High-strength wear-resistant castables are composed of high-strength aggregates and powder mineral additives. After optimized formula design, it has the advantages of minimal wear loss, high strength, arbitrary controllable shape, strong integrity, simple construction, and good construction performance. Due to the addition of high molecular polymers, the base concrete is firmly bonded. HIGH STRENGTH CASTABLE. Rongsheng’s high-strength wear-resistant castables are cheap and are the preferred material for construction sites with wear-resistant requirements.
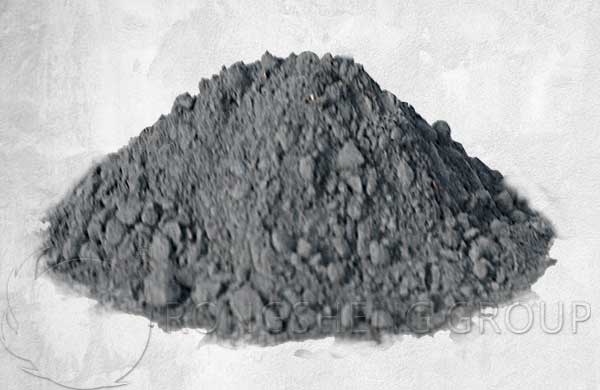
Wear Resistance of Rongsheng Castables Refractory
High-Aluminum Refractory Castables
High-Strength Index ★★★★
High-aluminum refractory castables are made of high-aluminum aggregate, high-aluminum fine powder, micro-silica powder, and high-aluminum cement through reasonable machine matching, and external water reducer. It has good high-temperature performance and is used in hardware, smelting, chemical industry, non-ferrous metals, and other industries.
Corundum Wear-Resistant Castable
High Strength Index ★★★★★★★
Corundum wear-resistant castable is a wear-resistant castable made of high-aluminum aggregate, corundum, α-alumina powder, and the appropriate amount of explosion-proof fiber through reasonable grading and pure calcium aluminate cement. Corundum wear-resistant castable has high strength, good wear resistance, thermal shock resistance, and good erosion resistance.
Silicon carbide castables have particularly good wear resistance. As long as they are used in the right places, their service life will be more than 50% longer than that of ordinary low-cement castables. Silicon carbide wear-resistant castables are also a kind of refractory castables with good wear resistance. Adding SiC to the castable increases its strength and wear resistance. Especially the high-temperature performance is enhanced. Silicon carbide castables can be used in high temperature and harsh conditions.
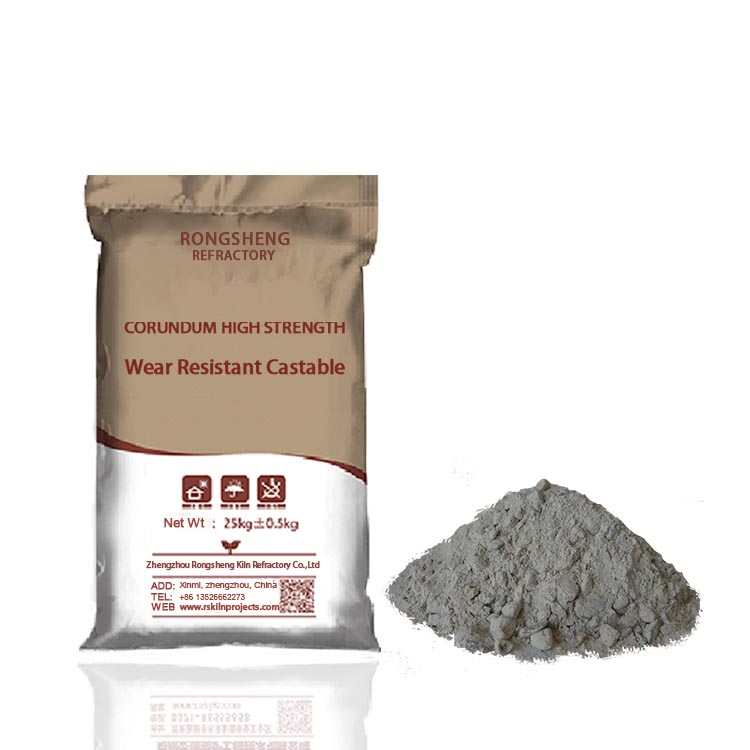
Wide Application Range of Castables Refractory
Casables are a kind of refractory materials that can be used at a high rate during boiler construction. With the development of boiler production conditions, they are now widely used in the lining construction of major boilers. It is because the service life and construction process of castables are relatively simple, which is very popular. So, how wide is the application range of castables?
Casable application range. With the improvement of the requirements for the integrity of the lining, the application range of castables is getting wider and wider. During the construction of refractory furnace linings, a large part of them will be used in the metallurgical industry. Amorphous refractory materials are an important foundation for the development of metallurgy. The main reason is that many new kilns have also appeared. The improvement of the quality of amorphous refractory materials is inseparable from new products and new boilers, and they complement each other. More importantly, the output of refractory castables is gradually increasing every year. The demand for castables is also increasing, so that the application range of castables is gradually expanding to high-temperature smelting furnaces. Moreover, refractory castables are no longer a single variety. Instead, with the development of boilers, many new refractory products and new construction methods have been developed. Some refractory castable products can be made into precast blocks refractory before leaving the factory. They are also very effective in high-temperature kilns such as ironmaking and steelmaking.
The purity and performance of refractory castables are now being improved. The development of new varieties has expanded the application scope of castables, and the output is also increasing. Refractory castables can extend the life of furnace linings and reduce material and energy consumption in terms of performance and quality. Therefore, they play a greater role in high-temperature thermal equipment. With the development of amorphous refractory materials, varieties are also changing. Refractory ramming materials and refractory plastics require manual stirring, the labor intensity is very high, the construction process is slow, and there is a trend of being replaced by refractory castables, and the output is also declining. Now, in order to improve the construction process and application needs, in order to extend the service life of power station boilers, thermal kilns, etc., refractory spray coatings, repair materials, and coatings are also developing.
Castables are the best among amorphous refractory materials, many of which are advanced refractory materials developed based on low-cement refractory castables and clay refractory castables. The emergence of new varieties has not only greatly increased the scope of use of castables, but also increased the application areas of castables. Amorphous refractory materials have a great development and are also very complete in variety. High-quality refractory manufacturers, Rongsheng refractory manufacturers.
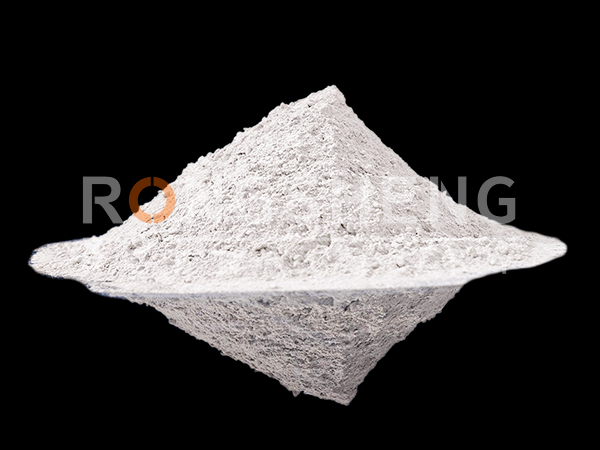
Why does the Refractory Castable become Hard, Sticky, and Non-Flowing?
The particle gradation of refractory castables is very important. During the construction of refractory castables, if the gradation is too tight, it will become hard and sticky when stirred. And it will not flow at the construction site, making it impossible to carry out construction.
In the production process of refractory castables, particle gradation is very important. The general ratio of castable particles to powder is 65:35 or 70:30. There are also ratios of 73:27 or even 74:26. However, no matter what the ratio is, the main reason for the lack of fluidity is unreasonable gradation.
Some castable manufacturers use cliff-like particle grading when producing refractory concrete. What is cliff-like particle grading? It is a combination of some particles separated in the middle. No matter what kind of particles have different expansion coefficients, the method of separating the particle ratio can increase the fluidity of the refractory castable. The castable itself is an application product. It can only be used reasonably and for a long period of time. Therefore, it is unscientific to judge the usability of the product based on a small proportion of products in the laboratory.
The strict particle grading can increase the density of the castable. The difference between castables and refractory bricks is that larger cracks will appear in actual use. Tiny cracks do not affect its use effect. Large particles or cliff-like particle ratios do not affect its stress resistance or the generation of cracks. For example, adding a certain proportion of explosion-proof fiber is to make it easier to discharge the water in the castable, so that the mid-term and late-term use of the castable is better.
The density of refractory castables is very high, but the thermal shock is not very good. Therefore, unreasonable particle grading will cause the castable to become hard and sticky during construction, and it will not flow, making it impossible to use on-site. If it does not flow, you can add a retarder to disperse and slow down the setting. This also ensures that the castable can be constructed normally on-site.
In a word, the reason why refractory castables become hard, sticky, and non-flowing is because of unreasonable particle grading.
Rongsheng High Strength Refractory Castable Manufacturer
To purchase high-quality monolithic refractory lining products, please choose a strong refractory manufacturer. Rongsheng Refractory Manufacturer is a strong manufacturer and seller of refractory materials. Our refractory products have been sold to more than 120 countries around the world. For example, South Africa, Chile, Egypt, Colombia, Uzbekistan, Italy, Indonesia, Ukraine, Hungary, Spain, Kenya, Syria, Zambia, Oman, Venezuela, India, Peru, the United States, Ethiopia, etc. And our refractory products are of reliable quality and competitive price. Comprehensive customer service. Contact us for free samples and quotes.