fine particles (less than 0.074 mm). Silicon carbide uses black silicon carbide with a particle size of less than 100 mesh. Carbon materials can be metallurgical coke or graphite, which requires low impurity content and high fixed carbon content. In order to improve the operating performance and sintering performance of high-alumina-silicon carbide-carbon ramming material during use, soft clay or bentonite can also be added. Sintering aids at different temperatures can also be added according to different use temperatures.
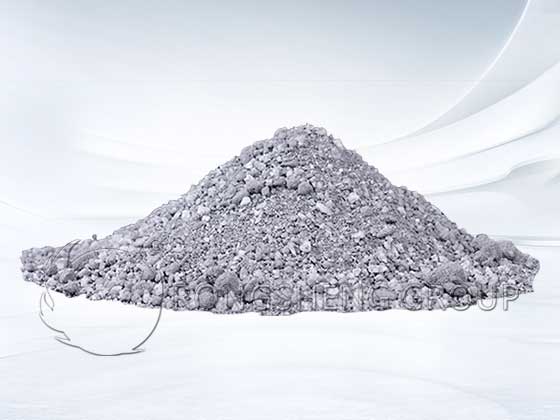
The binders used for this type of ramming material include asphalt, tar + asphalt, liquid phenolic resin, aluminum dihydrogen phosphate, etc. When asphalt is used as a binder, water needs to be added when preparing the ramming material, and it needs to be baked before use after ramming. When tar + asphalt is used as a binder, no water needs to be added when preparing the ramming material, and molten iron can be directly passed through without baking after ramming, which is a ramming material that does not require baking. However, the smoke is large during use, which will pollute the environment. When liquid phenolic resin is used as a binder, it is also not necessary to add water or bake, and it can be directly put into use, which is also a ramming material that does not require baking. It has light pollution to the environment, but the shelf life of the ramming material is short, and it needs to be prepared on site for direct use. When aluminum dihydrogen phosphate is used as a binder, it has poor resistance to corrosion by molten iron and slag. It can only be used as the lining of the iron ditch of a small blast furnace, and aluminum dihydrogen phosphate is basically no longer used as a binder.
Additives used to improve the performance of high-aluminum-silicon carbide-carbon ramming materials include antioxidants, plasticizers, impregnants, shrinkage inhibitors, etc. The purpose of adding antioxidants is to prevent excessive oxidation of carbon materials. Metal silicon powder and metal aluminum powder are usually used as antioxidants. Plasticizers generally use plastic clay. The purpose of adding impregnants is to allow silicon carbide and carbon materials to be well mixed with oxide refractory materials. Adding shrinkage inhibitors is to prevent excessive shrinkage during use, which may cause cracks in the groove lining. Generally, fine silica particles can be used as shrinkage inhibitors.
At present, the high-aluminum-silicon carbide-carbon ramming materials used in the iron troughs of medium and small blast furnaces have gradually transitioned from the baking type to the non-baking type. The advantage of the non-baking type ramming material is that it can save time for repairing the groove, and it can also avoid excessive oxidation of the carbon material during the baking process, which reduces the resistance of the groove lining to slag penetration and corrosion.
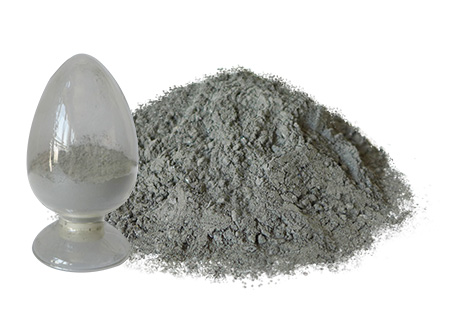
How to Double the Effect of High-Aluminum High-Temperature Resistant Ramming Materials?
In high-aluminum high-temperature resistant ramming materials, corundum powder is added to improve the matrix grade to improve its performance. The high-aluminum refractory high-temperature ramming materials added with zircon powder have a decomposition temperature of 1670°C to 1540°C due to impurities in zircon, and decompose into ZrO2 and SiO2. At high temperatures, the former forms baddeleyite, and the latter forms mullite with Al2O3. These two refractory minerals intersect with corundum or mullite, strengthen the organizational structure, and improve strength and corrosion resistance. At the same time, due to the volume effect, the shrinkage of the material is compensated and the anti-flaking property is enhanced. In high-aluminum or magnesia refractory high-temperature ramming materials, chromite is added, and chrome corundum or magnesia-chrome spinel can be generated at high temperatures. Even if these two minerals are not generated, corundum, magnesia and chromite are used as the skeleton and the silicate phase is filled to form a better organizational structure and bonding phase. It is conducive to the improvement of performance.
However, the amount of chromite should not be too much, otherwise the load softening temperature and strength of the refractory and high temperature ramming material will be reduced. Tests show that the amount of chromite in the magnesia-chromium refractory high-aluminum high-temperature ramming material should not exceed 30%, and the appropriate amount is 10-20%. This is mainly due to the excessive impurities brought in by the chromite. At the same time, the chromite is added in the form of aggregate, and the pre-synthesized magnesia-chromium sand fine powder should be added to the matrix to increase the degree of sintering and reduce volume expansion. In order to improve the performance of the magnesia-chromium refractory and high temperature ramming material, sodium hexametaphosphate and phosphate composites should be used, and metal aluminum powder and metal iron powder should be added to improve the medium temperature strength. With the increase in the amount of phosphate binder, the compressive strength after burning is also improved, and its amount is about 3%.
In the high-aluminum refractory and high-aluminum high-temperature ramming material, kyanite minerals can also be added. With the help of high-temperature decomposition, mullite can be formed and a volume expansion effect can be produced to offset the partial volume shrinkage of high-aluminum high-temperature resistant ramming materials, which is beneficial to the improvement of performance. The grade of kyanite family minerals has a great influence on the performance of refractory high-aluminum high-temperature resistant ramming materials. Therefore, its concentrate should be added, and the dosage is generally 15~35%. Refractory aggregates and powders are made from secondary alumina clinker, and the maximum particle size of aggregates is 5mm. The mass ratio of coarse and fine aggregates is 1:1. Suzhou mud is used as a plasticizer, and a water glass solution with a specific gravity of 1.38 is used as a binder. After adding kyanite family minerals, there is no obvious effect on the strength and load softening temperature of refractory high-aluminum high-temperature resistant ramming materials; the linear change after burning changes from linear contraction to linear expansion. That is, it shows the expansion agent effect of this type of material.
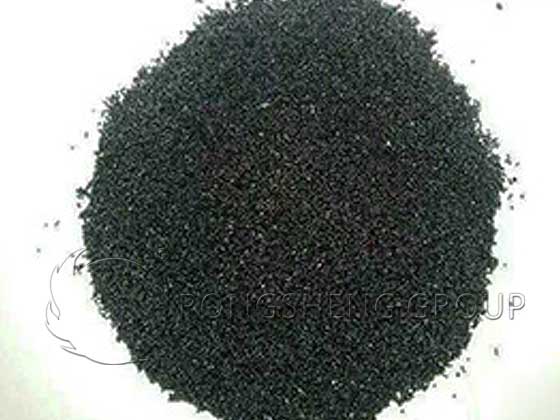
It should be pointed out that kyanite works very well as an expansion agent material. The linear change after burning at 1400℃ increases from negative 0.4% to positive 1.6%. In addition, there are also aluminate cement high-aluminum and corundum high-temperature resistant ramming materials, periclase cement magnesium high-temperature resistant ramming materials and phosphoric acid or phosphate high-temperature resistant ramming materials, which have also achieved good results. In order to facilitate users, refractory material manufacturers add preservatives to the refractory high-temperature resistant ramming materials and mix them evenly. Then put them into plastic bags and seal them. They can be stored for 3 to 6 months and still have plasticity for ramming construction, and their performance has no obvious decline. This kind of high-aluminum high-temperature resistant ramming material is also called plastic refractory high-temperature resistant ramming material.
Rongsheng Refractory Factory
Please choose Rongsheng Refractory Factory to buy high-quality high-alumina refractory ramming materials. Our environmentally friendly fully automatic monolithic refractory production line specializes in providing high-quality monolithic refractory products for monolithic refractory linings. Rongsheng’s refractory products have been sold to more than 120 countries around the world, such as South Africa, Chile, Egypt, Colombia, Uzbekistan, Italy, Indonesia, Ukraine, Hungary, Spain, Kenya, Syria, Zambia, Oman, Venezuela, India, Peru, the United States, Ethiopia, etc. Our comprehensive customer service protects the rights and interests of customers and provides guarantees for the long-life and efficient operation of high-temperature industrial furnace linings. Contact us for free solutions and quotes.