Self-baked carbon bricks and pre-baked carbon bricks have their own advantages and disadvantages in the use of ore-fired furnaces, and there are precedents of success and failure. Since self-baked carbon bricks are now mostly used in calcium carbide furnaces, while pre-baked carbon bricks are mostly used in ferroalloy furnaces. Ferroalloys have a larger melt density than calcium carbide, which will cause greater erosion of the carbon bricks at the bottom of the furnace, and the probability of bottom penetration will be greater. At present, there are few cases of self-baked carbon bricks being used in large ferroalloy furnaces, and the risk of self-baked carbon blocks in the sintering process is also very high. Therefore, it is not possible to judge that self-baked carbon bricks are definitely better than pre-baked carbon bricks based on the small number of self-baked bottom penetration accidents in the market.
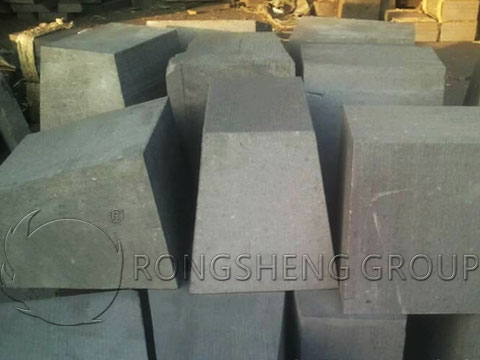
Comparison between self-baked carbon bricks and pre-baked carbon bricks | ||
Items | Self-baked carbon bricks | Pre-baked carbon bricks |
Advantages | The bonding seam has high strength after sintering, and the furnace bottom can be sintered into a whole. | The carbon block has high strength and density, the sintering quality of the carbon block can be measured, and the risk can be controlled. |
Disadvantages | Easy to oxidize, the sintering process of the carbon block is risky, and the furnace operation process is complicated. | The bonding seam has low strength after sintering. |
The binder pitch in the self-baking carbon brick is easy to oxidize in the unsintered state, so many manufacturers who tried to use self-baking carbon bricks had carbon brick oxidation accidents. According to market surveys and analysis, these manufacturers used to use pre-baked carbon bricks. After changing to self-baking carbon bricks, they still operated according to the pre-baked carbon brick baking process. “Only changing the carbon bricks without changing the process” does not provide enough protection for the self-baking carbon bricks. Therefore, it is not possible to simply judge that pre-baked carbon bricks are better than self-baking carbon bricks because self-baking carbon bricks are easy to oxidize. Rongsheng Refractory Factory supplies high-quality carbon bricks. Contact Rongsheng for free samples and quotations.
-
Light seam paste of carbon bricks
From the market survey, it can be seen that a large number of furnace bottom penetration accidents occur at the joints between carbon bricks. None of the more than 20 manufacturers we investigated had bottom penetration from carbon bricks, but all of them penetrated the carbon blocks after molten iron penetrated from the seam paste. The density of seam paste is smaller than that of formed carbon bricks, and the seam of carbon bricks after sintering is also the weakest link of the entire furnace bottom. The quality of the paste here determines the life of the entire submerged arc furnace.
More manufacturers have higher requirements for carbon bricks and pay more attention to them, but not enough attention to seam paste. Changing bricks without changing paste is an important reason why the life of the furnace bottom cannot be improved.
-
Heavy carbon material quality and light refractory brick quality
In the market survey, we found that because carbon materials are in direct contact with molten iron, the bottom penetration mostly occurs in the carbon brick layer. Therefore, manufacturers generally pay more attention to carbon materials, but not enough attention to the quality of other refractory materials.
The temperature of the contact surface of carbon bricks and high-alumina bricks is as high as 1200~1500 degrees. At such high temperatures, there are high requirements for the refractoriness, load softening point, high-temperature creep and reburning line change rate of refractory materials. If the quality of refractory materials is not good, at the normal smelting furnace bottom temperature, the refractory materials will soften and deform, causing the stability of the masonry to decrease or be damaged. Due to the qualitative change and deformation of the refractory masonry, the insulation capacity is reduced, the heat flow of the furnace bottom is increased, and the deformation of the masonry causes the structure of the furnace lining to crack and damage. It is bound to cause the furnace bottom to overheat, the furnace bottom steel plate to turn red and deform, and even the smelting products and melt to drill through the furnace bottom.
However, bottom penetration accidents caused by problems with refractory bricks are not easy to detect, and carbon bricks often become the “scapegoat” because they are in the front.
-
Emphasis on material quality over masonry quality
After the furnace materials are selected, the quality of masonry is the main factor that determines the life of the furnace body. A qualified construction team should be selected for furnace construction. The following points should be noted when building the furnace:
3.1 Brick selection
There is always a certain size error in the processing of carbon bricks. Due to the influence of the precision of the processing equipment, the vertical angle of carbon bricks is difficult to be less than 0.3°. Even if the carbon bricks are pre-laid by the manufacturer in advance, a process of picking bricks is still required due to the change of the masonry platform.
3.2 Stuffing
Generally speaking, the softening point of the seam paste is too low, and the coking value of the seam paste after sintering is also low. In this case, the seam paste with a low softening point that only considers the construction effect is not suitable for the masonry of the ore-heating furnace. In order to improve the ramming effect of the paste, the paste still needs to be heated when the ambient temperature is slightly lower. When heating, it cannot be heated quickly with a large fire, and a slow and stuffy method with a small fire should be adopted. If necessary, the construction surface also needs to be heated.
3.3 Ramming
The ramming density of the joint paste is the key to the life of the submerged arc furnace. The ramming layer should not be greater than 100mm, and the ramming density should be greater than 1.55g/cm3.
-
Focus on masonry and light on furnace baking
The masonry furnace contains certain volatiles and moisture, and there are certain gaps during the ramming process. After the furnace is baked, it can be melted and coked to form a dense whole, which increases the life of the furnace lining. However, in our investigation, it was found that carbon brick oxidation caused by furnace baking accounted for more than 20% of furnace lining accidents.
External factors affecting the life of the furnace lining include the influence of operation, such as raw material type, charging method, process reaction and furnace operation rate.
If the furnace charge is not refined and contains more impurities, more slag will be formed. The slag not only consumes electricity but also easily causes excessive slag accumulation in the furnace, and the bottom of the furnace rises and other bad furnace conditions will affect the life of the furnace lining.